Chemical injection quills with back pressure valves are used in a variety of industrial applications that require precise and controlled chemical injection. Here are some examples of common applications:
- Type of chemical being injected: Different chemicals may require different injection rates and pressures. Some chemicals may also be corrosive or hazardous, requiring special materials or safety measures.
- Operating pressure and temperature: The pressure and temperature of the process fluid can affect the performance and durability of the quill, and must be taken into account when designing the quill.
- Flow rate of the chemical: The flow rate of the chemical will affect the size and shape of the quill, and must be calculated to ensure proper injection.
- Material compatibility: The quill and back pressure valve must be made from materials that are resistant to corrosion and degradation by the process fluid and the chemical being injected.
- Environmental conditions: Exposure to UV radiation or extreme temperatures can affect the performance and durability of the quill, and the design must take these factors into account.
Overall, careful consideration of these factors will help to ensure that the chemical injection quill is designed to meet the specific requirements of the application, and is effective, reliable, and durable.
Type of chemical being injected
The type of chemical being injected is a critical factor to consider when designing a chemical injection quill. Different chemicals have different properties, such as viscosity, density, and reactivity, which can affect the design and operation of the quill.
For example, highly reactive chemicals may require a shorter quill length to minimize the time between injection and mixing with the process fluid, while viscous chemicals may require a larger quill diameter to prevent clogging or blockage.
In addition, the chemical properties can also affect the selection of materials for the quill and back pressure valve, as certain materials may be more resistant to corrosion or degradation from specific chemicals.
By carefully considering the type of chemical being injected, designers can ensure that the quill is optimized for the specific properties of the chemical, and that the system operates safely and effectively.
Operating pressure and temperature
Operating pressure and temperature are important factors to consider when designing a chemical injection quill. The quill must be able to withstand the pressure and temperature conditions of the process fluid, while also providing consistent and accurate injection of the chemical.
High operating temperatures or pressures can cause materials to degrade or corrode over time, which can lead to leaks or failure of the quill. In addition, extreme conditions may also affect the chemical properties, such as viscosity or reactivity, which can impact the performance of the injection system.
To ensure the quill can handle the operating conditions, designers must carefully select materials that are resistant to corrosion and high temperatures, and properly size the quill to prevent pressure drops or flow restrictions. They must also consider the impact of the operating conditions on the back pressure valve, and ensure it is properly sized and calibrated to provide accurate and consistent control over the injection flow. By considering these factors, designers can ensure the quill operates safely and reliably in a variety of operating conditions.
Flow rate of the chemical
The flow rate of the chemical is a critical factor to consider when designing a chemical injection quill. The quill must be designed to handle the required flow rate while ensuring consistent and accurate injection of the chemical into the process fluid.
The flow rate of the chemical can be influenced by several factors, such as the injection pressure, the properties of the chemical, and the process fluid conditions. For example, highly viscous chemicals may require a larger diameter quill to accommodate a higher flow rate, while low viscosity chemicals may require a smaller quill diameter to prevent backflow or leakage.
To properly design the quill for the required flow rate, designers must accurately calculate the injection pressure and consider the properties of the chemical and process fluid. They must also select materials that are resistant to erosion and wear, as high flow rates can cause accelerated degradation of the quill.
In addition to properly sizing the quill, designers must also select an appropriate back pressure valve to provide accurate and consistent control over the injection flow rate. By carefully considering the flow rate of the chemical, designers can ensure that the quill operates reliably and efficiently, providing accurate injection of the chemical into the process fluid.
Material compatibility
Material compatibility is a crucial factor to consider when designing a chemical injection quill, as it directly affects the quill’s ability to withstand exposure to the chemical being injected and the process fluid. The quill must be constructed from materials that are compatible with the chemical to be injected and must be able to withstand the temperature and pressure conditions of the process fluid.
Failure to select materials that are compatible with the chemical being injected can result in degradation of the quill, which can lead to failure, leaks, or other issues. For example, chemical reactions between the chemical being injected and the quill material can result in corrosion or erosion, leading to leaks or contamination of the process fluid.
When selecting materials for the quill, it is essential to consider the chemical properties, such as acidity or alkalinity, viscosity, and temperature. Designers must also consider the properties of the process fluid, including pressure, temperature, and flow rate. In many cases, specialized coatings or linings may be required to protect the quill from chemical attack.
By carefully selecting materials that are compatible with the chemical and process fluid, designers can ensure that the quill operates reliably and effectively, providing accurate and consistent injection of the chemical into the process fluid.
Environmental conditions
Environmental conditions are an important factor to consider when designing a chemical injection quill. The quill must be able to operate effectively under a range of environmental conditions, including temperature, humidity, and exposure to the elements.
For outdoor applications, the quill must be designed to withstand exposure to the elements, including rain, wind, and UV radiation. In areas with extreme temperatures, the quill must be able to operate reliably in hot or cold conditions without degradation or failure.
Environmental factors can also affect the selection of materials for the quill. For example, in areas with high humidity, materials that are prone to rust or corrosion should be avoided. In environments with high levels of dust or particulate matter, the quill should be designed with appropriate filters to prevent contamination of the chemical being injected.
When designing a chemical injection quill, it is essential to consider the environmental conditions in which it will be used and to select materials and components that are appropriate for the operating environment. This will help to ensure that the quill operates reliably and effectively, even under challenging environmental conditions.
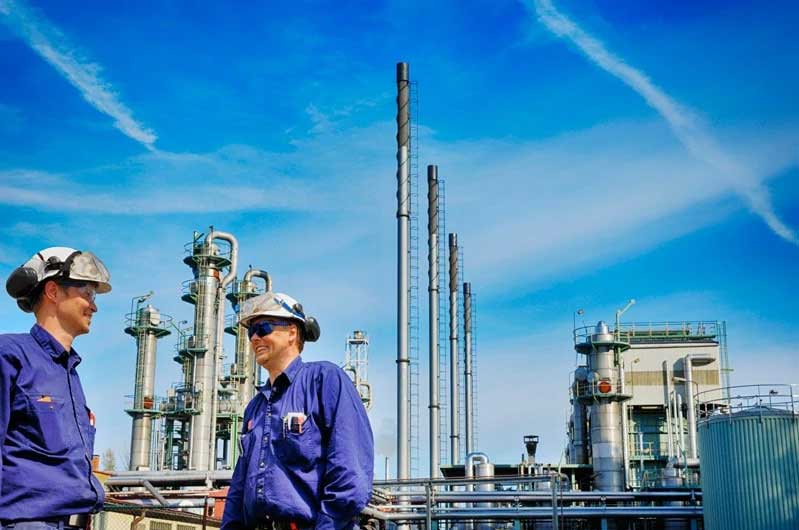
Contact us
Crystal Industrial Syndicate
Phone : +91-22-27563850
Fax: +91-22-67939439
www.crystalindustrial.in
sales@crystalindustrial.in
Crystal Industrial Syndicate from India, manufactures a variety of custom injection quills for a range of industrial processes. Our world-class chemical injection quills are manufactured in India comply with the world’s most stringent certifications. We have clients the world over, from Europe and North America to Africa and the Middle East. Please contact us for details about how we can meet your injection quills requirements. Contact us
Copyright © 2023 by Crystal Industrial Syndicate Pvt Ltd. All rights reserved. www.crystalindustrial.in