Purpose of back pressure valve in chemical injection quills
The purpose of back pressure valves in chemical injection quills is to regulate the flow of fluid back into the chemical injection system, preventing contamination and protecting the system from overpressure. The valve helps maintain a consistent and safe pressure level, ensuring accurate chemical injection and protecting equipment from damage.
Types of back pressure valves
There are several types of back pressure valves used in chemical injection quills, including:
- Spring-loaded check valves
- Ball check valves
- Diaphragm check valves
- Pilot-operated check valves
- Globe valves
Spring-loaded check valves
Spring-loaded check valves are one of the most common types of back pressure valves used in chemical injection quills. They consist of a valve body, a spring, and a ball or disc that seals the valve. The valve opens when the pressure in the system exceeds the force of the spring, allowing fluid to flow through the valve. When the pressure decreases, the spring pushes the ball or disc against the valve seat, sealing the valve and preventing fluid from flowing back into the system.
One of the key advantages of spring-loaded check valves is their simplicity and reliability. They have few moving parts and require minimal maintenance, making them a popular choice for many chemical injection applications. They are also relatively inexpensive compared to other types of back pressure valves.
However, spring-loaded check valves are limited in their ability to regulate pressure and can be prone to leakage if the spring becomes worn or damaged. They are also limited in their ability to handle high flow rates, so they may not be the best choice for applications with high fluid velocity.
Overall, spring-loaded check valves are a good choice for many chemical injection applications, especially when simple, reliable, and low-cost solutions are desired.
Ball check valves
Ball check valves are another type of back pressure valve used in chemical injection quills. They consist of a valve body, a ball, and a seat. The ball is free to move within the valve body and seals the valve by resting against the seat. When fluid flows through the valve in the proper direction, the ball is lifted off the seat and fluid is allowed to pass. When the flow reverses, the ball falls back onto the seat, sealing the valve and preventing fluid from flowing back into the system.
Ball check valves are commonly used in chemical injection applications that require high flow rates and higher pressures. The ball design allows for larger fluid passages, reducing fluid turbulence and reducing the risk of valve damage. Ball check valves also have a fast response time and can effectively regulate pressure in the system.
One of the disadvantages of ball check valves is that they require more space than other types of back pressure valves. They also have more moving parts, which can make them more prone to wear and failure. Ball check valves can also be more expensive than other types of back pressure valves.
Overall, ball check valves are a good choice for chemical injection applications that require high flow rates and higher pressures, and where space is not a concern. They are reliable and effective at regulating pressure, but require more maintenance and are more expensive than other types of back pressure valves.
Diaphragm check valves
Diaphragm check valves are a type of back pressure valve used in chemical injection quills. They consist of a valve body, a diaphragm, and a seat. The diaphragm is a flexible barrier that separates the fluid from the valve’s moving parts, preventing contamination and protecting the system from corrosive fluids. When fluid flows through the valve in the proper direction, the diaphragm moves, allowing fluid to pass. When the flow reverses, the diaphragm returns to its original position, sealing the valve and preventing fluid from flowing back into the system.
Diaphragm check valves are commonly used in chemical injection applications that involve corrosive or abrasive fluids, as the diaphragm provides a barrier that prevents fluid from coming into contact with the valve’s moving parts. They are also effective at regulating pressure, making them a good choice for applications where consistent pressure is required.
One of the disadvantages of diaphragm check valves is that they can be more expensive than other types of back pressure valves. They also have more moving parts and require more maintenance, as the diaphragm may need to be replaced if it becomes damaged or worn.
Overall, diaphragm check valves are a good choice for chemical injection applications that involve corrosive or abrasive fluids. They are effective at regulating pressure and protecting the system from contamination, but are more expensive and require more maintenance than other types of back pressure valves.
Pilot-operated check valves
Pilot-operated check valves are a type of back pressure valve used in chemical injection quills. They consist of a main valve and a pilot valve that controls the main valve. The pilot valve is a smaller valve that is operated by the fluid pressure in the system. When fluid flows through the valve in the proper direction, the pilot valve opens, allowing fluid to pass through the main valve. When the flow reverses, the pilot valve closes, sealing the main valve and preventing fluid from flowing back into the system.
