The process temperature and pressure are critical factors to consider when selecting an injection quill for your process. The injection quill must be able to withstand the temperature and pressure of the process stream and the chemical being injected.
The temperature of the process stream can affect the chemical properties and the performance of the injection quill. High temperatures can cause chemical reactions or degradation, which can affect the effectiveness of the chemical being injected. Additionally, the injection quill material must be able to withstand the high temperatures to prevent damage or failure.
Similarly, the pressure of the process stream can also affect the performance and durability of the injection quill. High-pressure applications require injection quills that can withstand the pressure to prevent damage or failure.
It’s essential to select an injection quill that can withstand the temperature and pressure of the process stream and the chemical being injected. The injection quill material and construction should be chosen to meet the process requirements and ensure safe and effective chemical injection.
Consulting with a qualified professional is recommended to ensure that the injection quill selected is appropriate for the specific process conditions. The professional will take into account the process temperature and pressure, the chemical being injected, and the process requirements to select the appropriate injection quill for the application.
Overall, the process temperature and pressure are critical factors to consider when selecting an injection quill. Choosing an injection quill that can withstand the process conditions will ensure safe and effective chemical injection and prevent damage or failure of the injection quill.
Importance of selecting the right injection quill for temperature and pressure
Selecting the right injection quill for the process temperature and pressure is crucial for ensuring safe and effective chemical injection. Failure to select the appropriate injection quill can lead to process issues, such as chemical degradation, equipment failure, and safety hazards.
If the injection quill cannot withstand the process temperature, it can cause chemical reactions or degradation, which can affect the effectiveness of the chemical being injected. This can lead to process issues, such as reduced efficiency, product quality issues, and safety hazards.
Similarly, if the injection quill cannot withstand the process pressure, it can result in equipment failure or safety hazards. High-pressure applications require injection quills that can withstand the pressure to prevent damage or failure. Failure to select the appropriate injection quill can lead to leaks, spills, or equipment failure, which can be hazardous and costly.
Choosing the appropriate injection quill for the process temperature and pressure is critical for ensuring safe and effective chemical injection. It’s essential to consult with a qualified professional to ensure that the injection quill selected can withstand the process conditions and meet the process requirements.
In summary, selecting the right injection quill for the process temperature and pressure is crucial for ensuring safe and effective chemical injection. Failure to select the appropriate injection quill can lead to process issues, equipment failure, and safety hazards. Consultation with a qualified professional is recommended to ensure the injection quill selected can meet the process requirements and withstand the process conditions.
How Process Temperature can affect the design of your injection quill
The process temperature plays a critical role in the design of an injection quill. High temperatures can cause chemical reactions or degradation, which can affect the effectiveness of the chemical being injected. Therefore, the injection quill must be designed to withstand the high temperatures and prevent damage or failure.
To design an injection quill for high-temperature applications, the material and construction of the injection quill must be carefully considered. The material must be able to withstand the temperature without degrading or reacting with the chemical being injected. For example, injection quills made of stainless steel or other high-temperature alloys may be used for high-temperature applications.
The length and diameter of the injection quill may also need to be adjusted for high-temperature applications. Longer injection quills may be required to ensure that the chemical is injected at the appropriate point in the process stream, while larger diameters may be needed to reduce the pressure drop across the injection quill.
Additionally, the design of the injection quill must account for the potential for thermal expansion and contraction. High temperatures can cause the injection quill to expand, which can affect the injection point and the performance of the chemical being injected. Therefore, the injection quill may need to be designed with expansion joints or other features to accommodate thermal expansion and contraction.
Overall, the process temperature plays a crucial role in the design of an injection quill. To ensure effective chemical injection and prevent damage or failure of the injection quill, the material, construction, length, diameter, and other design features of the injection quill must be carefully considered for the specific process temperature.
How Process Pressure can affect the design of your injection quill
Process pressure is another critical factor to consider when designing an injection quill. High-pressure applications require injection quills that can withstand the pressure to prevent damage or failure. Failure to select the appropriate injection quill for high-pressure applications can lead to leaks, spills, or equipment failure, which can be hazardous and costly.
To design an injection quill for high-pressure applications, the material, diameter, and wall thickness of the injection quill must be carefully considered. The material must be able to withstand the pressure without deforming, cracking, or failing. Injection quills made of high-strength materials such as stainless steel or high-strength alloys are commonly used for high-pressure applications.
The diameter and wall thickness of the injection quill must also be considered when designing for high-pressure applications. A larger diameter and thicker wall may be needed to reduce the pressure drop across the injection quill, which can help prevent the injection quill from failing due to excessive pressure.
Additionally, the design of the injection quill must account for the potential for vibration or oscillation caused by high-pressure flow. Vibrations can cause damage or failure of the injection quill, so it may be necessary to add supports or dampeners to prevent vibrations from affecting the injection quill.
In summary, process pressure is a crucial factor to consider when designing an injection quill. The material, diameter, wall thickness, and design features of the injection quill must be carefully considered for high-pressure applications to prevent damage or failure and ensure safe and effective chemical injection. It is important to consult with a qualified professional to determine the appropriate injection quill design for a specific high-pressure process application.
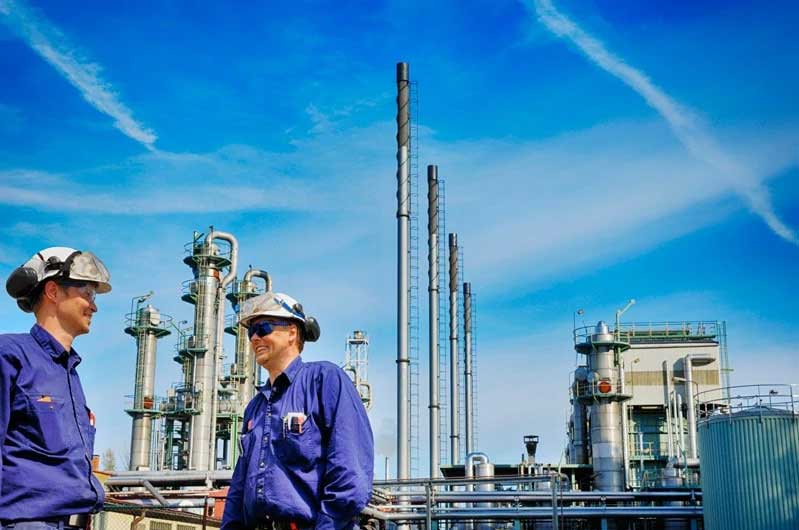
Contact us
Crystal Industrial Syndicate
Phone : +91-22-27563850
Fax: +91-22-67939439
www.crystalindustrial.in
sales@crystalindustrial.in
Crystal Industrial Syndicate from India, manufactures a variety of custom injection quills for a range of industrial processes. Our world-class chemical injection quills are manufactured in India comply with the world’s most stringent certifications. We have clients around the world, from Europe and North America to Africa and the Middle East. Please contact us for details about how we can meet your injection quills requirements. Contact us
Copyright © 2023 by Crystal Industrial Syndicate Pvt Ltd. All rights reserved. www.crystalindustrial.in