In addition to the factors to consider when designing a chemical injection quill, there are several design considerations to consider. These considerations include:
- Quill length and diameter: The length and diameter of the quill must be designed to ensure proper injection and mixing of the chemical with the process fluid.
- Injection point location: The location of the injection point must be carefully selected to ensure that the chemical is injected into the process fluid at the optimal location for mixing and reaction.
- Back pressure valve type and placement: The type and placement of the back pressure valve will depend on the specific requirements of the application, and must be selected to ensure proper pressure regulation and flow control.
- Injection rate and pressure: The injection rate and pressure must be carefully calculated to ensure that the correct amount of chemical is injected into the process fluid at the correct pressure.
- Material selection: The materials used for the quill and back pressure valve must be carefully selected to ensure compatibility with the process fluid and the chemical being injected, as well as resistance to corrosion and degradation.
Quill length and diameter
Quill length and diameter are important design considerations when designing a chemical injection quill. The length and diameter of the quill will impact the flow rate of the chemical being injected and the overall performance of the system.
The length of the quill should be selected to ensure that the chemical is injected at the correct location within the process stream. This may involve determining the optimal injection point based on the process conditions and ensuring that the quill is long enough to reach this point.
The diameter of the quill will impact the flow rate of the chemical being injected. A larger diameter quill will allow for a higher flow rate, while a smaller diameter quill will provide a lower flow rate. The diameter of the quill should be selected to match the required flow rate and the characteristics of the chemical being injected.
In addition to length and diameter, the design of the quill should also take into account factors such as the materials used, the type of injection mechanism, and the need for a back pressure valve. By considering these factors, the quill can be designed to ensure optimal performance and reliability, while also meeting the specific requirements of the application.
Injection point location
Injection point location is a critical design consideration when designing a chemical injection quill. The location where the chemical is injected into the process stream can have a significant impact on the effectiveness of the injection and the overall performance of the system.
The injection point should be selected to ensure that the chemical is dispersed evenly throughout the process stream and that it is injected at the correct location. This may involve determining the optimal injection point based on the process conditions and ensuring that the quill is long enough to reach this point.
The location of the injection point may also impact the flow rate and pressure of the system. For example, if the injection point is located in a high-pressure area, the quill may need to be designed with a back pressure valve to maintain a consistent flow rate and pressure. Conversely, if the injection point is located in a low-pressure area, the quill may need to be designed with a flow restrictor to prevent over-injection.
By carefully considering the injection point location, the design of the quill can be optimized to ensure that the chemical is injected at the right location and that the system operates at peak performance. This can help to improve process efficiency, reduce costs, and ensure consistent product quality.
Back pressure valve type and placement
When designing a chemical injection quill, the selection of an appropriate back pressure valve type and its placement is an important design consideration. The back pressure valve is responsible for controlling the flow rate of the injected chemical and maintaining a constant pressure in the pipeline. There are different types of back pressure valves, including spring-loaded, diaphragm, piston-style, and fixed orifice valves, each with its own advantages and limitations. The selection of the appropriate type of back pressure valve depends on the specific application and the flow rate and pressure requirements.
The placement of the back pressure valve in the chemical injection quill is also critical for the efficient operation of the system. Placing the valve too far from the injection point can result in inaccurate injection rates, while placing it too close can lead to clogging and inefficient chemical injection. It is important to consider the physical layout of the pipeline and the specific application requirements when determining the appropriate placement of the back pressure valve in the chemical injection quill.
Injection rate and pressure
The injection rate and pressure are important design considerations for a chemical injection quill. The injection rate is the amount of chemical that needs to be injected into the system per unit of time, and it depends on the application requirements. The injection pressure is the pressure at which the chemical is injected into the system and is determined by the downstream pressure and the pressure drop across the quill.
The injection rate and pressure are typically controlled by the selection of the appropriate quill diameter, length, and injection point location. A properly designed quill ensures that the chemical injection rate and pressure remain consistent over time, which helps to maintain the chemical process and system efficiency. Additionally, the back pressure valve also plays an important role in controlling the injection pressure, which in turn affects the injection rate. Therefore, it is crucial to select the appropriate back pressure valve type and placement to ensure accurate control of injection rate and pressure.
Material selection
Material selection is a critical design consideration when it comes to chemical injection quills. The materials used in the construction of the quill must be compatible with the chemical being injected and the environmental conditions in which the quill will be operating. Corrosive chemicals, for example, require the use of corrosion-resistant materials to prevent damage to the quill, and to ensure that the chemical is delivered safely to the target location.
Common materials used in the construction of chemical injection quills include stainless steel, PVC, and PTFE. Stainless steel is often used for its durability and corrosion resistance, while PVC and PTFE are commonly used for their chemical resistance.
The material selection process should also consider the cost and availability of the chosen material, as well as any industry or regulatory standards that must be met. Choosing the appropriate materials for the construction of the quill ensures that the device will perform safely and effectively, and can help to prevent equipment failure and costly downtime.
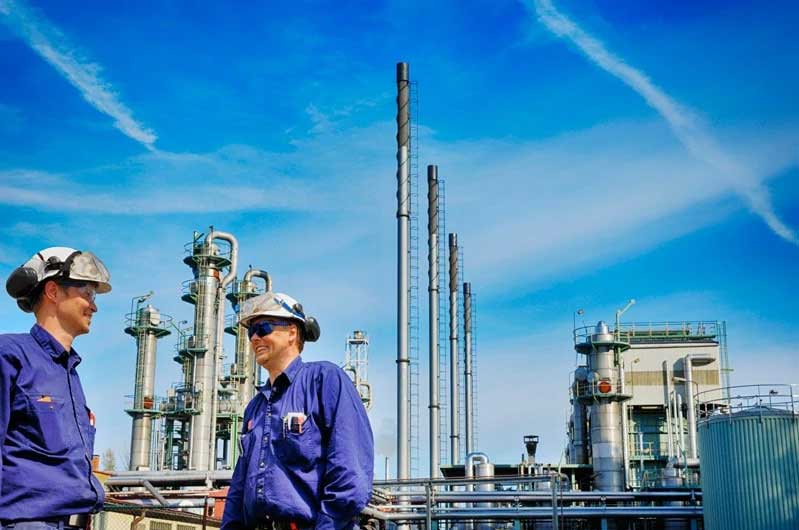
Contact us
Crystal Industrial Syndicate
Phone : +91-22-27563850
Fax: +91-22-67939439
www.crystalindustrial.in
sales@crystalindustrial.in
Crystal Industrial Syndicate from India, manufactures a variety of custom injection quills for a range of industrial processes. Our world-class chemical injection quills are manufactured in India comply with the world’s most stringent certifications. We have clients the world over, from Europe and North America to Africa and the Middle East. Please contact us for details about how we can meet your injection quills requirements. Contact us
Copyright © 2023 by Crystal Industrial Syndicate Pvt Ltd. All rights reserved. www.crystalindustrial.in