The fluid is delivered to the inlet of the injection quill, and is then directed through the body of the quill and into the outlet. The outlet of the quill is connected to the pipeline, and the fluid is injected into the pipeline through this connection.
Injection quills are used in the paint and coatings industry to efficiently and accurately inject fluid into a pipeline. The basic components of an injection quill include the body, inlet, outlet, diffuser, strainer, mounting flange, and vent.
As the fluid moves through the body of the injection quill, it is diffused and dispersed by the diffuser, which helps to control the flow rate and pressure of the fluid. The strainer helps to filter out any impurities in the fluid, ensuring that only the clean, paint or coating material reaches the pipeline.
The mounting flange of the injection quill is used to secure the quill in place and connect it to the pipeline. The vent at the top of the body of the injection quill allows air or gas to escape as the fluid is being injected, which helps to maintain a stable fluid pressure within the system and prevent the buildup of pressure that could cause damage to the pipeline or the injection quill.
Overall, the injection quill provides an efficient and effective way to inject fluid into a pipeline in the paint and coatings industry, while also offering improved control over the flow rate and pressure, reduced waste, enhanced safety, and reduced risk of contamination.
Benefits of using injection quills in paints and coatings processes
Injection quills provide a number of benefits when used in the paint and coatings industry:
- Increased efficiency and accuracy: By providing precise control over the flow rate and pressure of the fluid, injection quills help to improve the efficiency and accuracy of fluid injection, which in turn results in more efficient use of paint and coatings materials.
- Improved control over fluid flow: The diffuser, strainer, and vent in an injection quill help to control the flow rate and pressure of the fluid, which improves the ability to manage the fluid injection process.
- Reduced waste: With improved control over the flow rate and pressure of the fluid, injection quills help to minimize waste and improve material utilization, which can lead to cost savings over time.
- Enhanced safety: The use of injection quills helps to reduce the risk of contamination and improve the overall safety of the fluid injection process, which is particularly important when working with potentially hazardous materials like paint and coatings.
- Easy installation and maintenance: Injection quills are designed to be easy to install and maintain, which helps to minimize downtime and reduce the overall cost of operation.
Overall, the use of injection quills for paint and coatings provides a number of benefits that help to improve efficiency, control, safety, and cost-effectiveness in the fluid injection process.
Increased efficiency and accuracy
Increased efficiency and accuracy is one of the key benefits of using injection quills in the paint and coatings industry. By providing precise control over the flow rate and pressure of the fluid, injection quills help to ensure that the fluid is delivered to the pipeline in the most efficient and accurate manner possible.
Injection quills are equipped with a diffuser that helps to disperse and control the flow of fluid, and a strainer that filters out any impurities, ensuring that only clean fluid reaches the pipeline. This results in a more consistent and controlled fluid flow, which in turn reduces waste and minimizes the risk of contamination.
In addition, the use of injection quills helps to improve the accuracy of fluid delivery by reducing the risk of over- or under-delivery of fluid. This results in more efficient use of paint and coatings materials, which in turn can lead to cost savings over time.
Overall, the increased efficiency and accuracy of fluid delivery that is possible with the use of injection quills helps to improve the quality and efficiency of the paint and coatings process, while also reducing the risk of waste and contamination.
Improved control over fluid flow
Improved control over fluid flow is another key benefit of using injection quills in the paint and coatings industry. The diffuser, strainer, and vent in an injection quill all play a role in controlling the flow rate and pressure of the fluid, which helps to ensure that the fluid is delivered to the pipeline in a consistent and controlled manner.
The diffuser in the injection quill helps to disperse the fluid as it moves through the body of the quill, which helps to control the flow rate and pressure of the fluid. This improved control over the fluid flow helps to reduce the risk of over- or under-delivery of fluid, which in turn helps to minimize waste and improve material utilization.
The strainer in the injection quill filters out any impurities in the fluid, which helps to prevent contamination and improve the overall quality of the paint and coatings process.
The vent at the top of the injection quill allows air or gas to escape as the fluid is being injected, which helps to maintain a stable fluid pressure within the system and prevent the buildup of pressure that could cause damage to the pipeline or the injection quill.
Overall, the improved control over fluid flow that is possible with the use of injection quills helps to ensure a more consistent and accurate delivery of fluid to the pipeline, while also reducing the risk of waste and contamination.
Reduced waste
Reduced waste is a significant benefit of using injection quills in the paint and coatings industry. With improved control over the flow rate and pressure of the fluid, injection quills help to minimize waste and improve material utilization.