Pilot-operated check valves are commonly used in chemical injection applications that require precise control over pressure. The pilot valve provides a sensitive control mechanism, allowing the main valve to be opened and closed with a high degree of accuracy. This makes pilot-operated check valves a good choice for applications where consistent pressure is required.
One of the disadvantages of pilot-operated check valves is that they are more complex than other types of back pressure valves, with more moving parts that can be prone to wear and failure. They also require more maintenance, as the pilot valve may need to be serviced or replaced if it becomes damaged or worn.
Overall, pilot-operated check valves are a good choice for chemical injection applications that require precise control over pressure. They are effective at regulating pressure, but are more complex and require more maintenance than other types of back pressure valves.
Globe valves
Globe valves are a type of back pressure valve used in chemical injection quills. They consist of a valve body, a disc, and a stem. The disc is mounted on the stem and seals the valve by pressing against the valve seat. The stem is connected to a hand wheel or lever, which can be used to adjust the position of the disc and control the flow of fluid through the valve.
Globe valves are commonly used in chemical injection applications that require precise flow control and accurate pressure regulation. The adjustable disc allows for fine-tuning of the flow rate, making it a good choice for applications where consistent pressure is required. Globe valves are also capable of handling high flow rates and high pressures, making them a good choice for demanding applications.
One of the disadvantages of globe valves is that they have a more complex design compared to other types of back pressure valves, which can make them more expensive. They also have more moving parts, which can make them more prone to wear and failure. Globe valves also require more maintenance than other types of back pressure valves, as the stem and disc may need to be lubricated or replaced over time.
Overall, globe valves are a good choice for chemical injection applications that require precise flow control and accurate pressure regulation. They are capable of handling high flow rates and high pressures, but are more expensive and require more maintenance than other types of back pressure valves.
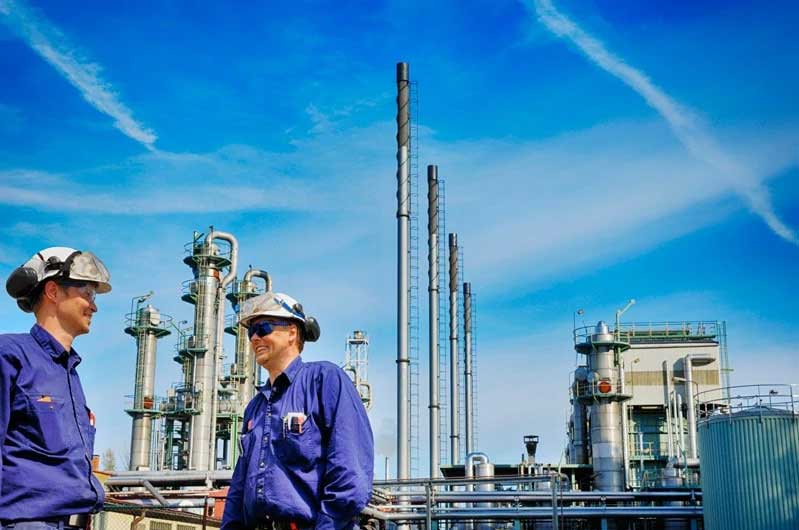
Contact us
Crystal Industrial Syndicate Pvt Ltd.
Telephone : +91-22-27563850 |
Telefax : +91-22-67939439
sales@crystalindustrial.in
Crystal Industrial Syndicate from India, manufactures a variety of custom injection quills for a range of industrial processes. Our world-class chemical injection quills are manufactured in India comply with the world’s most stringent certifications. We have clients the world, from Europe and North America to Africa and the Middle East. Please contact us for details about how we can meet your injection quills requirements. Contact us
Copyright © 2023 by Crystal Industrial Syndicate Pvt Ltd. All rights reserved. www.crystalindustrial.in