The body of injection quill
The body of these injection quills is an important component that must be durable and able to withstand the harsh environments found in the oil and gas industry.
The body of the injection quill typically consists of a cylindrical barrel made of metal, such as stainless steel or brass, which provides the necessary strength and resistance to corrosive fluids and high pressure environments. The body is designed to fit into the pipeline, with flanges or other connecting mechanisms allowing for secure attachment and proper fluid flow.
In addition to the barrel, the body of the injection quill may also include a control valve that regulates the flow of the fluid being injected and a check valve that prevents backflow. Some models may also feature a differential pressure gauge to monitor the pressure of the fluid being injected and ensure that it is being delivered at the correct rate.
The body of the injection quill must be designed with safety in mind, as well as being easy to install and maintain. It is essential for the body to be manufactured to exacting specifications in order to ensure consistent, accurate, and safe delivery of the fluid into the pipeline. The body of the injection quill is a critical component in the operation of oil and gas pipelines and must be able to perform reliably in order to protect the integrity of the pipeline and the environment.
The INLET of injection quill
The inlet of an injection quill is the component that connects the fluid source to the body of the device and is responsible for delivering the fluid into the pipeline. In the oil and gas industry, the inlet of an injection quill plays a critical role in delivering fluid additives into the pipeline to help maintain its integrity and prevent corrosion, scaling, and other problems.
The inlet of the injection quill is typically made of metal, such as stainless steel or brass, which provides strength and resistance to corrosive fluids and high pressure environments. The inlet is designed to connect to the fluid source, such as a tank or pump, and may include a fitting or connector to ensure a secure and leak-free connection.
In addition to the physical connection, the inlet may also include a control valve to regulate the flow of fluid into the body of the injection quill. This valve helps to ensure that the fluid is delivered at the correct rate and pressure, which is essential for the effective operation of the pipeline.
The inlet of the injection quill must be designed to meet specific industry standards, such as those set by the American Petroleum Institute (API), in order to ensure the safety and reliability of the system. It must also be easy to install and maintain, and must be able to withstand the harsh environments found in the oil and gas industry. The inlet of the injection quill is an essential component in the operation of oil and gas pipelines and must perform reliably to ensure the longevity and integrity of the pipeline.
The OUTLET of injection quill
The outlet of an injection quill is the component that delivers the fluid from the body of the device into the pipeline. In the oil and gas industry, the outlet of an injection quill is crucial for ensuring the effective delivery of fluid additives into the pipeline to maintain its integrity and prevent corrosion, scaling, and other problems.
The outlet of the injection quill is typically made of metal, such as stainless steel or brass, which provides strength and resistance to corrosive fluids and high pressure environments. The outlet is designed to connect to the pipeline and may include a fitting or connector to ensure a secure and leak-free connection.
In addition to the physical connection, the outlet may also include a check valve to prevent backflow of fluid into the body of the injection quill. This is an important safety feature that helps to prevent contamination of the fluid source and maintain the integrity of the pipeline.
The outlet of the injection quill must be designed to meet specific industry standards, such as those set by the American Petroleum Institute (API), in order to ensure the safety and reliability of the system. It must also be easy to install and maintain, and must be able to withstand the harsh environments found in the oil and gas industry. The outlet of the injection quill is an essential component in the operation of oil and gas pipelines and must perform reliably to ensure the longevity and integrity of the pipeline.
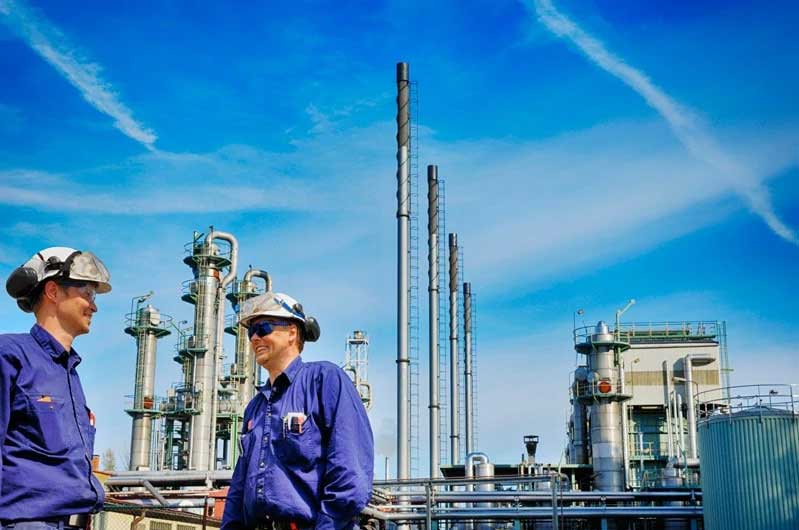
Contact us
Crystal Industrial Syndicate
Phone : +91-22-27563850
Fax: +91-22-67939439
www.crystalindustrial.in
sales@crystalindustrial.in
Crystal Industrial Syndicate from India, manufactures a variety of custom injection quills for a range of industrial processes. Our world-class chemical injection quills are manufactured in India comply with the world’s most stringent certifications. We have clients the world over, from Europe and North America to Africa and the Middle East. Please contact us for details about how we can meet your injection quills requirements. Contact us
Copyright © 2023 by Crystal Industrial Syndicate Pvt Ltd. All rights reserved. www.crystalindustrial.in