- Improper Material Selection
- Incorrect Dimensions
- Poor Welds or Joining Techniques
- Insufficient Wall Thickness
- Improper Surface Finish
- Incorrect Sizing
Click here for details on Poor Welds or Joining Techniques and Insufficient Wall Thickness
Click here for details on Improper Material Selection and Incorrect Dimensions
Improper Surface Finish
Improper surface finish is another mistake that can occur in the construction of the inlet of an injection quill. The surface finish of the inlet can impact the performance of the injection quill, and can also pose a risk to people or the environment.
For example, if the surface finish of the inlet is too rough, it may promote the buildup of deposits or contaminants, which can impact the flow of the fluid or gas. If the surface finish is too smooth, it may be difficult to clean or maintain, which can also impact performance and safety.
It is important to consider the intended application and operating conditions when determining the appropriate surface finish for the inlet. The surface finish should be chosen to ensure that the inlet will be able to perform its intended function safely and effectively, without posing a risk to people or the environment.
By ensuring that the surface finish of the inlet is appropriate, you can help ensure that it will be able to perform its intended function safely and effectively, without posing a risk to people or the environment.
Incorrect Sizing
Incorrect sizing of the inlet in an injection quill is a common mistake that can impact the performance and efficiency of the quill. The size of the inlet must be properly designed and sized to ensure optimal performance. An undersized inlet can lead to restricted flow and increased pressure drop, while an oversized inlet can result in poor mixing and inefficient injection.
When the inlet is undersized, it restricts the flow of the injected fluid, leading to increased pressure drop and reduced performance. This can impact the efficiency of the injection process and lead to additional wear and tear on the quill. Additionally, an undersized inlet can cause increased velocity and turbulence, which can result in erosion and corrosion of the inlet and the injection point.
On the other hand, an oversized inlet can lead to poor mixing and inefficient injection. This is because an oversized inlet can cause the injected fluid to disperse too quickly and not mix effectively with the process stream. This can result in inadequate dispersion of the injected fluid and reduced effectiveness of the injection process.
To avoid incorrect sizing, it is essential to design and size the inlet properly during the construction of the injection quill. This involves considering the fluid flow rate, viscosity, pressure drop, and other factors to ensure the inlet is properly sized for optimal performance. It is also important to ensure the inlet is correctly aligned and supported to prevent any bending, vibration, or other issues that can impact its performance.
Overall, incorrect sizing of the inlet in an injection quill can have significant consequences on the performance, efficiency, and longevity of the quill. Therefore, proper sizing of the inlet is a critical factor that must be carefully considered during the construction of the injection quill.
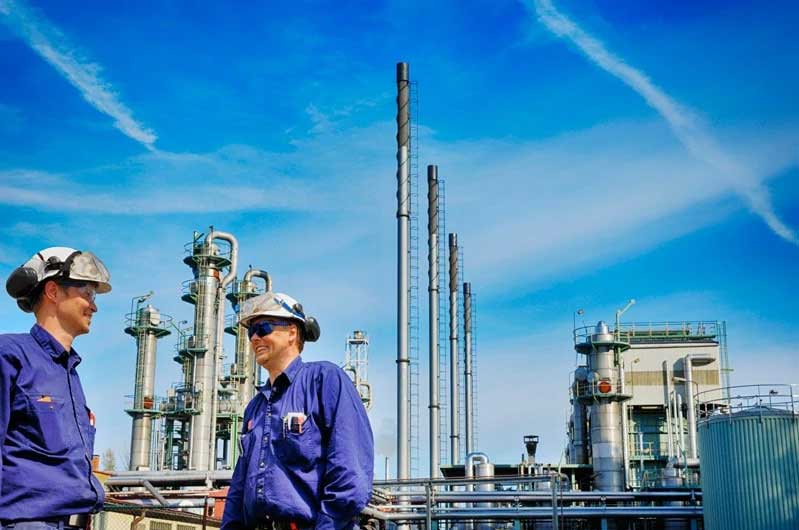
Contact us
Crystal Industrial Syndicate
Phone : +91-22-27563850
Fax: +91-22-67939439
www.crystalindustrial.in
sales@crystalindustrial.in
Crystal Industrial Syndicate from India, manufactures a variety of custom injection quills for a range of industrial processes. Our world-class chemical injection quills are manufactured in India comply with the world’s most stringent certifications. We have clients around the world, from Europe and North America to Africa and the Middle East. Please contact us for details about how we can meet your injection quills requirements. Contact us
Copyright © 2023 by Crystal Industrial Syndicate Pvt Ltd. All rights reserved. www.crystalindustrial.in