Two common mistakes that happen during the construction of the body of any injection quill are poor welds or joining techniques and insufficient wall thickness.
Poor welds or joining techniques
The body must be properly joined or welded to ensure that it is strong, durable, and leak-free.
If the body is not properly joined or welded, it may leak or separate, leading to system failures and environmental releases. In addition, poor welds or joining techniques can weaken the body, making it more susceptible to deformation or failure under pressure.
To avoid this mistake, it is essential to use a qualified welder or fabricator who is experienced in welding and joining materials that are suitable for the specific application. The welder or fabricator should use the appropriate welding or joining techniques and materials, and should follow all industry standards and codes.
In addition, it is important to conduct a thorough inspection of the welds or joints after they have been completed to ensure that they are free from defects and that they meet all quality standards.
By ensuring that the body of an injection quill is properly joined or welded, you can ensure that it will perform as intended, provide long-term, reliable service, and avoid costly repairs or replacements.
Insufficient Wall Thickness
Insufficient wall thickness is another mistake that can occur during the construction of the body of an injection quill. The wall thickness of the body must be sufficient to withstand the internal pressure and external loads that the device will be subjected to during operation.
If the wall thickness is insufficient, the body may be subject to deformation or failure under pressure. This can result in leaks, spills, and other environmental releases, as well as harm to people and property.
To avoid this mistake, it is important to consult with an engineer who specializes in fluid and gas transfer systems. The engineer will use mathematical models and fluid dynamics simulations to determine the required wall thickness for the specific application.
In addition, it is essential to use high-quality materials and to manufacture the body to the correct specifications. The manufacturer should also perform regular quality control checks and inspections to ensure that the wall thickness is consistent and meets the required specifications.
By ensuring that the body of an injection quill has sufficient wall thickness, you can ensure that it will perform as intended, provide long-term, reliable service, and avoid costly repairs or replacements.
The body of an injection quill is one of the most important components of the device. It serves as the main housing for the other components and protects them from the environment. The body is typically made of a corrosion-resistant material, such as stainless steel or plastic, to ensure that it can withstand the conditions in the pipeline or storage tank. The body of an injection quill must be strong and durable, as it is subjected to the pressure and flow of the fluid or gas being introduced. It must also be able to withstand the corrosive or abrasive properties of the fluid or gas. The size and shape of the body can vary depending on the flow rate and pressure requirements of the specific application.
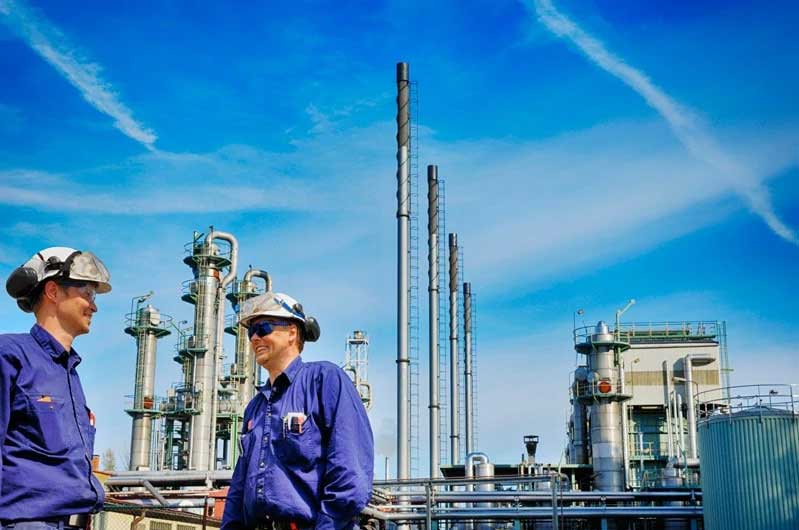
Contact us
Crystal Industrial Syndicate
Phone : +91-22-27563850
Fax: +91-22-67939439
www.crystalindustrial.in
sales@crystalindustrial.in
Crystal Industrial Syndicate from India, manufactures a variety of custom injection quills for a range of industrial processes. Our world-class chemical injection quills are manufactured in India comply with the world’s most stringent certifications. We have clients the world, from Europe and North America to Africa and the Middle East. Please contact us for details about how we can meet your injection quills requirements. Contact us
Copyright © 2023 by Crystal Industrial Syndicate Pvt Ltd. All rights reserved. www.crystalindustrial.in