Chemical injection quills with back pressure valves are used in many industrial situations where chemicals need to be injected in a precise and controlled way. Here are some of the most common uses:
- Water treatment: In water treatment, back pressure valves are used to inject chemicals such as chlorine, sodium hydroxide, and hydrogen peroxide into the water stream to achieve the desired pH, disinfection, or oxidation-reduction potential.
- Oil and gas industry: In the oil and gas industry, back pressure valves are used to inject chemicals such as corrosion inhibitors, demulsifiers, and scale inhibitors into the wellbore or production pipelines to protect against corrosion, emulsion formation, and scaling.
- Food and beverage industry: In the food and beverage industry, back pressure valves are used to inject chemicals such as sanitizers, cleaners, and antifoaming agents into the production lines to maintain a clean and hygienic process.
- Pharmaceutical industry: In the pharmaceutical industry, back pressure valves are used to inject chemicals such as acids, bases, and solvents into the process stream to control the pH, viscosity, and chemical reactions.
- Pulp and paper industry: In the pulp and paper industry, back pressure valves are used to inject chemicals such as bleach, sizing agents, and retention aids into the process stream to improve the paper quality and reduce the environmental impact.
- Mining industry: In the mining industry, back pressure valves are used to inject chemicals such as flocculants, coagulants, and pH adjusters into the process stream to separate the mineral particles from the waste material and improve the recovery rates.
Food and beverage industry
The food and beverage industry also uses chemical injection quills with back pressure valves for a variety of purposes. These systems are used to inject chemicals such as sanitizers, cleaning agents, and preservatives into the processing lines to ensure food safety and product quality.
Sanitizers are used to kill bacteria and other microorganisms that can contaminate food products. The use of back pressure valves in chemical injection quills ensures that sanitizers are injected at the correct rate and pressure to achieve the desired level of disinfection.
Cleaning agents are used to remove dirt, grime, and other contaminants from processing equipment. The use of back pressure valves in chemical injection quills ensures that cleaning agents are injected at the correct rate and pressure to achieve the desired level of cleaning.
Preservatives are used to extend the shelf life of food products. The use of back pressure valves in chemical injection quills ensures that preservatives are injected at the correct rate and pressure to achieve the desired level of preservation.
In addition to these applications, chemical injection quills with back pressure valves are also used in the food and beverage industry for pH control, flavor enhancement, and color stabilization. The use of back pressure valves ensures that chemicals are injected at the correct rate, pressure, and location, which helps to maintain product consistency and quality.
Overall, chemical injection quills with back pressure valves are an important tool in the food and beverage industry. They help to ensure that chemicals are injected at the correct rate, pressure, and location, which is essential for ensuring food safety and product quality.
Pharmaceutical industry
Chemical injection quills with back pressure valves are commonly used in the pharmaceutical industry for a variety of purposes. These systems are used to inject chemicals such as acids, bases, solvents, and reagents into the production process to ensure product quality, consistency, and safety.
One important application of chemical injection quills with back pressure valves in the pharmaceutical industry is in the production of active pharmaceutical ingredients (APIs). These are the compounds that make up the active component of a drug product. Back pressure valves are used in the injection of solvents, reagents, and other chemicals used in the synthesis of APIs. The use of back pressure valves ensures that these chemicals are injected at the correct rate and pressure, which is essential for maintaining product quality and consistency.
Another application of chemical injection quills with back pressure valves in the pharmaceutical industry is in the production of vaccines. These systems are used to inject adjuvants, which are substances that help to enhance the immune response to the vaccine. The use of back pressure valves ensures that adjuvants are injected at the correct rate and pressure, which is essential for maintaining product safety and effectiveness.
In addition to these applications, chemical injection quills with back pressure valves are also used in the pharmaceutical industry for pH control, sterilization, and cleaning. The use of back pressure valves ensures that chemicals are injected at the correct rate, pressure, and location, which helps to maintain product consistency and quality.
Overall, chemical injection quills with back pressure valves are an important tool in the pharmaceutical industry. They help to ensure that chemicals are injected at the correct rate, pressure, and location, which is essential for maintaining product quality, consistency, and safety.
Pulp and paper industry
Chemical injection quills with back pressure valves are commonly used in the pulp and paper industry to inject various chemicals into the production process. These systems are used to ensure that chemicals such as bleach, dyes, and other additives are injected at the correct rate, pressure, and location, which is essential for maintaining product quality and consistency.
