The use of a back pressure valve in a chemical injection quill offers a number of advantages, including:
- Consistent Injection Rate: A back pressure valve helps to ensure a consistent injection rate of the chemical into the system, regardless of changes in the process conditions. This is essential for maintaining the effectiveness of the chemical treatment process and ensuring the safety and efficiency of the system.
- Increased Efficiency: By regulating the injection rate and pressure, a back pressure valve helps to optimize the use of chemicals, reducing waste and ensuring that the chemicals are used effectively.
- Improved Safety: A back pressure valve helps to prevent over-injection of chemicals, which can be dangerous or cause damage to the system. It also helps to prevent under-injection, which can lead to poor performance or inadequate treatment of the process stream.
- Customizable and Adjustable: Back pressure valves are available in different sizes, types, and materials, and can be adjusted to suit the specific needs of the application. This means that they can be customized to meet the specific requirements of the system, ensuring optimal performance and effectiveness.
- Durability: Back pressure valves are typically made from high-quality materials, such as stainless steel, which makes them durable and resistant to corrosion and wear. This means that they can withstand harsh process conditions and have a longer lifespan, reducing the need for frequent replacement.
In summary, the use of a back pressure valve in a chemical injection quill can help to improve the safety, efficiency, and effectiveness of the chemical treatment process, while also ensuring that the system operates reliably and consistently.
Consistent Injection Rate
A back pressure valve plays a critical role in ensuring a controlled chemical injection in a system. Its main function is to regulate the pressure and flow rate of the injection fluid, and to maintain a consistent injection rate and pressure, even in the face of fluctuations in the process stream.
The back pressure valve works by controlling the flow of the injection fluid through the injection quill. As the pressure of the process stream fluctuates, the back pressure valve adjusts the flow rate of the injection fluid to maintain a constant pressure at the injection point. This is achieved through the use of a spring-loaded mechanism or a diaphragm, which responds to changes in pressure by opening or closing the valve, allowing more or less of the injection fluid to flow through.
One of the key benefits of a back pressure valve is its ability to provide accurate and consistent control of the injection rate, even in challenging process conditions. This can be particularly important in applications where precise dosing of the chemical is critical to the operation of the system. Back pressure valves can be adjusted to accommodate changes in the process stream and to optimize the injection rate to achieve the desired outcome.
Overall, a back pressure valve is an essential component of any controlled chemical injection system, as it ensures a reliable and accurate injection of chemicals into the system, which is necessary for the safe and efficient operation of the process.
Increased Efficiency
Increased efficiency is one of the key advantages of using a back pressure valve in a chemical injection quill. By regulating the injection rate and pressure of the chemical, a back pressure valve can optimize the use of the chemical, reducing waste and ensuring that the chemical is used effectively.
When chemicals are injected into a system without regulation, there is a risk of over-injection or under-injection, which can result in inefficiencies in the process. Over-injection can lead to waste of chemicals, which can be costly and have environmental impacts. Under-injection, on the other hand, can lead to poor performance or inadequate treatment of the process stream, which can result in decreased efficiency or even system failure.
A back pressure valve helps to prevent these inefficiencies by regulating the injection rate and pressure of the chemical. This ensures that the chemical is injected at the correct rate and pressure, in the right amount, and in the right location. This, in turn, can help to optimize the chemical treatment process and improve the overall efficiency of the system.
Moreover, the use of a back pressure valve can also help to reduce the frequency of chemical refilling or replacement, since the injection rate is optimized to achieve the desired outcome. This can help to reduce the costs associated with chemical usage and improve the overall efficiency of the process.
In conclusion, the increased efficiency achieved through the use of a back pressure valve in a chemical injection quill is a critical advantage, as it can help to optimize the chemical treatment process, reduce waste, and improve the overall performance of the system.
Improved Safety
Another important advantage of using a back pressure valve in a chemical injection quill is improved safety. The back pressure valve helps to prevent over-injection of chemicals, which can be dangerous or cause damage to the system. It also helps to prevent under-injection, which can lead to poor performance or inadequate treatment of the process stream.
Over-injection of chemicals can be a safety hazard, as it can lead to the buildup of excess pressure in the system. This pressure buildup can cause leaks, spills, or other hazards that can endanger workers or damage the environment. By regulating the injection rate and pressure, a back pressure valve helps to prevent over-injection and reduce the risk of these hazards.
Under-injection, on the other hand, can lead to poor performance of the chemical treatment process, which can compromise the safety and efficiency of the system. For example, if a chemical is not injected at the correct rate or in the right amount, it may not be effective in treating the process stream. This can result in inadequate treatment of the process stream, which can lead to safety hazards or system failure.
By ensuring that the chemical is injected at the correct rate and pressure, in the right amount, and in the right location, a back pressure valve helps to optimize the chemical treatment process, which can improve the safety and efficiency of the system. This can help to prevent hazards, reduce the risk of system failure, and ensure that the system operates safely and effectively.
