Chemical injection quills with back pressure valves are used in a range of industries, including:
- Oil and Gas industry
- Water Treatment industry
- Power Generation industry
- Pharmaceutical industry
- Food and Beverage industry
- Chemical Manufacturing
Benefits of back-pressure valves in the power generation industry
Back pressure valves in chemical injection quills used in power generation serve several purposes:
- Boiler Water Treatment: Back pressure valves help to regulate the flow of chemicals used for boiler water treatment. By maintaining consistent pressure, the valves help to ensure the correct amount of chemicals is added to the water supply and prevent over- or under-dosing.
- Cooling Tower Water Treatment: Back pressure valves help to regulate the flow of chemicals used for cooling tower water treatment. By maintaining consistent pressure, the valves help to prevent contamination of the chemical supply and maintain the purity and effectiveness of the chemicals used.
- Corrosion Control: Back pressure valves help to control the flow of chemicals used to prevent corrosion in power generation equipment. By maintaining consistent pressure, the valves help to ensure the efficacy of the corrosion inhibitors and prevent corrosion-related damage to equipment.
- Equipment Protection: Back pressure valves help to protect the pumps and injectors used in chemical injection systems. By preventing backflow, the valves help to prevent damage to equipment and ensure the longevity of the system.
Overall, back pressure valves play a crucial role in maintaining the safety and efficiency of chemical injection systems used in power generation. By regulating fluid flow and maintaining consistent pressure, back pressure valves help to optimize chemical injection processes, prevent contamination and protect equipment from damage and corrosion.
Benefits of back-pressure valves in the pharmaceutical industry
Back pressure valves in chemical injection quills used in the pharmaceutical industry serve several purposes:
- Sterilization: Back pressure valves help to regulate the flow of chemicals used for sterilization in pharmaceutical manufacturing. By maintaining consistent pressure, the valves help to ensure the correct amount of sterilizing agent is added to the system and prevent over- or under-dosing.
- Water Treatment: Back pressure valves help to regulate the flow of chemicals used for water treatment in pharmaceutical manufacturing. By maintaining consistent pressure, the valves help to prevent contamination of the water supply and ensure the purity of the water used in manufacturing processes.
- Corrosion Control: Back pressure valves help to control the flow of chemicals used to prevent corrosion in pharmaceutical manufacturing equipment. By maintaining consistent pressure, the valves help to ensure the efficacy of the corrosion inhibitors and prevent corrosion-related damage to equipment.
- Equipment Protection: Back pressure valves help to protect the pumps and injectors used in chemical injection systems. By preventing backflow, the valves help to prevent damage to equipment and ensure the longevity of the system.
Overall, back pressure valves play a crucial role in maintaining the safety and efficiency of chemical injection systems used in the pharmaceutical industry. By regulating fluid flow and maintaining consistent pressure, back pressure valves help to optimize chemical injection processes, prevent contamination, and protect equipment from damage and corrosion.
Benefits of back-pressure valves in the Food and Beverage industry
Back pressure valves in chemical injection quills used in the food and beverage industry serve several purposes:
- Water Treatment: Back pressure valves help to regulate the flow of chemicals used for water treatment in food and beverage manufacturing. By maintaining consistent pressure, the valves help to prevent contamination of the water supply and ensure the purity of the water used in manufacturing processes.
- Sterilization: Back pressure valves help to regulate the flow of chemicals used for sterilization in food and beverage manufacturing. By maintaining consistent pressure, the valves help to ensure the correct amount of sterilizing agent is added to the system and prevent over- or under-dosing.
- Sanitation: Back pressure valves help to regulate the flow of chemicals used for sanitation in food and beverage manufacturing. By maintaining consistent pressure, the valves help to ensure the efficacy of the sanitation agents and prevent the growth of harmful bacteria or pathogens.
- Equipment Protection: Back pressure valves help to protect the pumps and injectors used in chemical injection systems. By preventing backflow, the valves help to prevent damage to equipment and ensure the longevity of the system.
Overall, back pressure valves play a crucial role in maintaining the safety and efficiency of chemical injection systems used in the food and beverage industry. By regulating fluid flow and maintaining consistent pressure, back pressure valves help to optimize chemical injection processes, prevent contamination, and protect equipment from damage and corrosion.
Benefits of back-pressure valves in Chemical Manufacturing
Back pressure valves in chemical injection quills used in chemical manufacturing serve several purposes:
- Process Control: Back pressure valves help to regulate the flow of chemicals used in various chemical manufacturing processes. By maintaining consistent pressure, the valves help to ensure that the correct amount of chemical is added to the system and prevent over- or under-dosing.
- Reactor Feed: Back pressure valves help to regulate the flow of chemicals into reactors in chemical manufacturing. By maintaining consistent pressure, the valves help to optimize the reaction conditions and ensure the quality of the final product.
- Equipment Protection: Back pressure valves help to protect the pumps and injectors used in chemical injection systems. By preventing backflow, the valves help to prevent damage to equipment and ensure the longevity of the system.
- Safety: Back pressure valves help to prevent the release of hazardous chemicals into the environment in the event of a system failure. By preventing backflow, the valves help to contain chemicals and reduce the risk of exposure to workers and the public.
Overall, back pressure valves play a crucial role in maintaining the safety and efficiency of chemical injection systems used in chemical manufacturing. By regulating fluid flow and maintaining consistent pressure, back pressure valves help to optimize chemical injection processes, prevent contamination, and protect equipment from damage and corrosion.
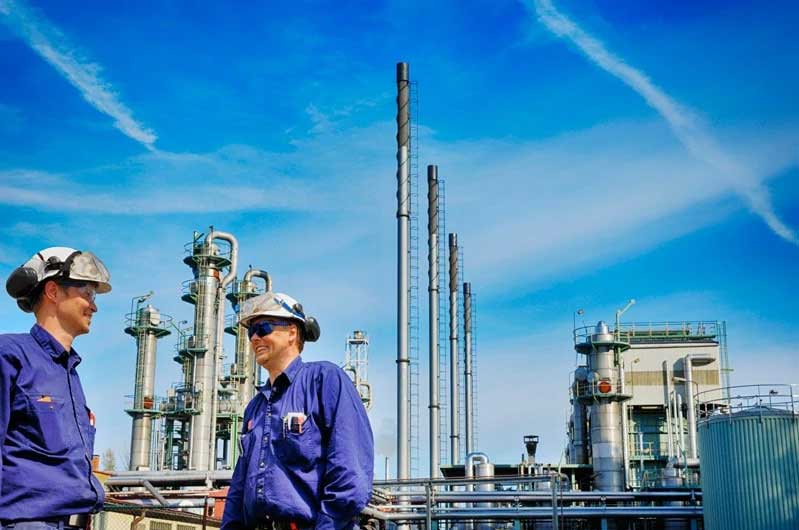
Contact us
Crystal Industrial Syndicate Pvt Ltd.
Telephone : +91-22-27563850 |
Telefax : +91-22-67939439
sales@crystalindustrial.in
Crystal Industrial Syndicate from India, manufactures a variety of custom injection quills for a range of industrial processes. Our world-class chemical injection quills are manufactured in India comply with the world’s most stringent certifications. We have clients the world, from Europe and North America to Africa and the Middle East. Please contact us for details about how we can meet your injection quills requirements. Contact us
Copyright © 2023 by Crystal Industrial Syndicate Pvt Ltd. All rights reserved. www.crystalindustrial.in