The following are some best practices for maintaining and servicing chemical injection quills with back pressure valves:
- Regular Inspection: Regular inspections should be performed to identify any issues with the valve or system. This can help to prevent malfunctions and minimize downtime.
- Cleaning: Back pressure valves should be cleaned regularly to remove any debris that may have accumulated in the valve or system. This can help to prevent clogging and improve valve performance.
- Maintenance: Regular maintenance should be performed to ensure the valve is functioning properly. This can include replacing seals, gaskets, or other components that may have worn or degraded over time.
- Testing: Back pressure valves should be tested regularly to ensure they are functioning properly. This can include a variety of tests such as backflow tests, hydrostatic tests, or performance tests.
- Training: Personnel involved in the maintenance and servicing of chemical injection quills with back pressure valves should receive proper training on the system, valve components, and maintenance procedures.
- Documentation: A comprehensive maintenance and service record should be kept for each valve. This can include information on inspections, cleaning, maintenance, and testing.
Overall, regular inspection, cleaning, maintenance, testing, training, and documentation are key components of a successful maintenance program for chemical injection quills with back pressure valves. By following these best practices, you can help to ensure the safety and reliability of the system and minimize downtime.
Regular Inspection
Regular inspections of chemical injection quills with back pressure valves are an important component of their maintenance program. The goal of regular inspections is to identify any issues with the valve or system that may need attention. During an inspection, the valve and surrounding system should be visually examined for any signs of wear, corrosion, or other signs of damage. In addition, the valve should be tested to ensure it is functioning properly, and to identify any performance issues that may need to be addressed. By performing regular inspections, you can prevent malfunctions, minimize downtime, and ensure the long-term reliability of the system.
Cleaning
Cleaning chemical injection quills with back pressure valves is an important component of their maintenance program. Over time, debris may accumulate in the valve or system, causing clogging or reduced performance. Cleaning the valve and surrounding system can help to prevent these issues and improve valve performance. Cleaning should be performed regularly, depending on the type of fluid being processed and the conditions of the system. In general, cleaning should involve removing any debris that has accumulated in the valve or system, and thoroughly washing the components to remove any residual debris. By cleaning the valve and system, you can help to ensure the safety and reliability of the system and minimize downtime.
Maintenance
Regular maintenance is an important component of maintaining chemical injection quills with back pressure valves. Maintenance can include a variety of tasks, such as replacing worn or degraded components, checking seals, gaskets, and other components for wear, and performing a thorough examination of the valve and surrounding system to identify any issues that may need to be addressed. Maintenance should be performed on a regular basis, depending on the type of fluid being processed and the conditions of the system. By performing regular maintenance, you can help to ensure the safety and reliability of the system and minimize downtime. Regular maintenance can also help to extend the life of the valve and system and improve overall performance.
Testing
Testing chemical injection quills with back pressure valves is an important component of their maintenance program. Testing should be performed on a regular basis to ensure the valve is functioning properly and to identify any performance issues that may need to be addressed. Testing can involve a variety of methods, including visual inspection, pressure testing, and flow testing. By testing the valve, you can verify its performance, identify any issues that may need to be addressed, and ensure the long-term reliability of the system. Testing should be performed by qualified technicians with the appropriate training and experience, and the results should be documented for future reference.
Training
Training is an important component of maintaining and servicing chemical injection quills with back pressure valves. Employees who work with or maintain these valves should be trained on the proper procedures for operating, maintaining, and servicing the valves. Training should include information on the valve’s design, operation, and maintenance requirements, as well as any safety concerns associated with working with the valve. Training can be provided through a variety of methods, including classroom instruction, hands-on training, and online resources. By providing regular training to employees, you can help to ensure that the valve and system are being operated and maintained properly, minimize the risk of malfunctions, and extend the life of the system.
Documentation
Documentation is an important component of maintaining and servicing chemical injection quills with back pressure valves. Documentation should include information on the valve’s design, operation, maintenance requirements, and testing results. This information can be used to track the valve’s performance over time, identify any issues that may need to be addressed, and provide a record of the valve’s maintenance history. Documentation should be updated regularly to reflect any changes to the valve or system, and should be accessible to all employees who work with or maintain the valve. By maintaining accurate and up-to-date documentation, you can help to ensure the safety and reliability of the system and minimize downtime.
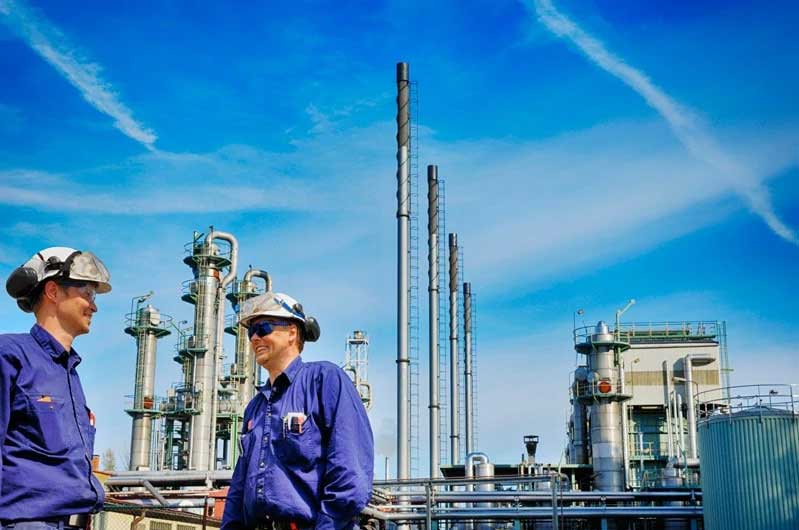
Contact us
Crystal Industrial Syndicate Pvt Ltd.
Telephone : +91-22-27563850 |
Telefax : +91-22-67939439
sales@crystalindustrial.in
Crystal Industrial Syndicate from India, manufactures a variety of custom injection quills for a range of industrial processes. Our world-class chemical injection quills are manufactured in India comply with the world’s most stringent certifications. We have clients the world, from Europe and North America to Africa and the Middle East. Please contact us for details about how we can meet your injection quills requirements. Contact us
Copyright © 2023 by Crystal Industrial Syndicate Pvt Ltd. All rights reserved. www.crystalindustrial.in