Flow rate and injection point are important factors to consider when selecting an injection quill for chemical injection applications. Here is an overview of how these factors can affect the choice of injection quill:
- Flow rate: The flow rate of the chemical being injected is an important consideration when selecting an injection quill. The size and shape of the quill can affect the flow rate of the chemical, and choosing a quill that is too small or too large for the flow rate can result in poor injection performance or damage to the quill or injection system.
In general, it is important to choose an injection quill that is appropriately sized for the flow rate of the chemical being injected. This may involve selecting a quill with a larger or smaller diameter, or choosing a quill with a different length or configuration that is better suited to the flow rate.
- Injection point: The location where the chemical is injected into the process stream is also an important consideration when selecting an injection quill. The injection point can affect the distribution of the chemical in the process stream, as well as the rate at which the chemical is mixed with the process fluid.
In general, it is important to choose an injection quill that is designed to inject the chemical at the appropriate location in the process stream. This may involve selecting a quill with a specific shape or configuration that is designed to inject the chemical in a particular way, or choosing a quill with a specific injection point that is optimized for the specific application.
Overall, the flow rate and injection point are important factors to consider when selecting an injection quill for chemical injection applications. By choosing a quill that is appropriately sized and designed for the specific flow rate and injection point, it is possible to achieve optimal injection performance and ensure reliable, consistent results.
Flow rate
The flow rate of the chemical being injected is a critical factor to consider when selecting an injection quill. The flow rate refers to the volume of the chemical being injected per unit time, and it can have a significant impact on the performance of the injection system.
Choosing an injection quill that is too small for the flow rate can result in poor injection performance and inadequate mixing of the chemical with the process fluid. This can lead to uneven distribution of the chemical in the process stream, as well as reduced effectiveness of the chemical treatment.
On the other hand, choosing an injection quill that is too large for the flow rate can result in excessive pressure drop and turbulence, which can damage the quill or the injection system. This can also lead to poor injection performance and ineffective chemical treatment.
In general, it is important to select an injection quill that is appropriately sized for the specific flow rate of the chemical being injected. This may involve choosing a quill with a larger or smaller diameter, or selecting a quill with a different length or configuration that is better suited to the flow rate.
By choosing an injection quill that is designed for the specific flow rate, it is possible to achieve optimal injection performance and ensure reliable, consistent results in chemical injection applications.
Injection point
The injection point is another important factor to consider when selecting an injection quill. The injection point refers to the location in the process stream where the chemical will be injected, and it can have a significant impact on the effectiveness of the chemical treatment.
Choosing the right injection point depends on a variety of factors, including the specific chemical being injected, the process conditions, and the desired treatment objectives. In some cases, the chemical may need to be injected directly into the process stream, while in other cases, it may be more effective to inject the chemical at a specific location or point within the process.
The injection point can also affect the design of the injection quill itself. For example, if the chemical needs to be injected at a specific angle or direction, the quill may need to be designed with a specific orientation or configuration to achieve optimal results.
In general, it is important to consider the injection point when selecting an injection quill to ensure that the chemical treatment is effective and consistent. By choosing a quill that is designed for the specific injection point, it is possible to achieve optimal performance and ensure reliable results in chemical injection applications.
Common flow rate and injection point considerations
When selecting an injection quill, there are several common flow rate and injection point considerations that should be taken into account:
- Flow Rate: The flow rate of the process stream is an important consideration when selecting an injection quill. The quill must be designed to accommodate the flow rate of the process stream and deliver the chemical treatment at the desired rate. If the flow rate is too high, the chemical may not be properly dispersed, resulting in uneven treatment. If the flow rate is too low, the chemical may accumulate in one location and cause damage to the process equipment.
- Injection Point Location: The location of the injection point is also important. The injection point should be strategically located to ensure that the chemical treatment is effective and consistent. For example, injecting the chemical at a point where there is turbulence in the process stream can help to ensure that the chemical is evenly dispersed throughout the process. Alternatively, injecting the chemical at a point where there is low flow may result in the chemical accumulating in one location.
