Chemical injection quills are important devices that are used in industrial process control to accurately and efficiently inject chemicals into process pipelines. They provide a number of advantages, but also have some limitations that should be considered.
1. Limited Injection Rate
Limited injection rate is an important feature of chemical injection quills in industrial process control. These quills provide a controlled and consistent injection rate of chemicals, which is critical for maintaining process efficiency and product quality.
The injection rate is limited by the design of the chemical injection quill. The quill is designed to provide a specific injection rate, which is based on factors such as the chemical being injected, the pipeline size and flow rate, and the process requirements. This ensures that the chemical is injected at a controlled and consistent rate, which helps to optimize process performance.
The limited injection rate provided by chemical injection quills is particularly important in industries where the injection rate is critical to process efficiency and product quality, such as the food and beverage industry or water treatment. In these industries, even small variations in injection rate can have a significant impact on product quality, resulting in increased costs associated with rework or regulatory compliance.
Overall, limited injection rate is a key feature of chemical injection quills. These devices provide a controlled and consistent injection rate of chemicals, which helps to maintain process efficiency and product quality. This ensures that the process operates at its optimum level, resulting in increased productivity, efficiency, and cost-effectiveness.
2. Chemical Compatibility
Chemical compatibility is an important aspect of chemical injection quills in industrial process control. These quills are designed to be compatible with a wide range of chemicals, which is critical for ensuring that the chemical being injected is delivered safely and effectively.
Chemical injection quills are typically constructed from materials that are resistant to chemical corrosion and degradation, such as stainless steel, PVC, or Teflon. These materials are selected based on the chemical being injected and the operating conditions of the process, to ensure that the quill is compatible with the chemical and does not degrade or contaminate the process.
Chemical compatibility is particularly important in industries where multiple chemicals are used in the process, such as the oil and gas industry or chemical processing. In these industries, the chemicals being injected may be reactive or hazardous, and it is critical that the injection quill is able to handle them safely and effectively.
Overall, chemical compatibility is a key aspect of chemical injection quills. These devices are designed to be compatible with a wide range of chemicals, which ensures that the chemical being injected is delivered safely and effectively. This results in increased process efficiency, productivity, and safety.
3. Pressure Limitations
Pressure limitations are an important consideration when using chemical injection quills in industrial process control. These quills are designed to operate within a specific pressure range, which is critical for ensuring that the chemical injection process is safe and effective.
The pressure limitations of chemical injection quills are determined by their design and construction. The quill is designed to withstand a specific pressure range, which is based on factors such as the pipeline size and flow rate, the chemical being injected, and the process requirements. This ensures that the quill can handle the pressure of the process without failure or damage.
Pressure limitations are particularly important in industries where the process operates at high pressures, such as the oil and gas industry or chemical processing. In these industries, the pressure can be very high and it is critical that the injection quill can handle the pressure without failure or damage. Failure of the quill can result in significant safety hazards, downtime, and loss of productivity.
Overall, pressure limitations are a key consideration when using chemical injection quills. These devices are designed to operate within a specific pressure range, which ensures that the chemical injection process is safe and effective. This results in increased process efficiency, productivity, and safety, while reducing the risk of downtime and loss of productivity.
4. Maintenance
Maintenance is a critical aspect of using chemical injection quills in industrial process control. Proper maintenance of these devices ensures that they continue to operate safely and effectively, and that the chemical injection process is optimized for maximum productivity and efficiency.
Maintenance requirements for chemical injection quills can vary depending on the design and construction of the device, as well as the specific process requirements. However, common maintenance tasks include inspecting the quill for signs of damage or corrosion, cleaning the quill and its components, and replacing worn or damaged parts as needed.
Regular maintenance of chemical injection quills is particularly important in industries where the process requirements may change over time or where the chemicals being injected may be reactive or hazardous. In these industries, regular maintenance ensures that the quill is functioning properly and that any changes to the process requirements are accounted for.
Overall, maintenance is a critical aspect of using chemical injection quills. Regular maintenance of these devices ensures that they continue to operate safely and effectively, resulting in increased process efficiency, productivity, and safety. Proper maintenance also helps to reduce the risk of downtime and loss of productivity, while ensuring that the chemical injection process is optimized for maximum efficiency and effectiveness.
5. Not suitable for all applications
While chemical injection quills have many advantages, they are not suitable for all applications in industrial process control. The effectiveness of these devices can be limited by certain factors, such as the type of chemical being injected or the specific process requirements.
For example, some chemicals may be too viscous or abrasive for the injection quill to handle effectively. Additionally, some processes may require a higher injection rate than what the quill is capable of providing. In these cases, alternative injection methods may need to be considered.
Furthermore, the installation of a chemical injection quill may not be feasible or practical in certain applications due to factors such as space limitations or equipment compatibility issues. It is important to evaluate the specific process requirements and consult with industry experts to determine whether a chemical injection quill is the best solution for a given application.
Overall, while chemical injection quills have many benefits, they are not suitable for all applications. It is important to carefully evaluate the specific process requirements and consult with industry experts to determine whether a chemical injection quill is the best solution for a given application.
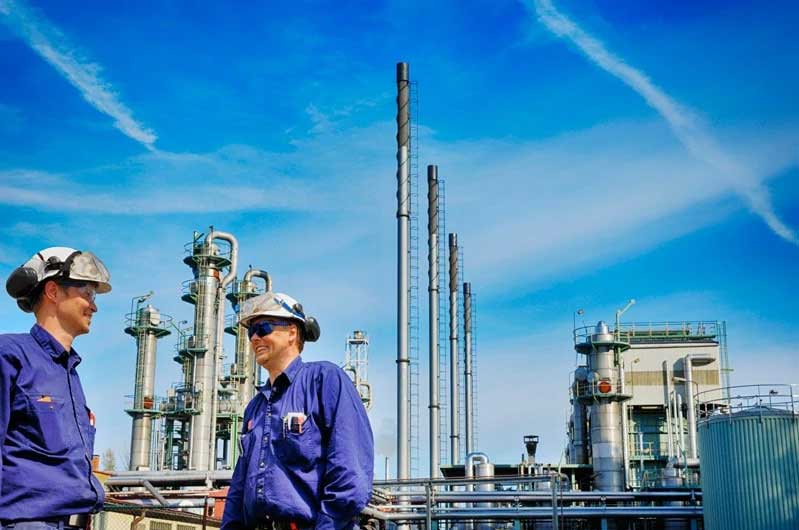
Contact us
Crystal Industrial Syndicate
Phone : +91-22-27563850
Fax: +91-22-67939439
www.crystalindustrial.in
sales@crystalindustrial.in
Crystal Industrial Syndicate from India, manufactures a variety of custom injection quills for a range of industrial processes. Our world-class chemical injection quills are manufactured in India comply with the world’s most stringent certifications. We have clients the world over, from Europe and North America to Africa and the Middle East. Please contact us for details about how we can meet your injection quills requirements. Contact us
Copyright © 2023 by Crystal Industrial Syndicate Pvt Ltd. All rights reserved. www.crystalindustrial.in