Surface preparation is the second stage of the installation process for injection quills. During this stage, the following tasks are performed:
- Cleaning the surface area: The surface area where the injection quill will be installed is thoroughly cleaned to ensure a secure and leak-free connection.
- Removing debris and corrosion: Any debris, rust, or corrosion on the surface area is removed to ensure a smooth and even surface for the installation.
- Verifying surface conditions: The surface conditions are checked to ensure that the area is free of any cracks, deformities or other issues that could affect the installation.
The purpose of the surface preparation stage is to create a clean and level surface that will allow for a secure and leak-free installation of the injection quill. This stage is crucial to ensure that the injection quill functions properly and lasts for its expected lifespan.
Cleaning the surface area
Cleaning the surface area is a crucial step in the Surface Preparation stage of the installation process for injection quills. The goal of this step is to remove any dirt, oil, grease, or other contaminants from the surface where the quill will be installed. This is important because any contaminants can interfere with the bonding of the quill to the surface, potentially leading to leaks or other issues. Cleaning the surface can typically be done using solvents or other cleaning agents, and it may involve using a brush or other tool to scrub the surface to ensure that it is thoroughly cleaned. After cleaning, the surface should be allowed to dry completely before the next step in the installation process is carried out.
Removing debris and corrosion
Removing debris and corrosion is a crucial step in the Surface Preparation stage of the installation process for injection quills. The goal of this step is to ensure that the surface where the quill will be installed is free of any debris or corrosion that could interfere with the bonding of the quill to the surface. Debris can include loose materials or particles that could cause blockages or other issues, while corrosion can weaken the surface and reduce its ability to bond with the quill.
To remove debris and corrosion, various tools and techniques may be used, such as wire brushing, sandblasting, or chemical cleaning. It is important to carefully evaluate the surface to determine the best approach for removing debris and corrosion and to follow any manufacturer recommendations for the specific type of injection quill being installed. Once the surface is free of debris and corrosion, it should be thoroughly cleaned and dried before the next step in the installation process is carried out.
Verifying surface conditions
Verifying surface conditions is a crucial step in the Surface Preparation stage of the installation process for injection quills. The goal of this step is to assess the surface where the quill will be installed to ensure that it meets the necessary conditions for successful installation. This includes evaluating the surface for cleanliness, smoothness, and compatibility with the material used for the quill.
To verify surface conditions, various tests and measurements may be performed, such as checking for rough spots, assessing the surface roughness, and measuring the surface temperature. If the surface does not meet the required conditions, additional cleaning or preparation may be needed before the installation can proceed. It is also important to consult the manufacturer’s specifications and guidelines to ensure that the surface is suitable for the specific type of injection quill being installed.
Once the surface conditions have been verified and found to be suitable, the next step in the installation process can proceed. However, if any issues are discovered during the verification process, they must be addressed before the installation can proceed to ensure a successful and long-lasting installation.
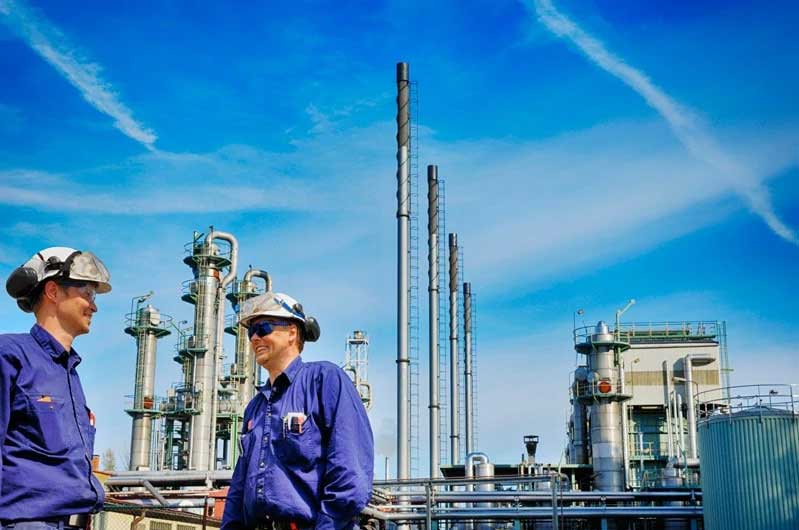
Contact us
Crystal Industrial Syndicate
Phone : +91-22-27563850
Fax: +91-22-67939439
www.crystalindustrial.in
sales@crystalindustrial.in
Crystal Industrial Syndicate from India, manufactures a variety of custom injection quills for a range of industrial processes. Our world-class chemical injection quills are manufactured in India comply with the world’s most stringent certifications. We have clients the world over, from Europe and North America to Africa and the Middle East. Please contact us for details about how we can meet your injection quills requirements. Contact us
Copyright © 2023 by Crystal Industrial Syndicate Pvt Ltd. All rights reserved. www.crystalindustrial.in