Direct steam injection quills manufactured in India are devices that are used to inject steam into a process or pipeline in a controlled and precise manner. They are typically used in industries such as food and beverage, chemical processing, and pharmaceuticals, where the controlled injection of steam is critical to the production process.
Direct steam injection quills work by introducing steam directly into the fluid stream through a series of nozzles or orifices. The steam is injected at a high velocity, creating a turbulent mixing zone that rapidly heats the fluid.
The quill is designed to provide precise and consistent steam injection, ensuring that the temperature of the fluid is maintained within a specified range. This is critical to ensure that the product is processed correctly and to maintain the quality of the final product.
Direct steam injection quills manufactured in India can be made from a variety of materials, depending on the requirements of the application. They are typically made from materials that are resistant to corrosion and erosion, and can withstand high temperatures and pressures.
Direct steam injection quills offer several advantages, including their ability to provide precise and consistent temperature control, their ease of installation and maintenance, and their ability to reduce processing time and improve efficiency. They are commonly used in applications such as heating liquids, pasteurization, and sterilization.
Advantages of Direct steam injection quills manufactured in India
Direct steam injection quills offer several advantages for various industrial applications. Here are some of the advantages and an overview of each:
- Efficient heating: Direct steam injection quills provide an efficient way to heat liquids. The steam is injected directly into the liquid, which provides quick and even heating, eliminating the need for external heat exchangers. This process can also be controlled, allowing precise temperature control.
- Reduced energy costs: As direct steam injection quills heat liquids more efficiently, less energy is required to reach and maintain the desired temperature. This can result in significant energy savings over time, reducing overall energy costs for industrial processes.
- Improved process control: Direct steam injection quills allow for better process control, as the amount of steam injected can be adjusted to achieve the desired temperature and flow rate. This can help to ensure consistent product quality and reduce the risk of product defects.
- Reduced processing time: Direct steam injection quills can reduce processing time for certain industrial applications. This is due to the rapid and even heating provided by the steam injection, which can speed up processing times and increase overall production efficiency.
- Reduced maintenance costs: Direct steam injection quills are relatively simple in design and do not have moving parts, making them easy to maintain. This can reduce maintenance costs and downtime for industrial processes.
- Versatile application: Direct steam injection quills can be used in a variety of industrial applications, including heating, cooking, mixing, and sterilization. They are commonly used in the food and beverage industry, chemical processing, and pharmaceuticals.
Overall, direct steam injection quills offer several advantages for industrial processes, including efficient heating, reduced energy costs, improved process control, reduced processing time, reduced maintenance costs, and versatile application.
Disadvantages of Direct steam injection quills manufactured in India
While Direct steam injection quills offer several advantages, they also have some disadvantages to consider. Here are some of the disadvantages and an overview of each:
- Limited to certain liquid viscosities: Direct steam injection quills are typically best suited for low to medium viscosity liquids. They may not be as effective for highly viscous liquids or slurries, which may require a different type of heating equipment.
- Risk of scorching or burning: Direct steam injection quills can be difficult to control and may cause scorching or burning of the liquid if too much steam is injected or if the injection is not properly controlled. This can result in off-flavors, reduced product quality, and even safety hazards.
- Limited steam pressure: Direct steam injection quills may be limited by the amount of steam pressure available. Higher steam pressures may be required for certain industrial processes, which may not be achievable with a direct steam injection system.
- Maintenance requirements: While direct steam injection quills are generally easy to maintain, they do require regular cleaning to prevent fouling and scaling. This can add to the maintenance requirements of industrial processes.
- Initial cost: Direct steam injection quills can be expensive to install initially. This may be a barrier for some industrial processes with limited budgets or cost constraints.
- Energy inefficiency: While direct steam injection quills can be energy-efficient, they can also be energy-inefficient if not properly controlled. Overuse of steam or poor control of steam injection can lead to higher energy costs over time.
Overall, while direct steam injection quills offer several advantages, they also have some disadvantages to consider. These include limitations in liquid viscosity, the risk of scorching or burning, limited steam pressure, maintenance requirements, initial cost, and energy inefficiency. It is important to carefully evaluate the specific needs and requirements of each industrial process before selecting a heating system, including direct steam injection quills.
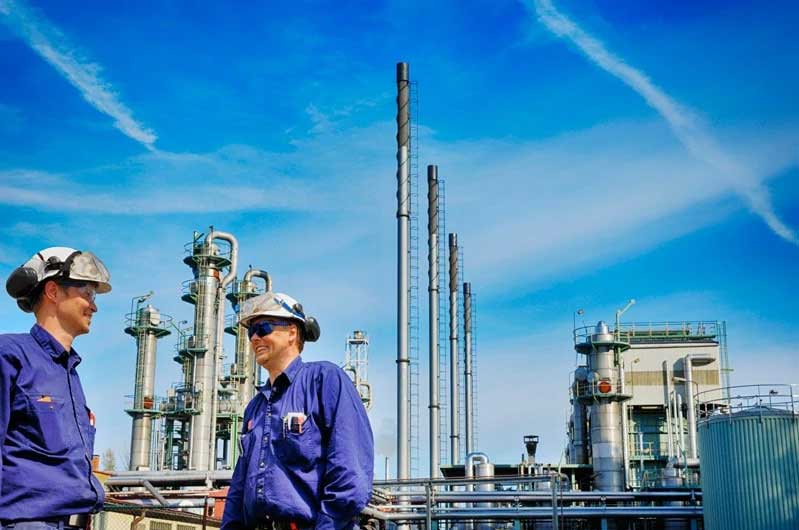
Contact us
Crystal Industrial Syndicate
Phone : +91-22-27563850
Fax: +91-22-67939439
www.crystalindustrial.in
sales@crystalindustrial.in
Crystal Industrial Syndicate from India, manufactures a variety of custom injection quills for a range of industrial processes. Our world-class chemical injection quills are manufactured in India comply with the world’s most stringent certifications. We have clients around the world, from Europe and North America to Africa and the Middle East. Please contact us for details about how we can meet your injection quills requirements. Contact us
Copyright © 2023 by Crystal Industrial Syndicate Pvt Ltd. All rights reserved. www.crystalindustrial.in