One important application of chemical injection quills with back pressure valves in the pulp and paper industry is in the production of pulp. Chemicals such as bleach and other oxidants are used to remove lignin and other impurities from the pulp. The use of back pressure valves ensures that these chemicals are injected at the correct rate and pressure, which is essential for maintaining product quality and consistency.
Another application of chemical injection quills with back pressure valves in the pulp and paper industry is in the production of paper. Chemicals such as dyes and other additives are used to enhance the color, texture, and other properties of the paper. The use of back pressure valves ensures that these chemicals are injected at the correct rate and pressure, which is essential for maintaining product quality and consistency.
In addition to these applications, chemical injection quills with back pressure valves are also used in the pulp and paper industry for pH control, slime control, and microbiological control. The use of back pressure valves ensures that chemicals are injected at the correct rate, pressure, and location, which helps to maintain product consistency and quality.
Overall, chemical injection quills with back pressure valves are an important tool in the pulp and paper industry. They help to ensure that chemicals are injected at the correct rate, pressure, and location, which is essential for maintaining product quality and consistency.
Mining industry
Chemical injection quills with back pressure valves are commonly used in the mining industry to inject various chemicals into the production process. These systems are used to ensure that chemicals such as acids, bases, flocculants, and other additives are injected at the correct rate, pressure, and location, which is essential for maintaining product quality and consistency.
One important application of chemical injection quills with back pressure valves in the mining industry is in the production of metals such as gold, copper, and silver. Chemicals such as cyanide and acid are used to leach the metal from the ore. The use of back pressure valves ensures that these chemicals are injected at the correct rate and pressure, which is essential for maintaining product quality and consistency.
Another application of chemical injection quills with back pressure valves in the mining industry is in the production of coal. Chemicals such as flocculants are used to separate the coal from the waste material. The use of back pressure valves ensures that these chemicals are injected at the correct rate and pressure, which is essential for maintaining product quality and consistency.
In addition to these applications, chemical injection quills with back pressure valves are also used in the mining industry for pH control, water treatment, and dust suppression. The use of back pressure valves ensures that chemicals are injected at the correct rate, pressure, and location, which helps to maintain product consistency and quality.
Overall, chemical injection quills with back pressure valves are an important tool in the mining industry. They help to ensure that chemicals are injected at the correct rate, pressure, and location, which is essential for maintaining product quality and consistency.
Click here for other applications of chemical injection quills with back pressure valve manufactured in India: Water treatment, oil & gas industry.
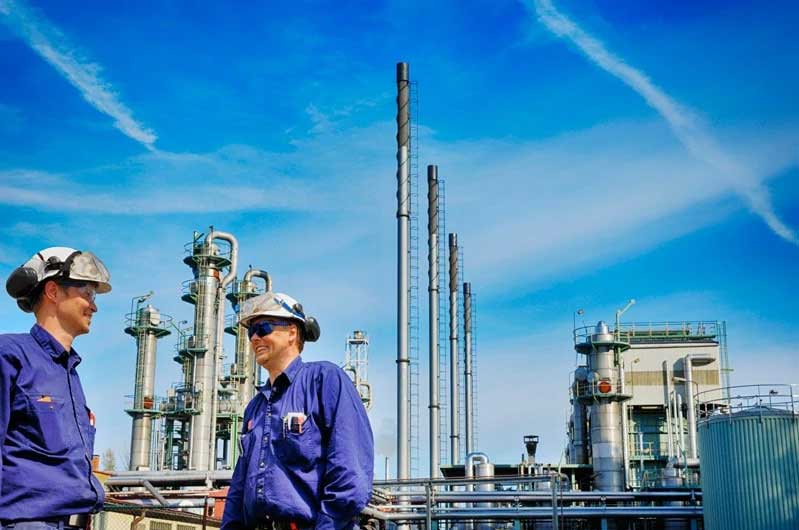
Contact us
Crystal Industrial Syndicate
Phone : +91-22-27563850
Fax: +91-22-67939439
www.crystalindustrial.in
sales@crystalindustrial.in
Crystal Industrial Syndicate from India, manufactures a variety of custom injection quills for a range of industrial processes. Our world-class chemical injection quills are manufactured in India comply with the world’s most stringent certifications. We have clients the world over, from Europe and North America to Africa and the Middle East. Please contact us for details about how we can meet your injection quills requirements. Contact us
Copyright © 2023 by Crystal Industrial Syndicate Pvt Ltd. All rights reserved. www.crystalindustrial.in