Maintenance and upkeep of injection quills are crucial for ensuring that the quills continue to operate efficiently and effectively in rubber and plastics manufacturing. Regular maintenance is necessary to keep the quills in good working condition and to ensure that they continue to deliver the raw material efficiently and effectively.
Some of the key maintenance and upkeep tasks that should be performed on injection quills include: Cleaning, Inspections, Lubrication, Calibration, Replacement of worn parts.
Lubrication
Lubrication is an important aspect of the maintenance and upkeep of injection quills in rubber and plastics manufacturing. Lubrication is necessary to ensure that the quills continue to operate smoothly and efficiently, and to prevent any wear or damage to the internal parts of the quill.
The lubrication process typically involves applying a suitable lubricant to the moving parts of the quill, such as the nozzle, the barrel, the sprue bushing, and the seals. It’s important to use a lubricant that is suitable for the type of raw material being used and the quill’s material composition.
It’s also important to lubricate the quill at the correct intervals, depending on the frequency of use, the operating temperature, and other factors. Over lubrication or using an inappropriate lubricant can cause damage to the quill, or affect the quality of the final product.
It is recommended to have a lubrication schedule in place, to ensure that the quills are lubricated at regular intervals. This will help to prevent any wear or damage to the internal parts of the quill, and keep it in good working condition.
Overall, lubrication is a crucial aspect of the maintenance and upkeep of injection quills in rubber and plastics manufacturing. Regular lubrication can help to ensure that the quills continue to operate smoothly and efficiently, and prevent any wear or damage to the internal parts of the quill, ultimately helping to increase the efficiency and productivity of the manufacturing process.
Calibration
Calibration is an important aspect of the maintenance and upkeep of injection quills in rubber and plastics manufacturing. Calibration is necessary to ensure that the quills are delivering the raw material at the correct flow rate and pressure, which is essential for maintaining the quality of the final product and the efficiency of the manufacturing process.
The calibration process typically involves measuring the flow rate and pressure of the raw material being delivered by the quill and making any necessary adjustments to the quill’s settings. It is important to ensure that the quill is calibrated to the specific requirements of the manufacturing process and the type of raw material being used.
It’s also important to calibrate the quill at the correct intervals, depending on the frequency of use, the operating temperature, and other factors. It can help to prevent any issues that may affect the quill’s performance and the final product quality.
It is recommended to have a calibration schedule in place, to ensure that the quills are calibrated at regular intervals. This will help to ensure that the quills are delivering the raw material at the correct flow rate and pressure and help to maintain the quality of the final product and the efficiency of the manufacturing process.
Overall, calibration is a crucial aspect of the maintenance and upkeep of injection quills in rubber and plastics manufacturing. Regular calibration can help to ensure that the quills are delivering the raw material at the correct flow rate and pressure, which is essential for maintaining the quality of injection quills.
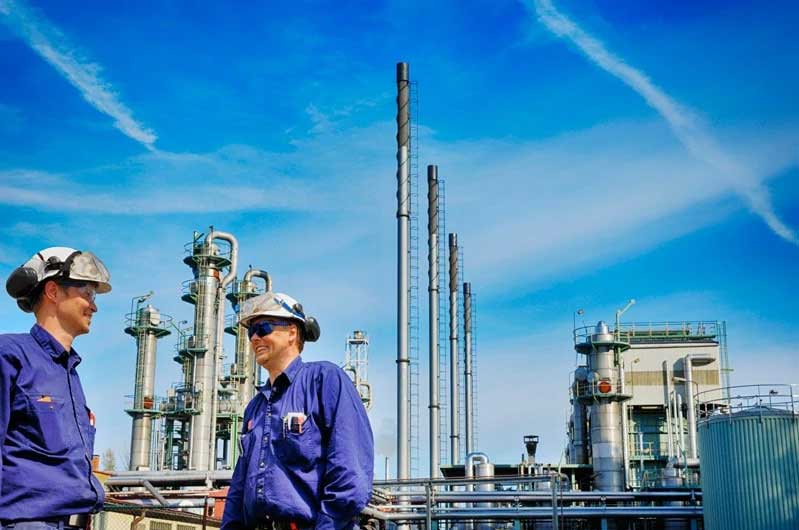
Contact us
Crystal Industrial Syndicate Pvt Ltd.
Telephone : +91-22-27563850 |
Telefax : +91-22-67939439
sales@crystalindustrial.in
Replacement of worn parts
Replacement of worn parts is an important aspect of the maintenance and upkeep of injection quills in rubber and plastics manufacturing. As the quills are subjected to high temperatures, pressures, and chemical properties of the raw material, it is important to replace worn parts as soon as they show signs of wear in order to maintain the quill’s performance and prevent any leakage or blockage that can cause material wastage or damage to the quill.
Some of the common worn parts that may need to be replaced include the nozzle, the seals, and the sprue bushing. These parts are exposed to the raw material and are most likely to wear out first.
It’s important to use replacement parts that are compatible with the quill, and that are suitable for the type of raw material being used and the quill’s material composition. Using the wrong replacement parts can cause damage to the quill or affect the quality of the final product.
It is recommended to have a replacement schedule in place, to ensure that worn parts are replaced at regular intervals. This will help to prevent any issues that may affect the quill’s performance and the final product quality.
Overall, replacement of worn parts is a crucial aspect of the maintenance and upkeep of injection quills in rubber and plastics manufacturing. Regular replacement of worn parts can help to maintain the quill’s performance and prevent any leakage or blockage that can cause material wastage or damage to the quill and ultimately help to increase the efficiency and productivity of the manufacturing process.
Crystal Industrial Syndicate from India, manufactures a variety of custom injection quills for a range of industrial processes. Our world-class chemical injection quills are manufactured in India comply with the world’s most stringent certifications. We have clients the world, from Europe and North America to Africa and the Middle East. Please contact us for details about how we can meet your injection quills requirements. Contact us
Copyright © 2023 by Crystal Industrial Syndicate Pvt Ltd. All rights reserved. www.crystalindustrial.in