Chemical compatibility is another important factor to consider when selecting an injection quill. The injection quill must be made from materials that are compatible with the chemical being injected to prevent reactions, corrosion, or damage to the injection quill.
When selecting materials for the injection quill, it is important to consider the properties of the chemical being injected, such as its pH, temperature, and concentration. The injection quill must be able to withstand these properties without degrading, reacting, or corroding.
Some chemicals may require injection quills made from specialized materials such as Teflon, Kynar, or Hastelloy. These materials have properties that make them resistant to certain chemicals or conditions and are commonly used for chemical injection applications.
Additionally, the design of the injection quill may need to be modified for certain chemical applications. For example, injection quills used for corrosive chemicals may need to be coated or lined with a chemical-resistant material to prevent damage to the injection quill.
Overall, chemical compatibility is a critical factor to consider when selecting an injection quill. It is important to consult with a qualified professional to ensure that the injection quill is made from the appropriate materials and designed to prevent chemical reactions or damage. By selecting the right injection quill, the chemical injection process can be conducted safely and effectively, without risk of contamination or equipment failure.
Examples of chemicals that may require specialized injection quills (corrosive, abrasive, high viscosity)
There are a variety of chemicals used in industrial processes that may require specialized injection quills due to their corrosive, abrasive, or high viscosity properties. Here are some examples:
- Corrosive chemicals: Corrosive chemicals are highly reactive and can cause damage or degradation to injection quills made from certain materials. Examples of corrosive chemicals include hydrochloric acid, sulfuric acid, and caustic soda. Injection quills used for these chemicals may need to be made from specialized materials such as Teflon, Kynar, or Hastelloy.
- Abrasive chemicals: Abrasive chemicals are substances that can cause erosion or wear to injection quills, particularly those made from metals. Examples of abrasive chemicals include slurries, sand, and cement. Injection quills used for these chemicals may need to be made from materials such as ceramic or tungsten carbide, which are more resistant to abrasion.
- High viscosity chemicals: High viscosity chemicals are substances with a thick or viscous consistency that can make injection more difficult. Examples of high viscosity chemicals include heavy oils, resins, and adhesives. Injection quills used for these chemicals may need to have a larger diameter to accommodate the thicker consistency of the chemical.
It is important to carefully evaluate the properties of the chemicals being injected to determine if specialized injection quills are required. Using the wrong type of injection quill can result in equipment failure, contamination, or safety hazards. Consulting with a qualified professional can help ensure that the right injection quill is selected for the chemical injection process.
Material properties and their impact on chemical compatibility
The material properties of injection quills play an important role in their chemical compatibility. Different materials have varying levels of resistance to chemical corrosion, temperature, pressure, and other factors that can impact the integrity and longevity of the injection quill.
Here are some material properties and their impact on chemical compatibility:
- Stainless steel: Stainless steel is a commonly used material for injection quills due to its durability, strength, and resistance to corrosion. It is often used for applications involving water, oil, and mild chemicals. However, stainless steel may not be suitable for more corrosive or high-temperature applications.
- Teflon (PTFE): Teflon is a high-performance polymer that is known for its chemical resistance and non-stick properties. It is often used for applications involving highly corrosive chemicals, such as hydrochloric acid and sulfuric acid. Teflon is also resistant to high temperatures, making it a good choice for applications involving hot chemicals.
- Kynar (PVDF): Kynar is a thermoplastic material that is known for its excellent chemical resistance, particularly to strong acids and bases. It is often used for applications involving aggressive chemicals and high temperatures.
- Hastelloy: Hastelloy is a nickel-based alloy that is known for its exceptional resistance to corrosion and high-temperature applications. It is often used for applications involving highly corrosive chemicals, such as hydrofluoric acid, and is well-suited for harsh environments.
- Ceramic: Ceramic injection quills are used for applications involving abrasive chemicals or high pressure. Ceramics are extremely hard and durable, making them suitable for handling abrasive chemicals such as slurries, sand, and cement.
When selecting the material for an injection quill, it is important to consider the chemical properties of the fluid being injected and the conditions under which the injection will occur. In some cases, a combination of materials may be required to ensure the injection quill is compatible with the chemical being used.
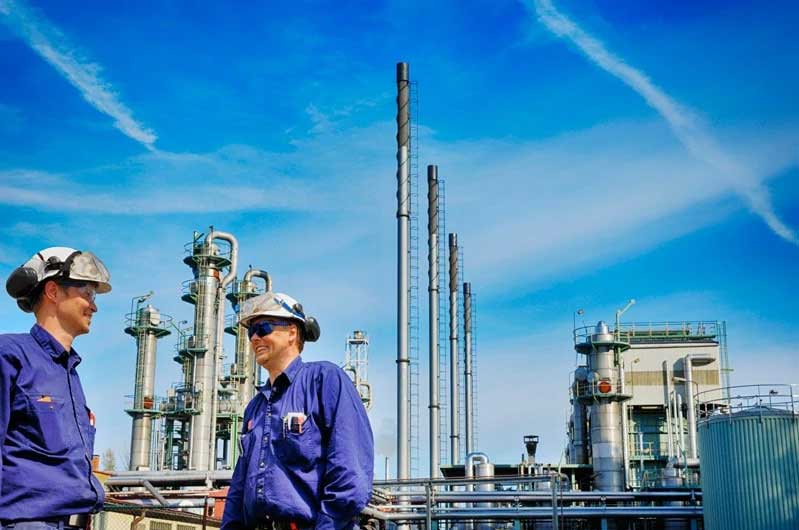
Contact us
Crystal Industrial Syndicate
Phone : +91-22-27563850
Fax: +91-22-67939439
www.crystalindustrial.in
sales@crystalindustrial.in
Crystal Industrial Syndicate from India, manufactures a variety of custom injection quills for a range of industrial processes. Our world-class chemical injection quills are manufactured in India comply with the world’s most stringent certifications. We have clients around the world, from Europe and North America to Africa and the Middle East. Please contact us for details about how we can meet your injection quills requirements. Contact us
Copyright © 2023 by Crystal Industrial Syndicate Pvt Ltd. All rights reserved. www.crystalindustrial.in