- Injection Point Orientation: The orientation of the injection point is also a consideration when selecting an injection quill. The quill must be designed to deliver the chemical treatment at the proper angle or direction to ensure that it is effectively dispersed throughout the process stream. For example, if the injection point is located at the top of a tank, the quill may need to be designed to deliver the chemical treatment in a downward direction to ensure that it reaches the bottom of the tank.
Overall, selecting an injection quill that is designed to accommodate the specific flow rate and injection point requirements of the application is crucial to achieving effective and consistent chemical treatment.
The orientation of the injection point is an important factor to consider when selecting an injection quill. The injection point orientation refers to the angle or direction at which the chemical treatment is delivered into the process stream. The injection point orientation can impact the effectiveness and consistency of the chemical treatment. Some common injection point orientations include: Radial Injection: Radial injection is a common injection point orientation that delivers the chemical treatment in a horizontal direction, perpendicular to the direction of the process stream. This orientation is often used in pipes or ducts where there is a high flow rate and the goal is to disperse the chemical treatment evenly throughout the process. Axial Injection: Axial injection is another common injection point orientation that delivers the chemical treatment in a vertical direction, parallel to the direction of the process stream. This orientation is often used in tanks or vessels where the goal is to distribute the chemical treatment evenly throughout the volume of the tank or vessel. Tangential Injection: Tangential injection is an injection point orientation that delivers the chemical treatment in a tangential direction, at an angle to the direction of the process stream. This orientation is often used in tanks or vessels where the goal is to create turbulence or mixing within the process stream to ensure that the chemical treatment is evenly dispersed throughout the volume of the tank or vessel. The injection point orientation is typically determined by the specific needs of the application, including the flow rate, tank or vessel design, and the desired level of chemical treatment. It is important to select an injection quill that is designed to accommodate the desired injection point orientation to ensure that the chemical treatment is effectively delivered and evenly dispersed throughout the process stream.
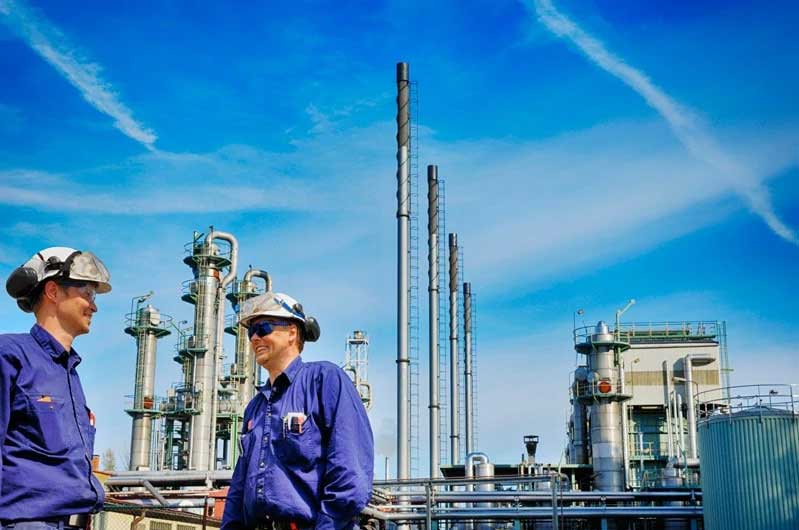
Contact us
Crystal Industrial Syndicate
Phone : +91-22-27563850
Fax: +91-22-67939439
www.crystalindustrial.in
sales@crystalindustrial.in
Crystal Industrial Syndicate from India, manufactures a variety of custom injection quills for a range of industrial processes. Our world-class chemical injection quills are manufactured in India comply with the world’s most stringent certifications. We have clients around the world, from Europe and North America to Africa and the Middle East. Please contact us for details about how we can meet your injection quills requirements. Contact us
Copyright © 2023 by Crystal Industrial Syndicate Pvt Ltd. All rights reserved. www.crystalindustrial.in