Choosing the right injection quill for your paint and coatings process is important to ensure optimal performance, enhanced safety, and cost-effectiveness. Here are some key factors to consider when choosing an injection quill:
- Flow rate and pressure: Consider the flow rate and pressure requirements of your paint and coatings process, and choose an injection quill that can handle these demands.
- Material compatibility: Ensure that the materials used in the injection quill are compatible with the fluid you will be using, such as paint or coating materials, to prevent contamination or other adverse reactions.
- Size and dimension: Choose an injection quill with a size and dimension that is suitable for your pipeline, and ensure that it can be easily installed and connected.
- Venting and straining: Consider the venting and straining capabilities of the injection quill, and ensure that it can effectively control fluid pressure and filter out impurities to enhance safety and reduce waste.
- Maintenance and cleaning: Choose an injection quill that is easy to maintain and clean, and has removable components for quick and easy access.
- Quality and durability: Ensure that the injection quill is made of high-quality materials and is robustly constructed to ensure durability and long-lasting performance.
- Cost-effectiveness: Consider the cost of the injection quill, and ensure that it provides cost-effective benefits such as reduced waste, improved efficiency, enhanced safety, and more.
By considering these key factors, you can choose the right injection quill for your paint and coatings process and ensure that it provides the desired benefits and performance.
1. Flow rate and pressure
Flow rate and pressure are two important factors to consider when choosing an injection quill for your paint and coatings process. The flow rate is the amount of fluid that is flowing through the pipeline, and the pressure is the force with which the fluid is flowing.
In order to ensure optimal performance, it is important to choose an injection quill that can handle the flow rate and pressure requirements of your paint and coatings process. If the flow rate is too high or the pressure is too low, the fluid may not be evenly distributed or may not reach the desired location. On the other hand, if the flow rate is too low or the pressure is too high, the fluid may not be effectively injected or may cause damage to the pipeline.
Therefore, it is important to accurately assess the flow rate and pressure requirements of your paint and coatings process and choose an injection quill that can handle these demands. This will help to ensure that the fluid is effectively injected and distributed, and that the process runs smoothly and efficiently.
2. Material compatibility
Material compatibility is another important factor to consider when choosing an injection quill for your paint and coatings process. It is important to ensure that the materials used in the injection quill are compatible with the fluid you will be using, such as paint or coating materials, to prevent contamination or other adverse reactions.
For example, some paint or coating materials may react with certain materials used in the construction of the injection quill, leading to corrosion or other forms of damage. This can not only affect the performance of the injection quill, but can also cause harm to the environment or to people working in close proximity to the pipeline.
Therefore, it is important to carefully consider the material compatibility of the injection quill and the fluid it will be used with, and to choose an injection quill that is made of materials that are suitable for your paint and coatings process. This will help to ensure optimal performance, reduce the risk of contamination or damage, and enhance safety.
3. Size and dimension
The size and dimensions of an injection quill are also important factors to consider when choosing the right one for your paint and coatings process. The size and dimensions of the injection quill will affect the flow rate and pressure, as well as the overall performance of the process.
It is important to choose an injection quill that is appropriately sized for your pipeline, taking into account the diameter of the pipeline and the required flow rate. If the injection quill is too small, the flow rate may be restricted and the process may not run effectively. On the other hand, if the injection quill is too large, the fluid may not be distributed evenly, leading to waste and inefficiencies.
In addition, the dimensions of the injection quill, such as the length and shape, can also affect the performance of the process. For example, a longer injection quill may provide more time for the fluid to mix and distribute evenly, while a more compact design may be easier to install and maintain.
Therefore, it is important to carefully consider the size and dimensions of the injection quill and choose one that is appropriately sized and dimensioned for your paint and coatings process. This will help to ensure optimal performance, reduce waste and inefficiencies, and enhance the overall effectiveness of the process.
4. Venting and straining
Venting and straining are important considerations when choosing an injection quill for your paint and coatings process. The vent on the injection quill allows air to escape from the pipeline, which is necessary to maintain proper fluid flow. The strainer, on the other hand, helps to remove any particles or debris that may be present in the fluid, preventing clogs and other issues in the pipeline.
It is important to choose an injection quill that is equipped with an effective vent and strainer, as these features can have a significant impact on the performance of the process. A poorly designed vent or strainer can lead to reduced flow rate and pressure, as well as potential clogs and other issues in the pipeline.
In addition, the vent and strainer should be compatible with the fluid being used, and should be easy to access and maintain. For example, some strainer designs may be more effective for certain fluids, while others may be more suitable for different flow rates.
Therefore, when choosing an injection quill for your paint and coatings process, it is important to carefully consider the venting and straining capabilities of the injection quill and choose one that is equipped with effective vents and strainers that are compatible with your fluid and process. This will help to ensure optimal performance, reduce waste and inefficiencies, and enhance the overall effectiveness of the process.
