Self-sealing injection quills are specialized devices used for injecting chemicals or fluids into a process stream. As the name suggests, these quills are designed to seal themselves once the injection is complete, preventing the process fluid from leaking out or the surrounding environment from seeping in.
Self-sealing injection quills typically consist of a hollow metal tube with an injection port at one end and a valve or plug at the other end. The quill is inserted into the process stream, and the chemical or fluid is injected through the injection port. Once the injection is complete, the valve or plug automatically seals the injection port, preventing any process fluid from escaping or any contaminants from entering the process stream.
Self-sealing injection quills are commonly used in applications where the injected chemical or fluid is hazardous, corrosive, or otherwise harmful to the process stream or surrounding environment. They are also used in applications where a high degree of precision and control is required, such as in the chemical, pharmaceutical, and food and beverage industries.
One of the key advantages of self-sealing injection quills is their ability to prevent leaks and spills, which can be costly and dangerous in certain applications. They also help to maintain the purity and integrity of the process stream, which is essential in industries such as pharmaceuticals and food and beverage production.
Overall, self-sealing injection quills are a specialized type of injection quill designed to provide precise and controlled injection while minimizing the risk of leaks and contamination. They are a valuable tool in a wide range of industries where safety and process integrity are a top priority.
Advantages of Self-sealing injection quills
Self-sealing injection quills offer several advantages, including:
- Preventing leaks and spills: One of the primary advantages of self-sealing injection quills is that they prevent leaks and spills of the injected chemical or fluid. This is especially important in applications where the injected substance is hazardous, corrosive, or otherwise harmful to the process stream or surrounding environment.
- Maintaining process integrity: Self-sealing injection quills help to maintain the purity and integrity of the process stream by preventing contaminants from entering or process fluids from escaping. This is important in industries such as pharmaceuticals and food and beverage production, where the quality and safety of the final product are paramount.
- Improving safety: By preventing leaks and spills, self-sealing injection quills help to improve safety in the workplace, reducing the risk of accidents and injuries.
- Increasing efficiency: Self-sealing injection quills can help to increase efficiency by reducing the amount of time and labor required for maintenance and clean-up. They also help to minimize downtime by preventing leaks and spills that can cause process disruptions.
- Providing precision and control: Self-sealing injection quills offer precision and control over the injection process, allowing for accurate dosing and consistent performance.
Overall, self-sealing injection quills are a valuable tool in industries where safety, process integrity, and efficiency are a top priority. They offer several advantages over traditional injection quills, including preventing leaks and spills, maintaining process integrity, improving safety, increasing efficiency, and providing precision and control.
Disadvantages of Self-sealing injection quills
While self-sealing injection quills offer several advantages, there are also some potential disadvantages to consider, including:
- Limited compatibility: Self-sealing injection quills may not be compatible with all types of chemicals or fluids. Some substances may require specialized materials or designs to ensure proper sealing and prevent damage to the quill or valve.
- Cost: Self-sealing injection quills can be more expensive than traditional injection quills due to the added complexity of the valve or plug mechanism. This may make them less attractive for applications where cost is a major concern.
- Maintenance requirements: Self-sealing injection quills require regular maintenance to ensure proper sealing and prevent buildup or clogging of the valve or plug mechanism. This can increase the time and labor required for maintenance compared to traditional injection quills.
- Limited flexibility: Once a self-sealing injection quill is installed, it may be difficult to modify or adjust the injection rate or volume. This can limit the flexibility of the system and may require costly modifications if process requirements change.
- Pressure limitations: Self-sealing injection quills may have pressure limitations that restrict their use in high-pressure applications. This can limit their utility in some industries or processes.
Overall, while self-sealing injection quills offer many advantages, they may not be the best solution for every application. It is important to carefully consider the potential disadvantages and weigh them against the benefits when evaluating whether a self-sealing injection quill is the right choice for a specific process.
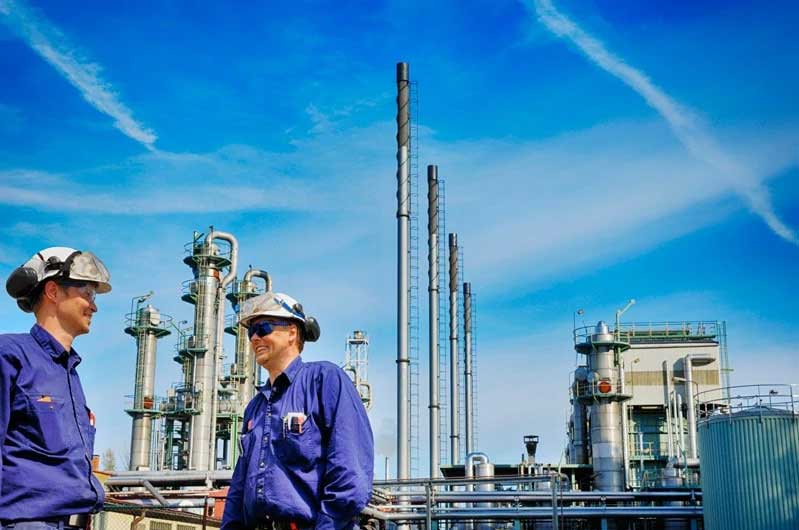
Contact us
Crystal Industrial Syndicate
Phone : +91-22-27563850
Fax: +91-22-67939439
www.crystalindustrial.in
sales@crystalindustrial.in
Crystal Industrial Syndicate from India, manufactures a variety of custom injection quills for a range of industrial processes. Our world-class chemical injection quills are manufactured in India comply with the world’s most stringent certifications. We have clients around the world, from Europe and North America to Africa and the Middle East. Please contact us for details about how we can meet your injection quills requirements. Contact us
Copyright © 2023 by Crystal Industrial Syndicate Pvt Ltd. All rights reserved. www.crystalindustrial.in