Chemicals are often put into pipelines, storage tanks, and other process equipment with the help of chemical injection quills. Chemical injection quills are helpful in some of the following industries:
Oil & Gas industry: In the oil and gas industry, corrosion inhibitors, biocides, and other chemicals are put into pipelines and process equipment with the help of chemical injection quills. This keeps the equipment from rusting and keeps it working properly.
Power generation industry: In the power generation industry, chemical injection quills are used to put chemicals into boilers, cooling towers, and other process equipment to keep systems running well, decrease downtime, and make equipment last longer.
Water treatment industry: In the water treatment industry, chemical injection quills are used to put water treatment chemicals like chlorine and hydrogen peroxide into pipelines, storage tanks, and treatment systems to keep the water clean and keep its quality.
Food and beverage industry: Chemical injection quills are used in the food and beverage industry to put chemicals like sanitizers and cleaning agents into pipelines and process equipment to keep things clean and make sure the food and beverage products are of good quality.
Pulp and paper industry: Chemical injection quills are used in the pulp and paper industry to put chemicals, such as process aids, into pipelines and process equipment. This makes the production process more efficient and improves the quality of the final product.
These are just a few examples of processes where chemical injection quills are helpful. Chemical injection quills can help to make production processes more efficient, cut down on downtime, extend the life of equipment, and keep the quality of the products and systems being used.
India manufactures injection quills that help the oil and gas industry
In the oil and gas business, injection quills are a very important tool that are used to put chemicals into pipelines, storage tanks, and other process equipment. Using injection quills has a number of benefits for the business world, such as:
- Corrosion Control: Controlling and stopping corrosion is one of the most important benefits of injection quills in the oil and gas industry. By adding corrosion inhibitors, biocides, and other chemicals to pipelines and process equipment, it is possible to keep the equipment’s integrity and avoid costly breakdowns and downtime.
- Increased efficiency: Injection quills can also help make the process of making oil and gas more efficient. By putting chemicals into the pipelines and process equipment, the flow of oil and gas can be improved. This cuts down on downtime and makes more oil and gas.
- Reduced downtime: Downtime can be cut down with the help of injection quills in the oil and gas industry. By putting chemicals into the pipelines and process equipment, workers don’t have to do as much manual maintenance and cleaning. This cuts downtime and boosts production.
- Better safety: Using injection quills can also help make the oil and gas business safer. By automating the way chemicals are put into pipelines and process equipment, mistakes made by people are less likely to happen. This makes workers safer and reduces the chance of accidents.
- Compliance with rules: Injection quills can also help oil and gas companies follow rules about how chemicals are handled and put into pipelines and other process equipment. By using injection quills, companies can make sure they are following all rules and regulations. This makes it less likely that they will get fines or other penalties.
In the oil and gas industry, injection quills can also help extend the life of pipelines and process equipment. By adding chemicals to the equipment on a regular basis, the need for manual maintenance and cleaning is cut down. This lowers the risk of equipment failure and makes the equipment last longer.
In conclusion, the oil and gas industry can benefit from the use of injection quills in many ways, such as controlling and preventing corrosion, increasing efficiency, reducing downtime, making safety better, and following rules. By using injection quills, oil and gas companies can improve their operations and make more oil and gas. This leads to lower costs and a better bottom line.
India manufactures injection quills that help the power generation industry
In the power generation industry, injection quills are an important tool that are used to put chemicals into pipes, boilers, and other process equipment. Using injection quills has a number of benefits for the power generation business, such as:
Controlling corrosion: In the power generation industry, one of the main benefits of injection quills is that they can be used to control and stop corrosion. By adding corrosion inhibitors, biocides, and other chemicals to boilers and other process equipment, it is possible to keep the equipment in good shape and avoid costly breakdowns and downtime.
Efficiency: Injection quills can also help make the process of making power more efficient. By adding chemicals to boilers and other process equipment, the flow of water and steam can be improved. This cuts down on downtime and boosts output.
Reducing downtime: Downtime can be cut down with the help of injection quills in the power generation industry. By putting chemicals into boilers and other process equipment, people don’t have to clean and fix them by hand as much, which cuts downtime and boosts production.
Improving safety: Safety is also improved when injection quills are used in the power generation industry. By automating the way chemicals are put into boilers and other process equipment, mistakes made by people are less likely to happen. This makes workers safer and reduces the chance of accidents.
Compliance with rules: Injection quills can also help companies that make power follow rules about how chemicals are handled and put into boilers and other process equipment. By using injection quills, companies can make sure they are following all rules and regulations. This makes it less likely that they will get fines or other penalties.
In the power generation industry, injection quills can also help extend the life of boilers and process equipment. By adding chemicals to the equipment on a regular basis, the need for manual maintenance and cleaning is cut down. This lowers the risk of equipment failure and makes the equipment last longer.
In conclusion, the use of injection quills in the power generation industry has many benefits, such as controlling and preventing corrosion, improving efficiency, cutting down on downtime, making things safer, and making sure rules are followed. By using injection quills, companies that make power can improve their operations and make more power. This cuts costs and makes the bottom line better.
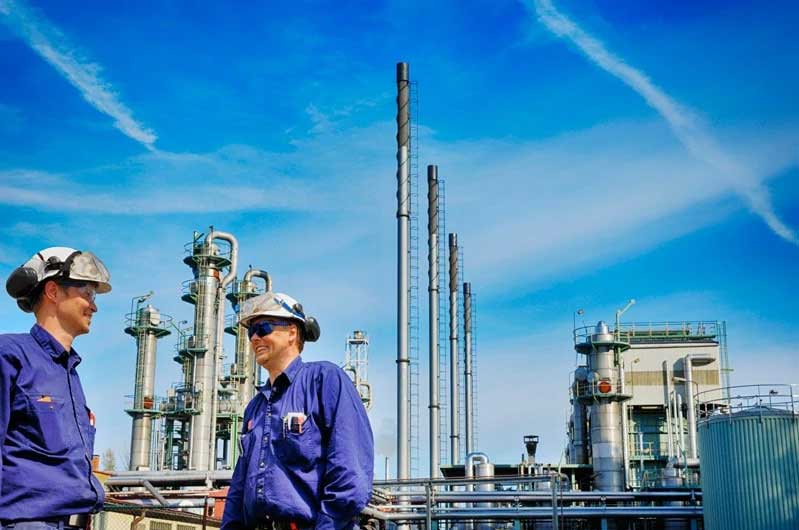
Contact us
Crystal Industrial Syndicate
Phone : +91-22-27563850
Fax: +91-22-67939439
www.crystalindustrial.in
sales@crystalindustrial.in
Crystal Industrial Syndicate from India, manufactures a variety of custom injection quills for a range of industrial processes. Our world-class chemical injection quills are manufactured in India comply with the world’s most stringent certifications. We have clients the world, from Europe and North America to Africa and the Middle East. Please contact us for details about how we can meet your injection quills requirements. Contact us
Copyright © 2023 by Crystal Industrial Syndicate Pvt Ltd. All rights reserved. www.crystalindustrial.in