In conclusion, improved safety is an important advantage of using a back pressure valve in a chemical injection quill, as it can help to prevent over-injection and under-injection of chemicals, which can compromise the safety and efficiency of the system.
Customizable and Adjustable
The fourth advantage of using a back pressure valve in a chemical injection quill is its customizability and adjustability. Back pressure valves can be customized and adjusted to meet the specific needs of the process, making them highly versatile and adaptable to various system configurations and requirements.
Back pressure valves can be adjusted to control the injection rate and pressure of the chemical, which can be critical in achieving the desired outcome of the chemical treatment process. They can be customized to accommodate different chemical viscosities, operating pressures, and flow rates, allowing for optimal chemical injection and treatment.
Moreover, back pressure valves can be designed to accommodate different materials of construction, making them suitable for use in a wide range of process environments. They can be made from various materials, such as stainless steel, brass, or PVC, depending on the chemical being injected and the process conditions.
Additionally, back pressure valves can be integrated with various types of chemical injection quills, such as fixed or adjustable depth injection quills, to ensure that the chemical is injected at the correct location within the process stream.
By providing customizable and adjustable solutions for chemical injection, back pressure valves can help to optimize the chemical treatment process and improve the efficiency and safety of the system.
In conclusion, the customizability and adjustability of back pressure valves is an important advantage, as it allows for the optimization of the chemical treatment process to meet the specific needs of the system. This adaptability makes back pressure valves highly versatile and effective in achieving the desired outcome of the chemical treatment process.
Durability
The fifth advantage of using a back pressure valve in a chemical injection quill is durability. Back pressure valves are typically constructed from high-quality materials, such as stainless steel, brass, or other corrosion-resistant alloys, which ensure their long-term durability and reliability in a variety of process environments.
The durability of back pressure valves is especially important in harsh and demanding process environments where the chemical injection system is subjected to extreme temperatures, pressures, and chemical exposures. The robust construction of back pressure valves ensures that they can withstand these conditions and maintain their functionality over time, providing a reliable and long-lasting solution for chemical injection.
Back pressure valves also require minimal maintenance, which further adds to their durability and reliability. They typically operate for extended periods without requiring repair or replacement, which reduces the risk of system downtime and associated costs.
By providing a durable and reliable solution for chemical injection, back pressure valves can help to ensure that the chemical treatment process operates efficiently and effectively over the long term, which enhances the safety and performance of the system.
In conclusion, the durability of back pressure valves is an important advantage that ensures their long-term reliability and functionality in harsh and demanding process environments. The robust construction of back pressure valves, combined with their minimal maintenance requirements, makes them a cost-effective and efficient solution for chemical injection in a variety of industrial applications.
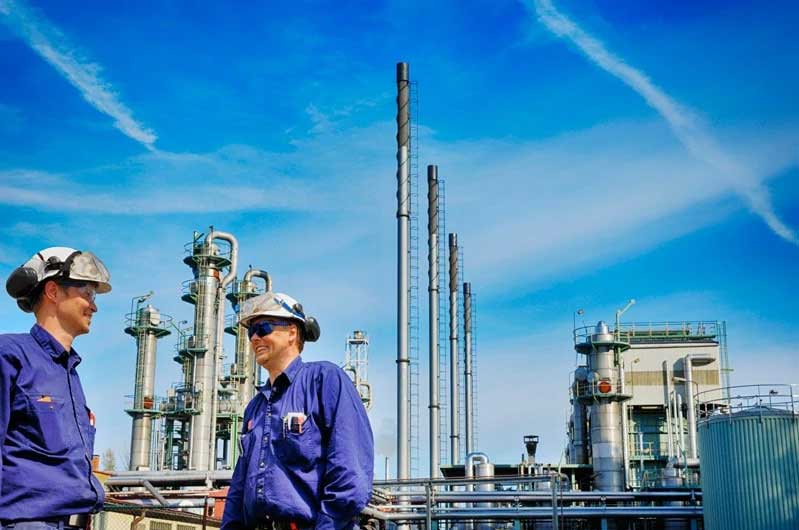
Contact us
Crystal Industrial Syndicate
Phone : +91-22-27563850
Fax: +91-22-67939439
www.crystalindustrial.in
sales@crystalindustrial.in
Crystal Industrial Syndicate from India, manufactures a variety of custom injection quills for a range of industrial processes. Our world-class chemical injection quills are manufactured in India comply with the world’s most stringent certifications. We have clients the world over, from Europe and North America to Africa and the Middle East. Please contact us for details about how we can meet your injection quills requirements. Contact us
Copyright © 2023 by Crystal Industrial Syndicate Pvt Ltd. All rights reserved. www.crystalindustrial.in