Direct steam injection quills are a type of injection quill used to inject steam directly into a liquid process stream. This injection method is commonly used in industries such as food and beverage, chemical processing, and pharmaceuticals, where precise temperature control is essential for the manufacturing process.
Direct steam injection quills typically consist of a steam nozzle located inside a hollow tube or pipe. The steam is injected into the process stream through the nozzle, where it is mixed with the liquid to raise the temperature to the desired level. The steam flow rate is typically controlled by a valve or other flow control mechanism.
Direct steam injection quills can be used for a variety of applications, including heating, sterilization, and cooking. They can also be used to improve mixing and dispersion of the injected steam within the process stream.
One advantage of direct steam injection quills is their ability to rapidly heat the process stream to the desired temperature. This allows for faster processing times and greater efficiency in the manufacturing process. Additionally, direct steam injection quills are often more efficient and cost-effective than other heating methods, such as indirect heating or heat exchangers.
However, direct steam injection quills also have some limitations. For example, they may not be suitable for processes that require extremely precise temperature control or where there is a risk of thermal degradation of the product. Additionally, the injection of steam can result in a change in the physical and chemical properties of the process stream, which may need to be taken into account in the manufacturing process.
Advantages of Direct steam injection quills
- Rapid heating: Direct steam injection quills can rapidly heat the process stream to the desired temperature. This allows for faster processing times and increased efficiency in the manufacturing process.
- Precise temperature control: Direct steam injection quills offer precise temperature control, which is important in industries such as food and beverage, where temperature can affect the quality and safety of the final product.
- Efficient: Direct steam injection quills are often more efficient and cost-effective than other heating methods, such as indirect heating or heat exchangers. This is because they use steam directly to heat the process stream, without the need for an intermediate fluid or heat transfer surface.
- Improved mixing and dispersion: Direct steam injection quills can improve mixing and dispersion of the injected steam within the process stream, which can result in more uniform heating and processing. This can be particularly useful for processes that require consistent and precise temperature control.
- Flexibility: Direct steam injection quills can be used for a variety of applications, including heating, sterilization, and cooking. They can also be used with a wide range of liquids and process streams, making them a versatile option for many manufacturing processes.
- Reduced fouling: Direct steam injection quills can reduce fouling in the process stream, which can improve the performance and efficiency of other equipment in the manufacturing process. This is because the injected steam can help to break up and prevent the build-up of solids or other contaminants in the process stream.
Overall, the advantages of direct steam injection quills make them a popular choice for many industries and manufacturing processes. They offer rapid heating, precise temperature control, efficiency, improved mixing and dispersion, flexibility, and reduced fouling, making them a versatile and cost-effective option for many manufacturing applications.
Disadvantages of Direct steam injection quills
- Scaling and buildup: Direct steam injection quills can be prone to scaling and buildup, especially in hard water conditions. This can reduce the efficiency of the quill and result in increased maintenance and cleaning requirements.
- Corrosion: Direct steam injection quills can be susceptible to corrosion, especially when used with acidic or corrosive process streams. This can result in damage to the quill and the need for more frequent replacement.
- Energy costs: Direct steam injection quills can be energy-intensive, especially when used for large-scale heating applications. This can result in increased energy costs and a higher overall operating cost.
- Steam quality: Direct steam injection quills rely on a consistent supply of high-quality steam, which can be a challenge in some manufacturing environments. Poor steam quality can result in reduced quill efficiency and performance.
- Maintenance: Direct steam injection quills require regular maintenance to ensure optimal performance and prevent scaling, buildup, and corrosion. This can result in additional maintenance costs and downtime for the manufacturing process.
Overall, while direct steam injection quills offer several advantages, they also have some disadvantages that need to be considered when selecting a heating method for a manufacturing process. Scaling and buildup, corrosion, energy costs, steam quality, and maintenance requirements are some of the key disadvantages associated with direct steam injection quills.
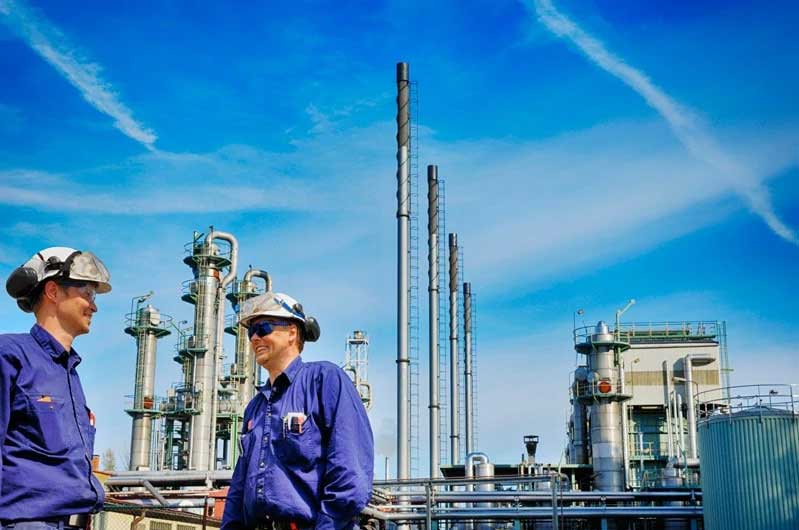
Contact us
Crystal Industrial Syndicate
Phone : +91-22-27563850
Fax: +91-22-67939439
www.crystalindustrial.in
sales@crystalindustrial.in
Crystal Industrial Syndicate from India, manufactures a variety of custom injection quills for a range of industrial processes. Our world-class chemical injection quills are manufactured in India comply with the world’s most stringent certifications. We have clients around the world, from Europe and North America to Africa and the Middle East. Please contact us for details about how we can meet your injection quills requirements. Contact us
Copyright © 2023 by Crystal Industrial Syndicate Pvt Ltd. All rights reserved. www.crystalindustrial.in