Cut-out and drilling is the third stage of the installation process for injection quills. During this stage, the following tasks are performed:
- Cutting a hole in the pipe: A hole is cut in the pipe at the determined location for the injection quill.
- Drilling a hole in the pipe wall: A hole is drilled in the pipe wall for the process line to pass through and connect to the injection quill.
- Verifying hole size and location: The size and location of the holes are verified to ensure that the injection quill and process line will fit and connect properly.
The purpose of the cut-out and drilling stage is to create the necessary openings in the pipe for the injection quill and process line to be installed. This stage is critical in ensuring that the injection quill is correctly positioned and connected to the process line.
Cutting a hole in the pipe
Cutting a hole in the pipe is an important step in the Cut-out and Drilling stage of the installation process for injection quills. The goal of this step is to create an opening in the pipe where the quill can be inserted and secured. This opening must be precise and of the correct size and shape to ensure a secure and leak-free installation.
To cut the hole in the pipe, various tools and techniques may be used, such as a hole saw, a cutting torch, or a band saw. The choice of tool will depend on the material of the pipe and other factors, such as its thickness and location. It is important to follow the manufacturer’s specifications and guidelines for the specific type of injection quill being installed to ensure that the hole is cut correctly.
Once the hole has been cut, it is important to remove any sharp edges or burrs that could damage the quill or cause leaks. This can be done using a file, sandpaper, or other tools. After the hole has been cut and prepared, the next step in the installation process can proceed.
It is important to note that cutting a hole in a pipe can be a dangerous task that requires specialized training and equipment. It should only be performed by experienced professionals who have the necessary knowledge and skills to do so safely.
Drilling a hole in the pipe wall
Drilling a hole in the pipe wall is an important step in the Cut-out and Drilling stage of the installation process for injection quills. The goal of this step is to create an opening in the pipe wall where the quill can be inserted and secured. This opening must be precise and of the correct size and shape to ensure a secure and leak-free installation.
To drill a hole in the pipe wall, various tools and techniques may be used, such as a drill press, a hand-held drill, or a specialized drilling machine. The choice of tool will depend on the material of the pipe and other factors, such as its thickness and location. It is important to follow the manufacturer’s specifications and guidelines for the specific type of injection quill being installed to ensure that the hole is drilled correctly.
Once the hole has been drilled, it is important to remove any sharp edges or burrs that could damage the quill or cause leaks. This can be done using a file, sandpaper, or other tools. After the hole has been drilled and prepared, the next step in the installation process can proceed.
It is important to note that drilling a hole in a pipe wall can be a dangerous task that requires specialized training and equipment. It should only be performed by experienced professionals who have the necessary knowledge and skills to do so safely.
Verifying hole size and location
Verifying the hole size and location is a crucial step in the Cut-out and Drilling stage of the installation process for injection quills. The goal of this step is to ensure that the hole created in the pipe wall is of the correct size and in the correct location to allow for a secure and leak-free installation of the quill.
To verify the hole size and location, various tools and techniques may be used, such as a template, a measuring tape, or a specialized gauging device. The specific tools and techniques used will depend on the manufacturer’s specifications and guidelines for the specific type of injection quill being installed.
It is important to measure the hole accurately and compare the measurements to the manufacturer’s specifications to ensure that it is the correct size. The location of the hole must also be verified to ensure that it is in the correct position relative to the other components in the system.
If the hole is not the correct size or in the correct location, it may need to be re-drilled or adjusted. It is important to take the time to verify the hole size and location to ensure that the quill can be inserted and secured properly.
Once the hole size and location have been verified and found to be correct, the next step in the installation process can proceed. However, if any issues are discovered during the verification process, they must be addressed before the installation can proceed to ensure a successful and long-lasting installation.
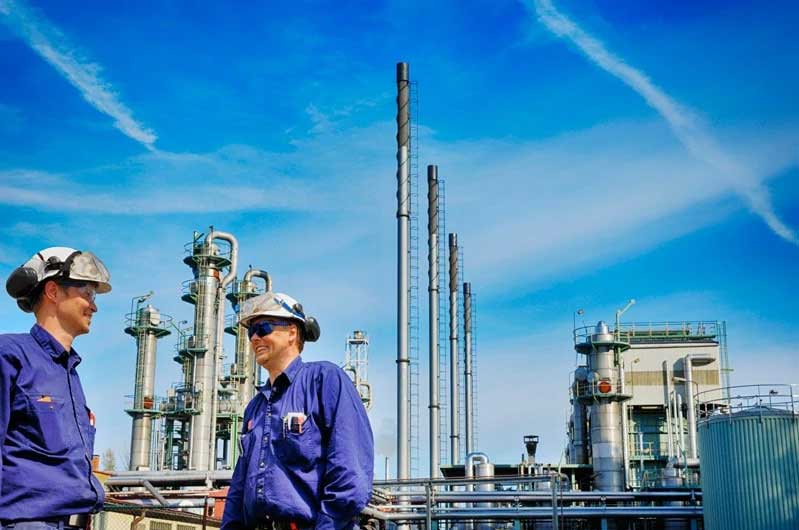
Contact us
Crystal Industrial Syndicate
Phone : +91-22-27563850
Fax: +91-22-67939439
www.crystalindustrial.in
sales@crystalindustrial.in
Crystal Industrial Syndicate from India, manufactures a variety of custom injection quills for a range of industrial processes. Our world-class chemical injection quills are manufactured in India comply with the world’s most stringent certifications. We have clients the world over, from Europe and North America to Africa and the Middle East. Please contact us for details about how we can meet your injection quills requirements. Contact us
Copyright © 2023 by Crystal Industrial Syndicate Pvt Ltd. All rights reserved. www.crystalindustrial.in