The process of designing a chemical injection quill involves several key steps, including:
- Determining the injection point location: The injection point must be located in the process flow where the chemical can mix and react effectively with the process fluid.
- Calculating the injection rate and pressure: The injection rate and pressure must be carefully calculated to ensure that the correct amount of chemical is injected into the process fluid at the correct pressure.
- Selecting the appropriate quill diameter and length: The quill diameter and length must be selected based on the injection rate and pressure, as well as the desired mixing and reaction.
- Choosing the appropriate back pressure valve: The type and placement of the back pressure valve must be selected to ensure proper pressure regulation and flow control.
- Selecting compatible materials: The materials used for the quill and back pressure valve must be compatible with the process fluid and chemical being injected, and must be resistant to corrosion and degradation.
- Finalizing the design: Once all of these considerations have been taken into account, the final design can be developed and refined to optimize performance and durability.
Determining the injection point location
Determining the injection point location is one of the crucial steps in designing a chemical injection quill. The injection point location should be selected based on the process requirements and should be suitable for the type of chemical being injected. It is important to consider factors such as fluid flow, pressure, and temperature to determine the optimal location for the injection point. The injection point location can be at the side, bottom or top of the pipeline. It is also important to ensure that the injection point location is accessible for maintenance and replacement of the quill. The location of the back pressure valve should also be considered while determining the injection point location. Overall, the injection point location should be selected after careful consideration of the process requirements and the factors that affect the chemical injection system.
Calculating the injection rate and pressure
Calculating the injection rate and pressure is a critical step in the design of a chemical injection quill. It involves determining the required flow rate of the chemical to be injected and the pressure at which it should be injected. The flow rate and pressure are dependent on the chemical being injected, the application, and the injection point location.
The injection rate is usually expressed in gallons per minute (GPM) or liters per minute (LPM), and the injection pressure is typically measured in pounds per square inch (PSI) or bar. The required injection rate and pressure can be determined by considering factors such as the desired chemical concentration, the system flow rate, the back pressure, and the chemical compatibility with the system material.
Once the injection rate and pressure are calculated, they can be used to select an appropriate injection quill design, including the quill length and diameter, the material of construction, and the back pressure valve type and placement. It is essential to ensure that the selected injection quill design can deliver the required injection rate and pressure while maintaining a safe and reliable operation.
Selecting the appropriate quill diameter and length
Selecting the appropriate quill diameter and length is an important step in designing a chemical injection quill. The diameter of the quill should be chosen based on the required flow rate of the chemical, while the length of the quill should be selected based on the depth of the injection point. The quill should be long enough to ensure that the chemical is being injected at the desired depth, but not so long that it becomes difficult to handle or introduces unnecessary restrictions in the system. The diameter of the quill should also be selected based on the pressure and flow rate requirements, as larger diameters can accommodate higher flow rates and lower pressure drops. The length of the quill can be adjusted by using extensions or coupling multiple quills together, but this should be done with care to avoid excessive pressure drops or other flow restrictions.
Choosing the appropriate back pressure valve
Choosing the appropriate back pressure valve is an important step in designing a chemical injection quill. The type of back pressure valve that is selected will depend on the specific application and the desired level of control over the injection process. Some common types of back pressure valves include spring-loaded, diaphragm, piston-style, and fixed orifice valves.
When selecting a back pressure valve, it is important to consider factors such as the flow rate of the chemical being injected, the operating pressure and temperature, and the desired level of control over the injection process. The valve should be able to maintain a constant pressure and flow rate, and should be able to handle the specific chemical being injected without corroding or degrading over time.
In addition to selecting the appropriate type of back pressure valve, it is also important to consider the placement of the valve within the injection quill. The valve should be located at a point where it can effectively control the flow of the chemical being injected, while also allowing for easy maintenance and replacement as needed. Proper installation and maintenance of the back pressure valve is critical to ensuring the safe and effective operation of the chemical injection quill.
Selecting compatible materials
Selecting compatible materials is an important step in designing a chemical injection quill. The materials used should be able to withstand the pressure, temperature, and the chemical being injected. Compatibility between the materials and the chemical should also be considered to prevent any negative reactions or damage to the system. The material options for the quill itself, as well as the fittings, tubing, and any other components, should be evaluated to ensure they are suitable for the intended application. Factors such as corrosion resistance, mechanical strength, and temperature resistance should also be taken into account during the material selection process.
Finalizing the design
After considering all the factors and design considerations, the final step is to finalize the design of the chemical injection quill. This involves ensuring that all the chosen materials and components are compatible, and the design meets the requirements for the application.
The design should be reviewed by a qualified engineer to ensure that it meets all the applicable codes and standards. The engineer should also check that the injection point location, quill diameter and length, injection rate and pressure, and back pressure valve selection are appropriate for the application.
Once the design is finalized, the chemical injection quill can be fabricated, assembled, and installed. The installation should be carried out by trained personnel, and the chemical injection system should be tested to ensure that it is operating safely and effectively. Regular maintenance and monitoring should also be performed to ensure that the system is functioning as intended.
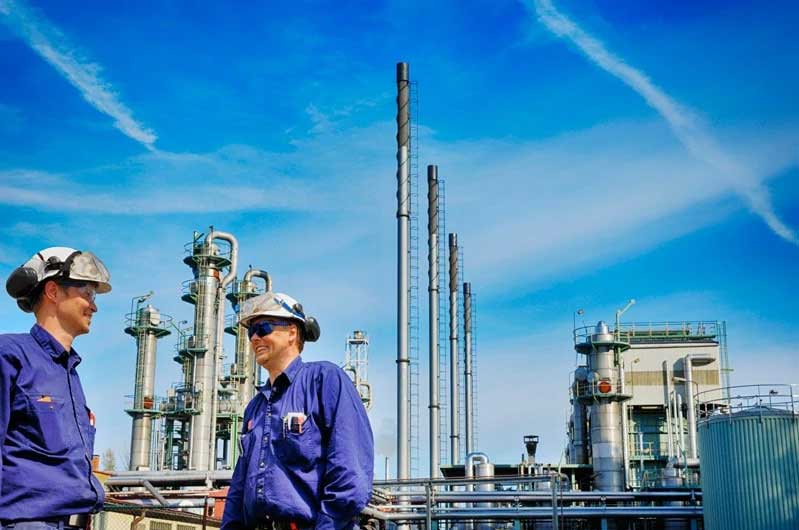
Contact us
Crystal Industrial Syndicate
Phone : +91-22-27563850
Fax: +91-22-67939439
www.crystalindustrial.in
sales@crystalindustrial.in
Crystal Industrial Syndicate from India, manufactures a variety of custom injection quills for a range of industrial processes. Our world-class chemical injection quills are manufactured in India comply with the world’s most stringent certifications. We have clients the world over, from Europe and North America to Africa and the Middle East. Please contact us for details about how we can meet your injection quills requirements. Contact us
Copyright © 2023 by Crystal Industrial Syndicate Pvt Ltd. All rights reserved. www.crystalindustrial.in