6. Maintenance and cleaning
Maintenance and cleaning are also important considerations when choosing an injection quill for your paint and coatings process. The injection quill is subject to wear and tear over time, and it is important to choose an injection quill that is easy to maintain and clean in order to ensure optimal performance and longevity.
It is important to choose an injection quill that is designed with maintenance and cleaning in mind, with features such as easily accessible parts and simple disassembly for cleaning. Some injection quills may also be designed with materials that are resistant to corrosion and wear, helping to extend the lifespan of the quill.
In addition, the injection quill should be designed with ease of use in mind, with features such as straightforward installation and easy access to the vent and strainer. This can help to reduce the time and effort required for maintenance and cleaning, as well as minimize downtime and disruptions to the process.
Therefore, when choosing an injection quill for your paint and coatings process, it is important to carefully consider the maintenance and cleaning capabilities of the injection quill and choose one that is designed with ease of use and maintenance in mind. This will help to ensure optimal performance, reduce waste and inefficiencies, and enhance the overall effectiveness of the process.
6. Quality and durability
Quality and durability are critical factors to consider when choosing an injection quill for your paint and coatings process. The injection quill is a key component in the process and it is important to choose a high-quality, durable quill that can perform effectively over time.
It is important to choose an injection quill that is manufactured from high-quality materials that are resistant to corrosion and wear. This will help to extend the lifespan of the quill and reduce the need for frequent replacements. In addition, a high-quality injection quill should be designed with features that minimize the risk of leaks, clogs, and other issues, helping to ensure reliable performance over time.
The durability of the injection quill is also impacted by the manufacturing process and quality control measures in place. It is important to choose an injection quill that is manufactured by a reputable company with a proven track record of producing high-quality products. This will help to ensure that the quill is of the highest quality and that it will perform effectively over time.
Therefore, when choosing an injection quill for your paint and coatings process, it is important to carefully consider the quality and durability of the quill and choose one that is manufactured from high-quality materials and manufactured by a reputable company. This will help to ensure optimal performance, reduce waste and inefficiencies, and enhance the overall effectiveness of the process.
7. Cost effectiveness
Cost-effectiveness is an important factor to consider when choosing an injection quill for your paint and coatings process. While it may be tempting to choose the lowest cost option, it is important to consider the long-term impact of the injection quill on the overall process and budget.
An injection quill that is not cost-effective may require frequent replacements, repairs, or maintenance, which can result in higher costs over time. Additionally, an injection quill that is not of high quality or that is prone to leaks, clogs, or other issues may result in lost productivity, reduced efficiency, and increased waste, further increasing costs.
Therefore, when choosing an injection quill for your paint and coatings process, it is important to consider the overall cost-effectiveness of the quill and choose one that provides the best value for the investment. This may mean choosing a higher quality, more durable quill that is designed for optimal performance and efficiency, even if it has a higher upfront cost.
By carefully considering the cost-effectiveness of the injection quill, you can help to ensure that you are making the best investment for your paint and coatings process, reducing costs over time and enhancing the overall effectiveness of the process.
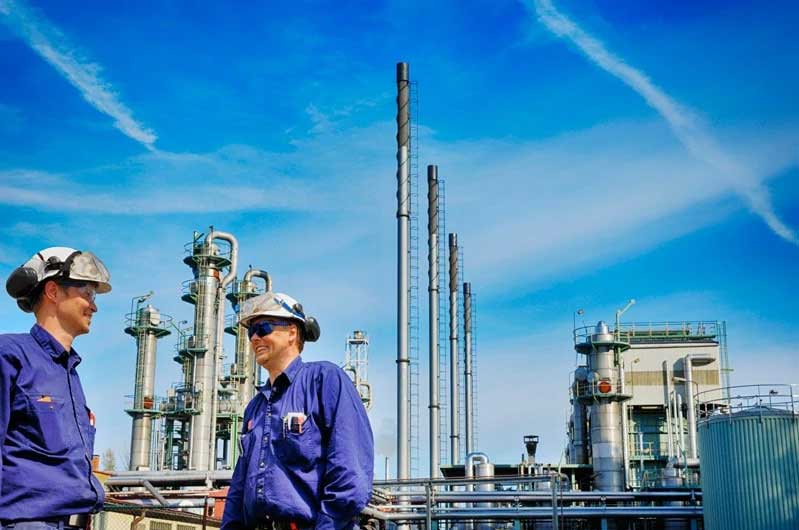
Contact us
Crystal Industrial Syndicate
Phone : +91-22-27563850
Fax: +91-22-67939439
www.crystalindustrial.in
sales@crystalindustrial.in
Crystal Industrial Syndicate from India, manufactures a variety of custom injection quills for a range of industrial processes. Our world-class chemical injection quills are manufactured in India comply with the world’s most stringent certifications. We have clients the world over, from Europe and North America to Africa and the Middle East. Please contact us for details about how we can meet your injection quills requirements. Contact us
Copyright © 2023 by Crystal Industrial Syndicate Pvt Ltd. All rights reserved. www.crystalindustrial.in