Startup is the sixth stage of the installation process for injection quills. During this stage, the following tasks are performed:
- Starting up the process line: The process line is started up and the injection quill is integrated into the process.
- Monitoring the injection quill: The injection quill is monitored for proper operation, including proper flow rate, pressure, and temperature.
- Verifying proper operation: The injection quill is checked for proper operation and any issues are identified and resolved.
The purpose of the startup stage is to bring the injection quill into operation as part of the process line. This stage is critical to ensure that the injection quill is functioning properly and that the process line is running smoothly and efficiently.
Starting up the process line is the final step in the Startup stage of the installation process for injection quills. The goal of this step is to begin operation of the process line with the new injection quill installed.
Starting up the process line
Before starting up the process line, it is important to conduct a final inspection of the injection quill to ensure that all connections are secure, that there are no leaks, and that the quill is properly installed and configured.
Once the final inspection is complete, the process line can be started. This typically involves opening valves and starting pumps or other process equipment, depending on the specific process line configuration.
It is important to closely monitor the operation of the process line during the start-up process to ensure that there are no problems or issues with the operation of the injection quill. This may involve monitoring flow rates, pressure levels, and other performance criteria specific to the type of injection quill being installed.
Once the process line is up and running with the new injection quill, it is important to continue to monitor the operation of the quill to ensure that it continues to function properly and that it is delivering the correct amount of fluid to the process line.
The successful start-up of the process line with the new injection quill is a key milestone in the installation process and signifies the completion of the installation and the start of normal operation.
Monitoring the injection quill
Monitoring the injection quill is an important step in the Startup stage of the installation process for injection quills. The goal of this step is to closely observe the operation of the quill to ensure that it is functioning properly and delivering the correct amount of fluid to the process line.
This may involve monitoring flow rates, pressure levels, and other performance criteria specific to the type of injection quill being installed. Any issues or deviations from expected performance levels should be immediately addressed to ensure that the injection quill is delivering the correct amount of fluid to the process line.
Additionally, monitoring the injection quill can help identify any potential problems or issues early on, allowing them to be resolved before they become more serious or result in damage to the process line or equipment.
It is also important to periodically inspect the injection quill to ensure that it is securely attached to the process line and that there are no leaks or other problems with the installation.
Regular monitoring and maintenance of the injection quill is important to ensure that it continues to function properly and deliver the correct amount of fluid to the process line over time.
Verifying proper operation
Verifying proper operation is an important step in the Startup stage of the installation process for injection quills. The goal of this step is to confirm that the injection quill is functioning correctly and delivering the correct amount of fluid to the process line.
This may involve monitoring flow rates, pressure levels, and other performance criteria specific to the type of injection quill being installed. Any deviations from expected performance levels should be immediately addressed to ensure that the injection quill is operating properly.
It is also important to inspect the injection quill and surrounding process line components to ensure that there are no leaks or other issues with the installation.
If any problems or issues are detected during the verification process, it is important to take immediate steps to resolve them, as these issues can impact the performance of the process line and the accuracy of the fluid delivery.
Once all issues have been resolved and the injection quill has been confirmed to be operating properly, the process line can be considered to be fully operational with the new injection quill installed. This is an important milestone in the installation process, as it signifies that the quill is delivering the correct amount of fluid to the process line as intended.
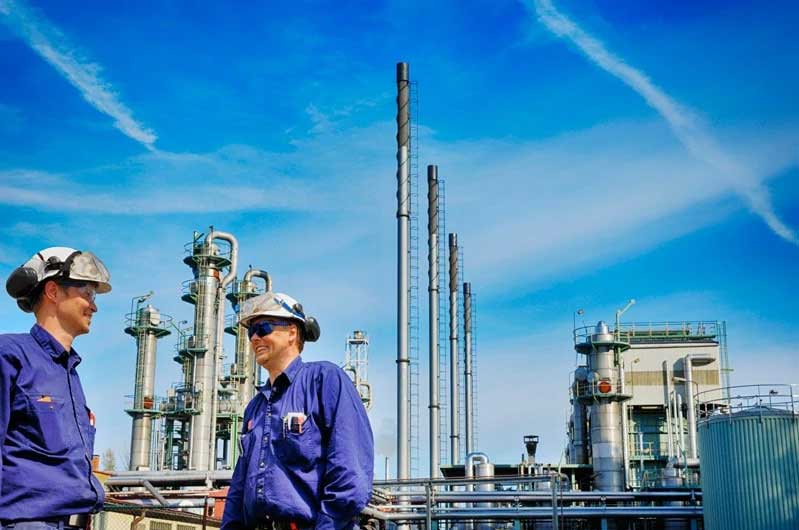
Contact us
Crystal Industrial Syndicate
Phone : +91-22-27563850
Fax: +91-22-67939439
www.crystalindustrial.in
sales@crystalindustrial.in
Crystal Industrial Syndicate from India, manufactures a variety of custom injection quills for a range of industrial processes. Our world-class chemical injection quills are manufactured in India comply with the world’s most stringent certifications. We have clients the world over, from Europe and North America to Africa and the Middle East. Please contact us for details about how we can meet your injection quills requirements. Contact us
Copyright © 2023 by Crystal Industrial Syndicate Pvt Ltd. All rights reserved. www.crystalindustrial.in