Advantages of Chemical injection quills with flow meters
Chemical injection quills with flow meters offer several unique advantages over other types of quills. Some of these advantages include:
- Accurate chemical dosing: Flow meters provide accurate measurements of the chemical flow rate, which ensures that the correct amount of chemical is injected into the system. This helps to improve the effectiveness of the chemical treatment and reduce waste.
- Real-time monitoring: Flow meters provide real-time monitoring of the chemical injection rate, which allows operators to detect any changes in the flow rate and make adjustments as needed. This helps to prevent over or underdosing and ensures that the system is operating optimally.
- Improved safety: Chemical injection quills with flow meters can help to improve safety by providing accurate and reliable chemical dosing. This helps to prevent over or underdosing, which can lead to safety hazards or equipment failure.
- Reduced maintenance: Flow meters can help to reduce maintenance requirements by providing early detection of any issues with the chemical injection system. This allows operators to identify and address problems before they become more severe, which can help to prevent downtime and reduce repair costs.
- Compliance with regulations: Flow meters can help companies comply with regulations by ensuring that the correct amount of chemical is injected into the system. This helps to prevent environmental contamination and protect public health.
Overall, chemical injection quills with flow meters offer several unique advantages that make them an attractive option for many industries. Their accurate chemical dosing, real-time monitoring, improved safety, reduced maintenance requirements, and compliance with regulations make them a popular choice for a wide range of applications.
Applications of Chemical injection quills with flow meters
Chemical injection quills with flow meters are used in various industries for different applications. Here are some common applications of chemical injection quills with flow meters:
- Water treatment: Chemical injection quills with flow meters are used in water treatment systems to inject precise amounts of chemicals into the water stream. The flow meters help to ensure accurate dosing and prevent under or overdosing, which can impact the effectiveness of the water treatment process.
- Oil and gas industry: Chemical injection quills with flow meters are used in the oil and gas industry to inject precise amounts of chemicals into the pipelines. This helps to prevent corrosion, scale buildup, and other issues that can lead to equipment failure. The flow meters help to ensure that the correct amount of chemical is injected, improving the effectiveness of the treatment.
- Food processing: Chemical injection quills with flow meters are used in the food processing industry to inject precise amounts of sanitizers and cleaning agents into the food processing equipment. The flow meters help to ensure accurate dosing and prevent contamination of the food.
- Chemical manufacturing: Chemical injection quills with flow meters are used in chemical manufacturing processes to inject precise amounts of chemicals into the reaction vessels. This helps to control the chemical reactions and ensure that the desired product is produced. The flow meters help to ensure accurate dosing and prevent waste.
- Water purification: Chemical injection quills with flow meters are used in water purification systems to inject precise amounts of chemicals into the water stream. The flow meters help to ensure accurate dosing and prevent under or overdosing, which can impact the effectiveness of the water purification process.
Overall, chemical injection quills with flow meters are used in various industries to inject precise amounts of chemicals into a system. The flow meters help to ensure accurate dosing, prevent waste, and improve the effectiveness of the treatment.
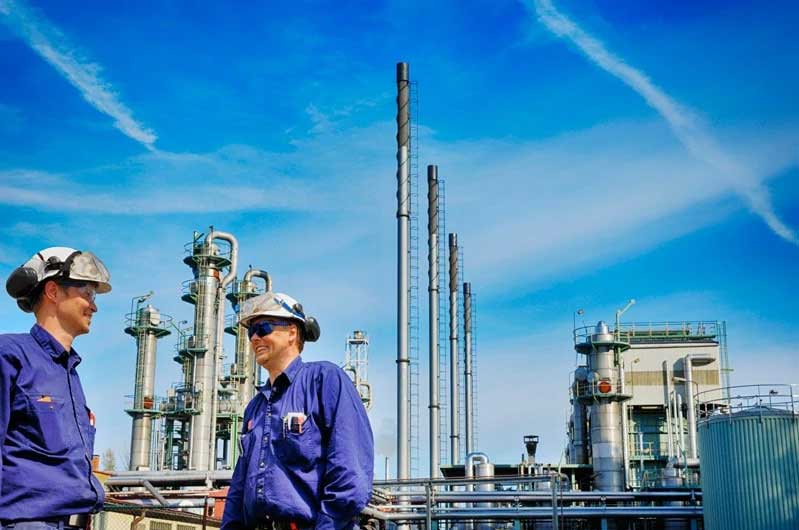
Contact us
Crystal Industrial Syndicate
Phone : +91-22-27563850
Fax: +91-22-67939439
www.crystalindustrial.in
sales@crystalindustrial.in
Crystal Industrial Syndicate from India, manufactures a variety of custom injection quills for a range of industrial processes. Our world-class chemical injection quills are manufactured in India comply with the world’s most stringent certifications. We have clients around the world, from Europe and North America to Africa and the Middle East. Please contact us for details about how we can meet your injection quills requirements. Contact us
Copyright © 2023 by Crystal Industrial Syndicate Pvt Ltd. All rights reserved. www.crystalindustrial.in