Chemical injection quills are important devices that are used in industrial process control to accurately and efficiently inject chemicals into process pipelines. They provide a number of advantages, but also have some limitations that should be considered.
Advantages of Chemical Injection Quills
- Accurate Injection: Chemical injection quills provide an accurate method of injecting chemicals into a pipeline. They ensure that the chemical is delivered exactly where it is needed and in the right amount. This helps to ensure that the process is effective and efficient.
- Increased Safety: Chemical injection quills provide a safe method of injecting chemicals into pipelines. They eliminate the need for manual injection, which can be dangerous due to the risk of exposure to hazardous chemicals.
- Minimal Disruption: Chemical injection quills can be installed without requiring any shutdown of the process. They can be installed while the process is running, which minimizes disruption and downtime.
- Cost-effective: Chemical injection quills are a cost-effective solution for chemical injection. They reduce chemical waste and ensure that the right amount of chemical is used, which saves money on chemical costs.
- Easy to Install and Maintain: Chemical injection quills are easy to install and maintain. They can be installed without the need for specialized tools or equipment and can be easily removed for maintenance.
Limitations of Chemical Injection Quills
- Limited Injection Rate: Chemical injection quills have a limited injection rate, which means they may not be suitable for processes that require high injection rates.
- Chemical Compatibility: Chemical injection quills may not be compatible with all types of chemicals. It is important to ensure that the quill is compatible with the chemical being injected.
- Pressure Limitations: Chemical injection quills have pressure limitations that must be considered. They may not be suitable for processes with high pressure requirements.
- Maintenance: Although chemical injection quills are easy to maintain, regular maintenance is still required to ensure they are functioning properly.
- Not suitable for all applications: Chemical injection quills may not be suitable for all applications. It is important to consider the specific requirements of the process before selecting a chemical injection quill.
Overall, chemical injection quills provide an effective, efficient, and safe method of injecting chemicals into pipelines. However, it is important to consider the advantages and limitations of these devices before selecting one for a particular application.
Click here for limitations of Chemical Injection Quills
Advantage: Accurate Injection
Accurate injection is one of the key advantages of chemical injection quills in industrial process control. These quills provide a precise and controlled method of injecting chemicals into pipelines, which ensures that the chemical is delivered exactly where it is needed and in the right amount. This accurate injection is critical for many industrial processes, as the wrong amount or location of injected chemicals can have serious consequences, including process inefficiencies, environmental damage, or safety hazards.
Chemical injection quills are designed with precision in mind. They typically feature a fixed or adjustable injection rate, which allows the operator to control the flow rate and volume of the injected chemical. Additionally, the quills are designed to provide a uniform distribution of the chemical across the cross-section of the pipeline, which ensures that the chemical is evenly distributed and effectively mixed with the process fluid.
Accurate injection is particularly important for processes that require precise dosing, such as in water treatment, oil and gas production, or food and beverage manufacturing. In these industries, precise dosing can be critical to ensure product quality, meet regulatory requirements, and protect the environment. For example, in water treatment, accurate injection of disinfectants and other chemicals is critical to ensure that the water is safe for human consumption.
Overall, accurate injection is a key advantage of chemical injection quills. These devices provide a precise, controlled, and uniform method of injecting chemicals into pipelines, which ensures that the process is efficient, effective, and safe.
Advantage: Increased Safety
Increased safety is another key advantage of using chemical injection quills in industrial process control. These quills provide a safe method of injecting chemicals into pipelines, which reduces the risk of accidents and injuries associated with manual injection methods.
Manual injection methods involve opening valves or manually pouring chemicals into the process pipeline, which can be dangerous due to the risk of exposure to hazardous chemicals. This can result in chemical burns, inhalation hazards, or other types of injuries to the workers. Additionally, manual injection methods can result in inconsistent dosing, which can lead to process inefficiencies or product quality issues.
Chemical injection quills, on the other hand, eliminate the need for manual injection, reducing the risk of exposure to hazardous chemicals. These quills are designed to safely and accurately inject chemicals into the process pipeline, without the need for workers to be in close proximity to the chemicals. Additionally, chemical injection quills are typically designed to withstand high pressure and temperature, which further enhances their safety in the process environment.
Increased safety is particularly important in industries that deal with hazardous chemicals, such as the oil and gas industry, chemical processing, or mining. In these industries, the use of chemical injection quills can significantly reduce the risk of accidents and injuries, ensuring a safer working environment for the workers.
Overall, increased safety is a key advantage of chemical injection quills. These devices provide a safe and reliable method of injecting chemicals into pipelines, which reduces the risk of accidents and injuries associated with manual injection methods.
Advantage: Minimal Disruption
Minimal disruption is another important advantage of chemical injection quills in industrial process control. These quills can be installed without requiring any shutdown of the process, which minimizes disruption and downtime.
Manual injection methods often require the process to be shut down temporarily while the chemicals are being injected, which can result in production downtime and lost productivity. Chemical injection quills, on the other hand, can be installed while the process is running, which minimizes disruption and downtime. This ensures that the process can continue to run uninterrupted, resulting in increased productivity and efficiency.
