What is the purpose of injection quill in piping?
The purpose of an injection quill in piping systems is to introduce chemicals, such as disinfectants or corrosion inhibitors, into the pipeline at a specific location. The quill is inserted into the pipeline and the chemicals are injected through it, allowing for a controlled and precise application. This can help to maintain the integrity of the pipeline, prevent corrosion, and control the growth of microorganisms, among other benefits. Injection quills are often used in industrial settings, such as in water treatment plants or oil and gas facilities.
Give a real-world example of successful injection quill in piping?
One example of a successful injection quill project in an industrial setting was the installation of a quill system in a petrochemical refinery. The refinery was experiencing corrosion in their crude oil piping system, which was causing leaks and equipment failure. The company implemented an injection quill system that injected a corrosion inhibitor into the crude oil stream at specific intervals. The corrosion inhibitor coated the inside of the pipes, preventing corrosion and extending the life of the piping system. The quill system was able to accurately and consistently deliver the corrosion inhibitor, resulting in a significant reduction in equipment failures and maintenance costs for the refinery.
What are the benefits and cost savings achieved through the use of injection quills in piping systems?
The benefits of using injection quills in piping systems include:
- Increased equipment life: Injection quills can be used to inject corrosion inhibitors or other chemicals into the piping system, which can help prevent corrosion and extend the life of the equipment.
- Reduced maintenance costs: By extending the life of the equipment, injection quills can help reduce the need for costly repairs and maintenance.
- Improved process efficiency: Injection quills can also be used to inject chemicals that improve the efficiency of a process, such as a quill to inject a pH adjuster in water treatment plant.
- Accurate chemical dosing: Injection quills can deliver chemicals at very specific intervals and in precise amounts, ensuring that the correct amount of chemical is used.
- Easy retrofit: Injection quills can be easily retrofitted into existing piping systems, making them a cost-effective solution for upgrading older systems.
In terms of cost savings, the use of injection quills can lead to significant reductions in equipment failures, maintenance costs, and downtime. Additionally, the improved process efficiency and accurate chemical dosing can lead to cost savings in the form of reduced chemical usage and increased production output.
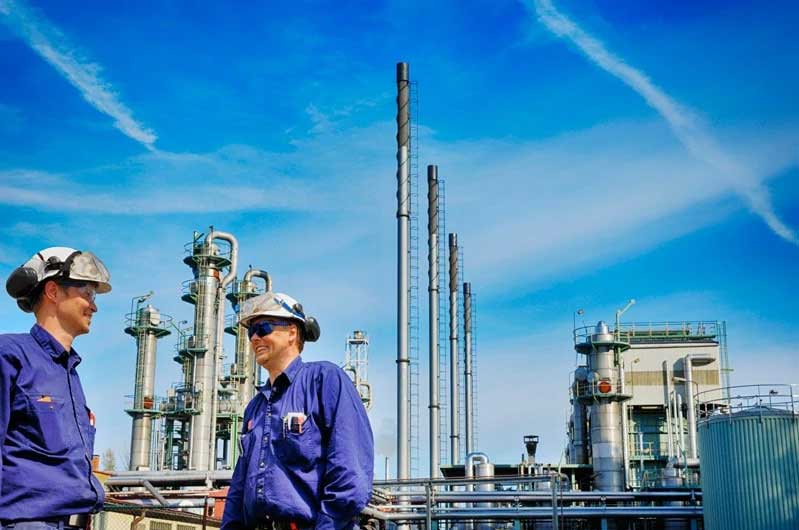
Contact us
Crystal Industrial Syndicate Pvt Ltd.
Telephone : +91-22-27563850 |
Telefax : +91-22-67939439
sales@crystalindustrial.in
Crystal Industrial Syndicate from India, manufactures a variety of custom injection quills for a range of industrial processes. Our world-class chemical injection quills are manufactured in India comply with the world’s most stringent certifications. We have clients the world, from Europe and North America to Africa and the Middle East. Please contact us for details about how we can meet your injection quills requirements. Contact us
Copyright © 2023 by Crystal Industrial Syndicate Pvt Ltd. All rights reserved. www.crystalindustrial.in