The maintenance procedure for chemical injection quills will vary depending on the design and construction of the device, as well as the specific process requirements. However, here are some common maintenance steps that can help ensure the effective and safe operation of the quill:
- Inspect the quill regularly: Inspect the quill and its components for any signs of damage, wear, or corrosion. Check for any leaks or other issues that could affect the performance of the device.
- Clean the quill and its components: Remove any build-up or deposits on the quill and its components. This can be done using a soft brush or a cleaning solution that is compatible with the chemical being injected.
- Replace worn or damaged parts: Replace any parts that are worn, damaged, or corroded. This can include seals, gaskets, or other components that may affect the performance of the quill.
- Lubricate moving parts: Lubricate any moving parts of the quill to ensure smooth operation and reduce wear and tear.
- Test the quill: Test the quill regularly to ensure that it is functioning properly and that any changes to the process requirements are accounted for. This may include checking the injection rate or pressure, or performing a functional test of the quill.
Overall, regular maintenance is critical to ensuring the safe and effective operation of chemical injection quills. Proper maintenance helps to reduce the risk of downtime and loss of productivity, while ensuring that the chemical injection process is optimized for maximum efficiency and effectiveness.
Inspect the quill regularly
Inspecting the chemical injection quill regularly is a critical aspect of the maintenance procedure for this device. This step helps to identify any issues that could affect the performance of the quill or the quality of the injected chemicals.
During the inspection process, the quill and its components should be thoroughly examined for signs of wear, corrosion, or damage. This can include checking the quill for leaks, cracks, or other defects, as well as inspecting the connections between the quill and the injection system.
Regular inspections help to detect issues before they become major problems, which can prevent downtime and reduce the risk of accidents or spills. If any issues are found during the inspection process, they should be addressed promptly to prevent further damage or performance issues.
Overall, regular inspections are a critical aspect of the maintenance procedure for chemical injection quills. By inspecting the quill regularly, operators can identify and address any issues before they become major problems, ensuring that the device continues to operate safely and effectively.
Clean the quill and its components
Cleaning the chemical injection quill and its components is an important maintenance step to ensure the effective and safe operation of the device. Over time, the quill and its components may become clogged with deposits or debris, which can affect the performance of the device and the quality of the injected chemicals.
During the cleaning process, the quill and its components should be thoroughly cleaned to remove any buildup or deposits that may have accumulated. This can be done using a soft brush or a cleaning solution that is compatible with the chemical being injected.
Cleaning the quill and its components helps to ensure that the injected chemicals remain at the desired concentration and that the quill operates efficiently. It also reduces the risk of blockages or other issues that could affect the performance of the device.
Overall, cleaning the chemical injection quill and its components is an important maintenance step to ensure the safe and effective operation of the device. By keeping the quill and its components clean, operators can help to ensure that the device continues to operate at peak performance and that the quality of the injected chemicals remains consistent.
Replace worn or damaged parts
Replacing worn or damaged parts is an important maintenance step for chemical injection quills. Over time, parts of the quill can become worn, damaged, or corroded, which can affect the performance of the device and the quality of the injected chemicals.
During this maintenance step, the worn or damaged parts of the quill should be identified and replaced promptly to ensure that the device continues to operate effectively and safely. This can include seals, gaskets, O-rings, and other components that are critical to the operation of the quill.
Replacing worn or damaged parts helps to ensure that the quill operates at peak performance and that the quality of the injected chemicals remains consistent. It also reduces the risk of leaks or other issues that could affect the safety of the process.
Overall, replacing worn or damaged parts is a critical aspect of the maintenance procedure for chemical injection quills. By replacing these parts promptly, operators can ensure that the quill continues to operate safely and effectively, and that the quality of the injected chemicals remains consistent.
Lubricate moving parts
Lubricating moving parts is an important maintenance step for chemical injection quills. The quill contains several moving parts, such as valves and pistons, that require regular lubrication to operate effectively and efficiently.
During this maintenance step, the moving parts of the quill should be identified, and a suitable lubricant should be applied to them to ensure that they move freely and smoothly. This can include lubricating the valve stems, plungers, and other components that require lubrication.
Lubricating the moving parts of the quill helps to ensure that the device operates smoothly, quietly, and efficiently. It also helps to prevent wear and tear on the moving parts, which can reduce the lifespan of the device.
Overall, lubricating the moving parts of the chemical injection quill is a critical aspect of the maintenance procedure for this device. By keeping the moving parts lubricated, operators can help to ensure that the quill continues to operate at peak performance and that the quality of the injected chemicals remains consistent.
Test the quill
Testing the chemical injection quill is a critical aspect of the maintenance procedure for this device. Regular testing helps to ensure that the quill is operating effectively and that the quality of the injected chemicals remains consistent.
During this maintenance step, the quill should be tested to ensure that it is injecting chemicals at the desired rate and concentration. This can include testing the flow rate, pressure, and chemical concentration to ensure that they are within the desired parameters.
Testing the chemical injection quill helps to identify any issues or deviations from the desired parameters, which can then be addressed through appropriate maintenance procedures. This helps to ensure that the device continues to operate safely and effectively, and that the quality of the injected chemicals remains consistent.
Overall, testing the chemical injection quill is a critical aspect of the maintenance procedure for this device. By regularly testing the quill, operators can help to identify any issues and ensure that the quill continues to operate at peak performance and that the quality of the injected chemicals remains consistent.
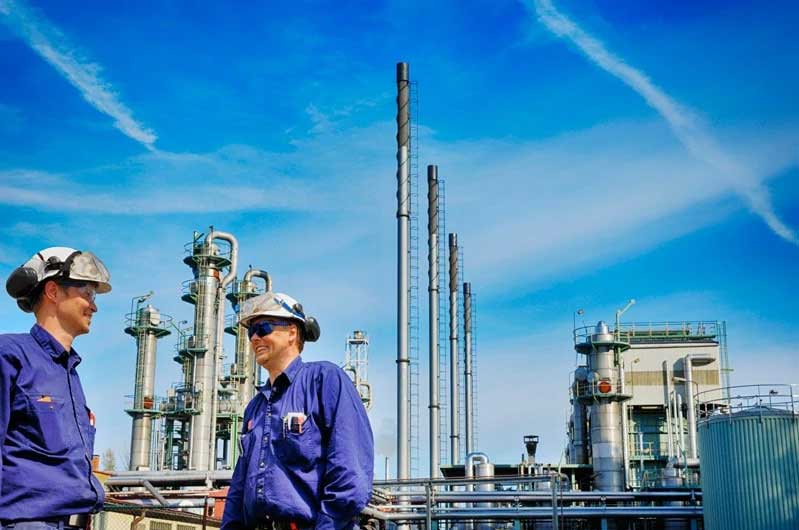
Contact us
Crystal Industrial Syndicate
Phone : +91-22-27563850
Fax: +91-22-67939439
www.crystalindustrial.in
sales@crystalindustrial.in
Crystal Industrial Syndicate from India, manufactures a variety of custom injection quills for a range of industrial processes. Our world-class chemical injection quills are manufactured in India comply with the world’s most stringent certifications. We have clients the world over, from Europe and North America to Africa and the Middle East. Please contact us for details about how we can meet your injection quills requirements. Contact us
Copyright © 2023 by Crystal Industrial Syndicate Pvt Ltd. All rights reserved. www.crystalindustrial.in