Common problems with injection quills include clogging, corrosion, and improper installation. Here are some ways to fix these issues:
- Clogging: To prevent clogging, use a strainer at the inlet of the quill and clean the quill regularly. In case of severe clogging, removing the quill and cleaning it with a solvent may be necessary.
- Corrosion: To prevent corrosion, use materials that are compatible with the fluid being injected and the environment in which the quill is installed. Regular inspection and maintenance can help identify and fix corrosion problems early on.
- Improper installation: Improper installation can cause leaks, reduced flow, and other issues. To fix these problems, follow the manufacturer’s instructions and guidelines for proper installation and use.
It’s important to address these problems as soon as they arise to ensure the proper functioning of the injection quill and to avoid any potential harm to the process or the environment.
Clogging
Clogging in injection quills is a common problem that occurs when solid particles or debris accumulate in the quill, blocking or reducing the flow of fluid. This can lead to reduced performance, lower process efficiency, and increased downtime. Clogging can be caused by a variety of factors, such as using low-quality fluid, not using a strainer, and not regularly cleaning the quill.
To prevent clogging, it’s important to use high-quality fluid that is free of contaminants, and to use a strainer at the inlet of the quill to catch any larger particles. Regular cleaning of the quill, either by flushing with solvent or by removing and cleaning the quill itself, can also help to prevent clogging. In the event of severe clogging, removing the quill and cleaning it with a solvent may be necessary.
Overall, clogging in injection quills can have a significant impact on process efficiency and performance, and it’s important to take steps to prevent and address this problem in order to maintain the proper functioning of the injection quill.
Corrosion
Corrosion in injection quills can be a significant problem, as it can cause degradation of the quill and surrounding components, leading to reduced performance and potential failure. Corrosion can be caused by a variety of factors, including exposure to corrosive fluids and harsh environments, using materials that are not compatible with the fluid being injected, and improper installation.
To prevent corrosion in injection quills, it’s important to use materials that are compatible with both the fluid being injected and the environment in which the quill is installed. Regular inspection and maintenance can help to identify and address potential corrosion issues early on. In some cases, using protective coatings or linings can also help to prevent corrosion.
In the event that corrosion has already occurred, repairing or replacing the corroded components may be necessary. It’s important to address corrosion promptly in order to prevent further damage and maintain the proper functioning of the injection quill.
Overall, corrosion can have a significant impact on the performance and lifespan of injection quills, and it’s important to take steps to prevent and address this issue in order to maintain their proper functioning.
Improper installation
Improper installation of injection quills can lead to a variety of problems, such as leaks, reduced flow, and reduced performance. Improper installation can be caused by a variety of factors, including not following the manufacturer’s instructions and guidelines, incorrect positioning, and inadequate tightening of connections.
To prevent improper installation, it’s important to follow the manufacturer’s instructions and guidelines for proper installation and use. This may include ensuring that the quill is positioned correctly and that all connections are tightened properly. Regular inspection and maintenance can help to identify and address potential installation issues early on.
In the event of improper installation, fixing the issue may involve adjusting the position of the quill, tightening connections, or replacing components as needed. It’s important to address improper installation promptly in order to prevent further damage and maintain the proper functioning of the injection quill.
Overall, improper installation of injection quills can have a significant impact on their performance and longevity, and it’s important to take steps to prevent and address this issue in order to ensure their proper functioning.
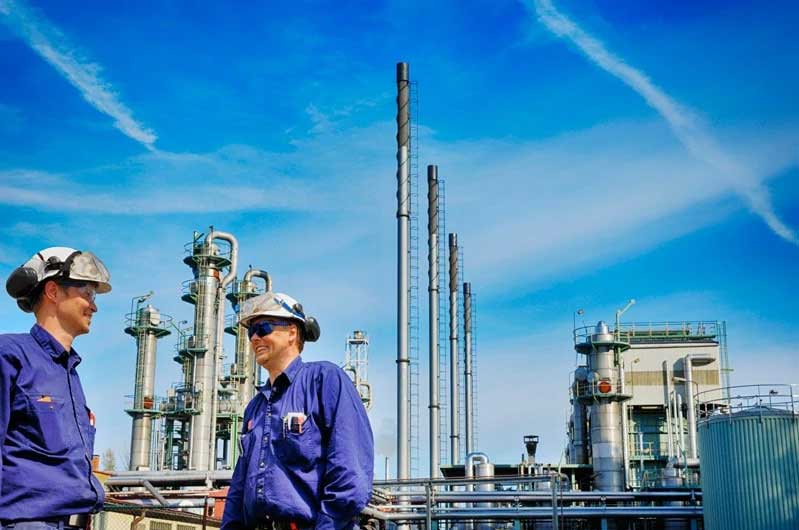
Contact us
Crystal Industrial Syndicate
Phone : +91-22-27563850
Fax: +91-22-67939439
www.crystalindustrial.in
sales@crystalindustrial.in
Crystal Industrial Syndicate from India, manufactures a variety of custom injection quills for a range of industrial processes. Our world-class chemical injection quills are manufactured in India comply with the world’s most stringent certifications. We have clients the world, from Europe and North America to Africa and the Middle East. Please contact us for details about how we can meet your injection quills requirements. Contact us
Copyright © 2023 by Crystal Industrial Syndicate Pvt Ltd. All rights reserved. www.crystalindustrial.in