Injection quills help to ensure a more consistent and accurate delivery of fluid to the pipeline, which helps to reduce the risk of over- or under-delivery of fluid. This results in more efficient use of paint and coatings materials, which in turn can lead to cost savings over time.
In addition, the strainer in the injection quill helps to filter out any impurities in the fluid, which helps to prevent contamination and improve the overall quality of the paint and coatings process. This helps to reduce the risk of waste and minimize the need for rework or additional material, which can further reduce the overall cost of operation.
Overall, the reduced waste that is possible with the use of injection quills helps to improve the efficiency, quality, and cost-effectiveness of the paint and coatings process.
Enhanced safety
Enhanced safety is another important benefit of using injection quills in the paint and coatings industry. Injection quills help to control the flow rate and pressure of the fluid, which minimizes the risk of damage to the pipeline or the injection quill, and reduces the risk of leaks or spills.
The vent in the injection quill allows air or gas to escape as the fluid is being injected, which helps to maintain a stable fluid pressure within the system and prevent the buildup of pressure that could cause damage to the pipeline or the injection quill.
In addition, the strainer in the injection quill helps to filter out any impurities in the fluid, which helps to prevent contamination and improve the overall quality of the paint and coatings process. This reduces the risk of adverse reactions or other safety hazards associated with contaminated materials.
The mounting flange in the injection quill provides a secure and stable connection to the pipeline, which helps to prevent leaks or disconnections that could cause damage or safety hazards.
Overall, the enhanced safety that is possible with the use of injection quills helps to protect the pipeline, workers, and the environment, and minimizes the risk of accidents or other safety hazards in the paint and coatings process.
Easy installation and maintenance
Easy installation and maintenance are additional benefits of using injection quills in the paint and coatings industry. Injection quills are designed for quick and simple installation, and can be easily connected to the pipeline using the mounting flange.
The compact design of the injection quill makes it easy to access for maintenance and cleaning, and the various components can be easily removed and replaced as needed. This helps to minimize downtime and maintenance costs, and ensures that the injection quill continues to perform at optimal levels.
In addition, the use of high-quality materials and robust construction helps to ensure that injection quills are durable and long-lasting, which further minimizes the need for maintenance or replacement.
Overall, the easy installation and maintenance of injection quills helps to ensure that they continue to perform at optimal levels and provide the desired benefits of increased efficiency, improved control, reduced waste, enhanced safety, and more.
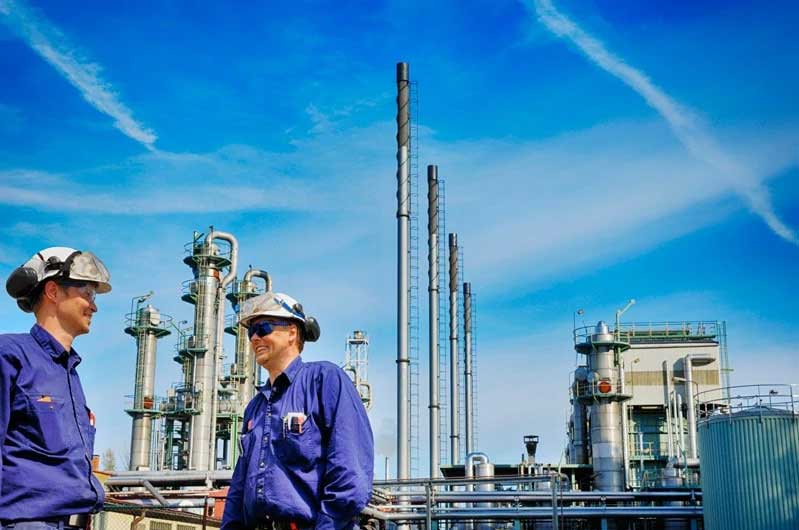
Contact us
Crystal Industrial Syndicate
Phone : +91-22-27563850
Fax: +91-22-67939439
www.crystalindustrial.in
sales@crystalindustrial.in
Crystal Industrial Syndicate from India, manufactures a variety of custom injection quills for a range of industrial processes. Our world-class chemical injection quills are manufactured in India comply with the world’s most stringent certifications. We have clients the world over, from Europe and North America to Africa and the Middle East. Please contact us for details about how we can meet your injection quills requirements. Contact us
Copyright © 2023 by Crystal Industrial Syndicate Pvt Ltd. All rights reserved. www.crystalindustrial.in