Chemical injection quills are typically designed to be easy to install and operate, which further minimizes disruption. They can be installed quickly and easily without the need for specialized tools or equipment, which reduces the time and cost associated with installation. Additionally, chemical injection quills require little to no maintenance, which further minimizes disruption to the process.
Minimal disruption is particularly important in industries that require continuous operation, such as the oil and gas industry or chemical processing. In these industries, any interruption in the process can result in lost productivity, increased costs, or safety hazards.
Overall, minimal disruption is a key advantage of chemical injection quills. These devices can be installed while the process is running, which minimizes disruption and downtime, resulting in increased productivity, efficiency, and safety.
Advantage: Cost-effective
Cost-effectiveness is another key advantage of chemical injection quills in industrial process control. These quills can be a cost-effective solution for injecting chemicals into pipelines, which can lead to significant cost savings over time.
Manual injection methods can be costly due to the labor-intensive nature of the process, which can result in increased labor costs and reduced productivity. Additionally, manual injection methods can result in inconsistent dosing, which can lead to process inefficiencies or product quality issues. This can result in increased costs associated with rework or process downtime.
Chemical injection quills, on the other hand, provide a cost-effective solution for injecting chemicals into pipelines. These devices are typically designed to be easy to install and operate, which reduces the time and cost associated with installation and maintenance. Additionally, chemical injection quills provide accurate and consistent dosing, which can lead to improved process efficiencies and product quality, resulting in cost savings associated with reduced rework and downtime.
Cost-effectiveness is particularly important in industries that are focused on cost control, such as the food and beverage industry or water treatment. In these industries, any cost savings that can be achieved without compromising product quality or regulatory compliance are highly valued.
Overall, cost-effectiveness is a key advantage of chemical injection quills. These devices provide a cost-effective solution for injecting chemicals into pipelines, which can lead to significant cost savings over time, resulting in increased profitability and competitiveness.
Advantage: Easy to Install and Maintain
Easy installation and maintenance is another advantage of using chemical injection quills in industrial process control. These quills are typically designed to be easy to install and maintain, which reduces the time and cost associated with their use.
Chemical injection quills can be installed without requiring any significant modifications to the existing process infrastructure. They can be easily retrofitted into existing pipelines, which reduces the time and cost associated with installation. Additionally, many chemical injection quills are designed to be installed while the process is running, which further reduces downtime and disruption to the process.
Maintenance of chemical injection quills is also typically easy and straightforward. They are designed to be durable and reliable, which reduces the need for frequent maintenance or repairs. Additionally, most chemical injection quills are designed to be self-cleaning, which minimizes the need for manual cleaning and reduces maintenance requirements.
Easy installation and maintenance are particularly important in industries that require high levels of uptime and productivity, such as the oil and gas industry or chemical processing. In these industries, any interruption in the process can result in lost productivity, increased costs, or safety hazards.
Overall, easy installation and maintenance are key advantages of chemical injection quills. These devices can be installed quickly and easily, without requiring significant modifications to the existing process infrastructure. They are also designed to be durable and reliable, which reduces the need for frequent maintenance or repairs, resulting in increased uptime and productivity.
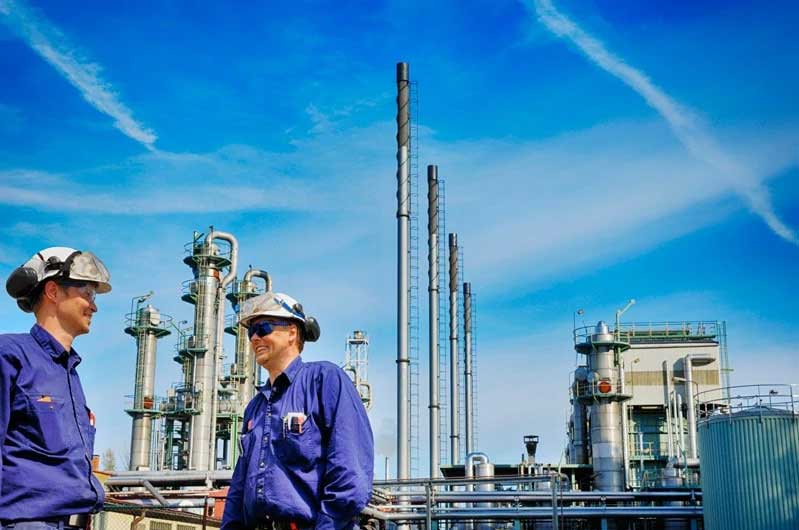
Contact us
Crystal Industrial Syndicate
Phone : +91-22-27563850
Fax: +91-22-67939439
www.crystalindustrial.in
sales@crystalindustrial.in
Crystal Industrial Syndicate from India, manufactures a variety of custom injection quills for a range of industrial processes. Our world-class chemical injection quills are manufactured in India comply with the world’s most stringent certifications. We have clients the world over, from Europe and North America to Africa and the Middle East. Please contact us for details about how we can meet your injection quills requirements. Contact us
Copyright © 2023 by Crystal Industrial Syndicate Pvt Ltd. All rights reserved. www.crystalindustrial.in