The key stages in the installation process for injection quills manufactured in India are:
- Preparation: Selecting the appropriate injection quill and determining the proper location for installation.
- Surface preparation: Cleaning the surface area where the injection quill will be installed.
- Cut-out and drilling: Cutting a hole in the pipe for the injection quill and drilling a hole in the pipe wall for the process line.
- Assembly: Attaching the injection quill to the process line and installing the nuts and gaskets.
- Leak testing: Testing the injection quill for any leaks.
- Startup: Starting up the process line and monitoring the injection quill for proper operation.
- Commissioning: Completing the final checks, documentation, and certification of the injection quill installation.
Preparation
Preparation is the first stage of the installation process for injection quills. During this stage, the following tasks are performed:
- Selection of appropriate injection quill: Based on the process requirements, the correct type and size of the injection quill is selected.
- Determining the proper location: The location for the installation of the injection quill is determined based on factors such as process flow, accessibility, and safety.
- Verifying the necessary tools and materials: A checklist of tools and materials required for the installation is prepared to ensure that everything needed is available.
The purpose of the preparation stage is to ensure that the correct injection quill is selected and that the installation location and necessary tools and materials are ready before the installation begins. This stage lays the foundation for a smooth and successful installation.
Click here for details of the PREPARATION process
Surface preparation
Surface preparation is the second stage of the installation process for injection quills. During this stage, the following tasks are performed:
- Cleaning the surface area: The surface area where the injection quill will be installed is thoroughly cleaned to ensure a secure and leak-free connection.
- Removing debris and corrosion: Any debris, rust, or corrosion on the surface area is removed to ensure a smooth and even surface for the installation.
- Verifying surface conditions: The surface conditions are checked to ensure that the area is free of any cracks, deformities or other issues that could affect the installation.
The purpose of the surface preparation stage is to create a clean and level surface that will allow for a secure and leak-free installation of the injection quill. This stage is crucial to ensure that the injection quill functions properly and lasts for its expected lifespan.
Click here for details of the SURFACE PREPARATION process
Cut-out and drilling
Cut-out and drilling is the third stage of the installation process for injection quills. During this stage, the following tasks are performed:
- Cutting a hole in the pipe: A hole is cut in the pipe at the determined location for the injection quill.
- Drilling a hole in the pipe wall: A hole is drilled in the pipe wall for the process line to pass through and connect to the injection quill.
- Verifying hole size and location: The size and location of the holes are verified to ensure that the injection quill and process line will fit and connect properly.
The purpose of the cut-out and drilling stage is to create the necessary openings in the pipe for the injection quill and process line to be installed. This stage is critical in ensuring that the injection quill is correctly positioned and connected to the process line.
Click here for details of the CUT-OUT AND DRILLING process
Assembly
Assembly is the fourth stage of the installation process for injection quills. During this stage, the following tasks are performed:
- Attaching the injection quill to the process line: The injection quill is attached to the process line and securely fastened.
- Installing nuts and gaskets: The appropriate nuts and gaskets are installed to ensure a leak-free connection between the injection quill and the process line.
- Verifying proper connections: The connections are checked to ensure that the injection quill is securely attached to the process line and that there are no leaks.
The purpose of the assembly stage is to connect the injection quill to the process line and ensure that the connection is secure and leak-free. This stage is crucial to ensure that the injection quill functions properly and that the process line is protected from any leaks.
Click here for details of the ASSEMBLY process
Leak testing
Leak testing is the fifth stage of the installation process for injection quills. During this stage, the following tasks are performed:
- Testing the injection quill for leaks: The injection quill is tested for any leaks using appropriate techniques such as pressure testing or visual inspection.
- Verifying proper operation: The injection quill is checked for proper operation, including proper flow rate, pressure, and temperature.
- Resolving any issues: If any leaks or other issues are detected, appropriate corrective action is taken to resolve them.
The purpose of the leak testing stage is to verify that the injection quill is properly installed and functioning without any leaks. This stage is important to ensure the safety and efficiency of the process line and to prevent any potential harm to the environment or equipment.
Click here for details of the LEAK TESTING process
Startup
Startup is the sixth stage of the installation process for injection quills. During this stage, the following tasks are performed:
- Starting up the process line: The process line is started up and the injection quill is integrated into the process.
- Monitoring the injection quill: The injection quill is monitored for proper operation, including proper flow rate, pressure, and temperature.
- Verifying proper operation: The injection quill is checked for proper operation and any issues are identified and resolved.
The purpose of the startup stage is to bring the injection quill into operation as part of the process line. This stage is critical to ensure that the injection quill is functioning properly and that the process line is running smoothly and efficiently.
Click here for details of the STARTUP process
Commissioning
Commissioning is the seventh and final stage of the installation process for injection quills. During this stage, the following tasks are performed:
- Final inspection: A final inspection of the installation is conducted to ensure that all components are properly installed and functioning.
- Documentation: All relevant documentation, including installation and test reports, is completed and filed.
- Training: Any necessary training is provided to the operating personnel on the proper use and maintenance of the injection quill.
- Handover: The installation is handed over to the operating personnel for ongoing use and maintenance.
The purpose of the commissioning stage is to complete the installation process, verify that the injection quill is properly installed and functioning, and prepare the installation for ongoing use and maintenance. This stage is critical to ensure that the injection quill is integrated into the process line smoothly and that the process line is running efficiently.
Click here for details of the STARTUP process
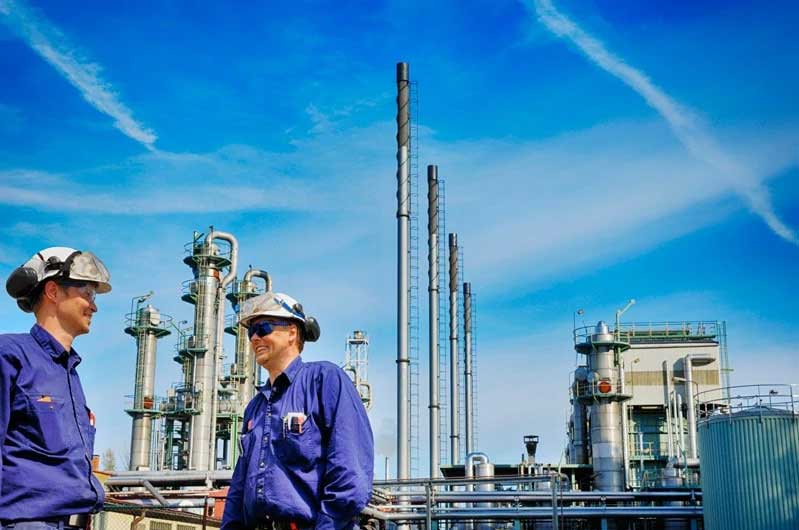
Contact us
Crystal Industrial Syndicate
Phone : +91-22-27563850
Fax: +91-22-67939439
www.crystalindustrial.in
sales@crystalindustrial.in
Crystal Industrial Syndicate from India, manufactures a variety of custom injection quills for a range of industrial processes. Our world-class chemical injection quills are manufactured in India comply with the world’s most stringent certifications. We have clients the world, from Europe and North America to Africa and the Middle East. Please contact us for details about how we can meet your injection quills requirements. Contact us
Copyright © 2023 by Crystal Industrial Syndicate Pvt Ltd. All rights reserved. www.crystalindustrial.in