What are Dual injection quills?
Dual injection quills are specialized tools used in chemical injection processes to introduce two different chemicals simultaneously into a pipeline or vessel. As the name suggests, these quills have two separate injection ports that allow for the injection of two different chemicals at the same time. Here are some key features and benefits of dual injection quills:
Overall, dual injection quills can be a valuable tool in chemical injection processes, allowing for the simultaneous injection of two different chemicals with precise control over the dosing of each chemical. They are a cost-effective and compact solution for a variety of pipeline and vessel configurations, offering reduced risk of contamination and improved quality control.
Advantages of Dual injection quills
Dual injection quills are specialized tools used in chemical injection processes to introduce two different chemicals simultaneously into a pipeline or vessel. They offer several advantages over other injection methods, including:
- Simultaneous Injection: One of the main advantages of dual injection quills is their ability to inject two different chemicals simultaneously. This can be beneficial in applications where multiple chemicals are required to achieve the desired result, such as in water treatment or chemical processing.
- Precise Control: Dual injection quills offer precise control over the injection process. Each injection port can be adjusted independently, allowing for accurate dosing of each chemical. This is important in applications where precise control is necessary for optimal performance.
- Compact Design: Dual injection quills are designed to be compact and easy to install. They can be used in a wide range of pipeline and vessel configurations, making them a versatile tool for chemical injection.
- Cost-Effective: Using a dual injection quill can be more cost-effective than using two separate injection quills. The dual quill allows for the injection of two chemicals using a single tool, reducing the need for additional equipment and minimizing installation and maintenance costs.
- Reduced Risk of Contamination: With two separate injection ports, there is less risk of cross-contamination between the two chemicals being injected. This can be especially important in applications where strict quality control measures are necessary.
- Improved Efficiency: Dual injection quills can improve the efficiency of chemical injection processes. With the ability to inject two chemicals simultaneously, the overall injection process can be faster and more streamlined.
- Versatility: Dual injection quills can be used in a wide range of applications, including water treatment, chemical processing, and oil and gas production. They can be used with a variety of chemicals and pipeline configurations, making them a versatile tool for chemical injection.
Overall, dual injection quills offer several advantages over other injection methods. They allow for the simultaneous injection of two different chemicals with precise control over dosing, while also offering a compact design, reduced risk of contamination, improved efficiency, and versatility in a wide range of applications.
Disadvantages of Dual injection quills
While dual injection quills offer many advantages in chemical injection processes, there are also some potential disadvantages to consider:
- Complexity: Dual injection quills are more complex than single injection quills, with two separate injection ports that require independent control. This can increase the complexity of the injection process, requiring more training and expertise to operate effectively.
- Higher Cost: Dual injection quills are more expensive than single injection quills, due to their more complex design and additional features. This can make them less cost-effective in some applications, especially where only one chemical is required.
- Maintenance: Dual injection quills require more maintenance than single injection quills, as there are more parts to inspect and replace. This can increase the overall cost of ownership and may require more downtime for maintenance.
- Limited Flow Rates: Dual injection quills may have more limited flow rates than single injection quills, due to the need to split the flow between two injection ports. This may limit their effectiveness in applications where high flow rates are required.
- Limited Chemical Compatibility: Dual injection quills may have limited compatibility with certain chemicals, especially if the chemicals are incompatible with each other or with the materials used in the quill.
- Increased Risk of Failure: With two separate injection ports, there is a higher risk of failure in dual injection quills compared to single injection quills. If one of the injection ports fails, the entire quill may need to be replaced, increasing downtime and maintenance costs.
Overall, while dual injection quills offer many advantages in chemical injection processes, they may also have some potential disadvantages to consider. These include increased complexity, higher cost, more maintenance, limited flow rates, limited chemical compatibility, and increased risk of failure.
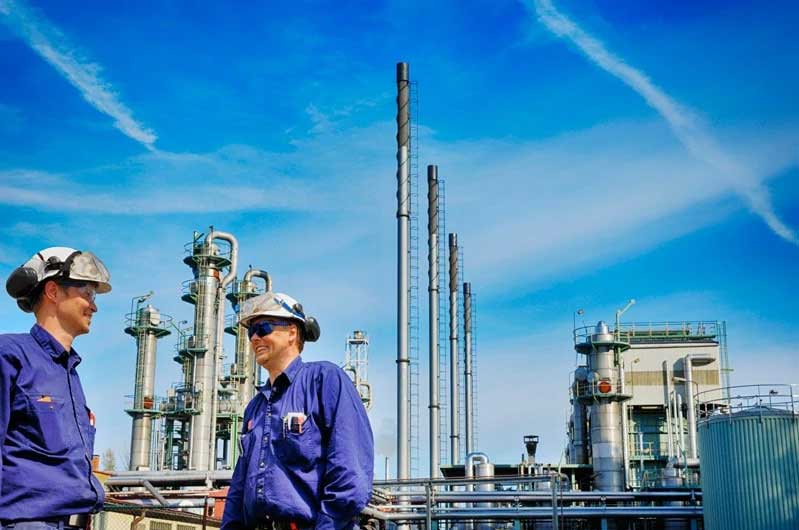
Contact us
Crystal Industrial Syndicate
Phone : +91-22-27563850
Fax: +91-22-67939439
www.crystalindustrial.in
sales@crystalindustrial.in
Crystal Industrial Syndicate from India, manufactures a variety of custom injection quills for a range of industrial processes. Our world-class chemical injection quills are manufactured in India comply with the world’s most stringent certifications. We have clients around the world, from Europe and North America to Africa and the Middle East. Please contact us for details about how we can meet your injection quills requirements. Contact us
Copyright © 2023 by Crystal Industrial Syndicate Pvt Ltd. All rights reserved. www.crystalindustrial.in