The purpose of the assembly stage is to connect the injection quill to the process line and ensure that the connection is secure and leak-free.
- Attaching the injection quill to the process line: The injection quill is attached to the process line and securely fastened.
- Installing nuts and gaskets: The appropriate nuts and gaskets are installed to ensure a leak-free connection between the injection quill and the process line.
- Verifying proper connections: The connections are checked to ensure that the injection quill is securely attached to the process line and that there are no leaks.
Attaching the injection quill to the process line
Attaching the injection quill to the process line is a crucial step in the Assembly stage of the installation process for injection quills manufactured in India. The goal of this step is to securely connect the quill to the process line so that it can be used for its intended purpose, which is typically to inject a fluid or gas into the process stream.
To attach the quill to the process line, various tools and techniques may be used, such as flanges, bolts, gaskets, or welding. The specific tools and techniques used will depend on the manufacturer’s specifications and guidelines for the specific type of injection quill being installed, as well as the type of process line and the materials used.
It is important to follow the manufacturer’s instructions carefully when attaching the quill to the process line to ensure a secure and leak-free connection. The bolts must be tightened to the correct torque, and gaskets or seals must be used to prevent leaks.
Once the quill has been attached to the process line, it is important to check for leaks and verify that the connection is secure. This can be done by performing a pressure test or a leak test. If any leaks are found, they must be addressed before the installation can be considered complete.
After the quill has been attached to the process line and the connection has been verified to be secure, the next step in the installation process can proceed. However, it is important to take the time to ensure that the quill has been properly attached to the process line to ensure that it functions as intended and to prevent any safety or environmental incidents.
Installing nuts and gaskets
Installing nuts and gaskets is a crucial step in the Assembly stage of the installation process for injection quills manufactured in India. The goal of this step is to provide a secure and leak-free connection between the process line and the injection quill.
Nuts and gaskets are typically used to connect the injection quill to the process line by creating a seal around the opening in the process line where the quill will be inserted. The specific types of nuts and gaskets used will depend on the manufacturer’s specifications and guidelines for the specific type of injection quill being installed, as well as the type of process line and the materials used.
To install the nuts and gaskets, the nuts and gaskets are positioned in the correct location on the process line and tightened using tools such as wrenches or spanners. It is important to follow the manufacturer’s instructions carefully when installing the nuts and gaskets to ensure a secure and leak-free connection.
Once the nuts and gaskets have been installed, it is important to check for leaks and verify that the connection is secure. This can be done by performing a pressure test or a leak test. If any leaks are found, they must be addressed before the installation can be considered complete.
After the nuts and gaskets have been installed and the connection has been verified to be secure, the next step in the installation process can proceed. However, it is important to take the time to ensure that the nuts and gaskets have been properly installed to prevent leaks and ensure that the injection quill functions as intended.
Verifying proper connections
Verifying proper connections is an important step in the Assembly stage of the installation process for injection quills. The goal of this step is to ensure that the injection quill has been securely and correctly attached to the process line, and that there are no leaks in the connection.
To verify proper connections, a pressure test or a leak test is typically performed. This test will involve applying pressure to the process line and checking for any leaks in the connection between the process line and the injection quill. If there are any leaks found, they must be addressed before the installation can be considered complete.
In addition to checking for leaks, it is also important to verify that the nuts and gaskets have been properly installed and tightened to ensure a secure connection. The tightness of the nuts and gaskets can be checked using a wrench or spanner, and the manufacturer’s specifications and guidelines should be followed when verifying the tightness of the nuts and gaskets.
Once the proper connections have been verified, the installation process can be considered complete. However, it is important to take the time to ensure that all connections have been properly verified to prevent leaks and ensure that the injection quill functions as intended.
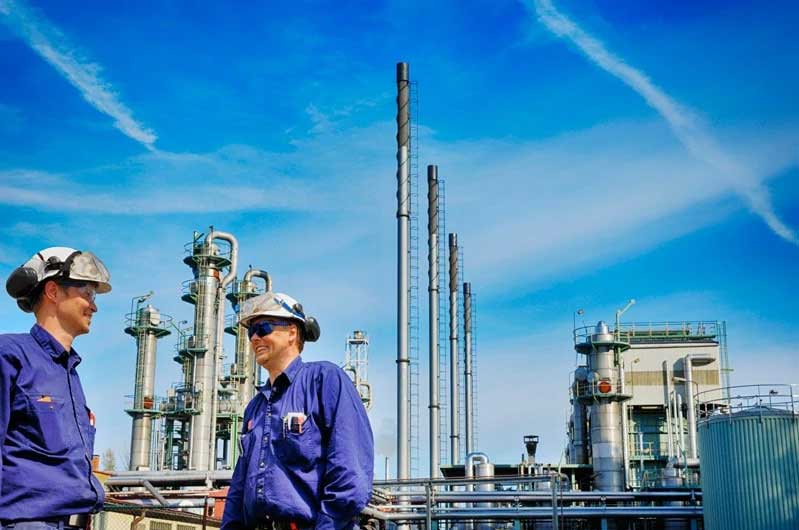
Contact us
Crystal Industrial Syndicate
Phone: +91-22-27563850
Fax: +91-22-67939439
www.crystalindustrial.in
sales@crystalindustrial.in
Crystal Industrial Syndicate from India, manufactures a variety of custom injection quills for a range of industrial processes. Our world-class chemical injection quills are manufactured in India comply with the world’s most stringent certifications. We have clients the world, from Europe and North America to Africa and the Middle East. Please contact us for details about how we can meet your injection quills requirements. Contact us
Copyright © 2023 by Crystal Industrial Syndicate Pvt Ltd. All rights reserved. www.crystalindustrial.in